A cross-industry group has come together recently in an effort to upgrade trains with 3D printed parts. Currently, components being fabricated via additive manufacturing technology–rather than more conventional methods–include four-passenger armrests and seven grab handles. These have already been installed in Chiltern Railways trains in the UK for a trial run, with research, development, and further coordination by Angel Trains, a leading train leasing company in the UK, 3D printing leader Stratasys (NASDAQ: SSYS), engineering consultancy DB ESG, and the train operators at Chiltern Railways too.
The train parts being created via 3D printing right now are of particular interest because they not only demonstrate the ‘accelerated’ rate at which parts can be manufactured—but these are parts that had become obsolete. With 3D scanning and 3D printing, however, they can be re-created and put back into production. This is critical for industries like trains where machinery may be running for decades but it is not cost-effective to try to track down one part that most distributors no longer sell—unlike car parts which are common and produced in enormous volumes.
As very old parts break down, train companies must be able to replace them quickly no matter what though, maintaining hardware as well as offering the best comfort and customer service possible to those riding trains.
“In recent times, we’ve seen growing concern amongst operators that sourcing replacement parts for older train fleets at a reasonable cost and in a short timeframe is proving increasingly difficult,” explains James Brown, Data and Performance Engineer, Angel Trains.
“The problem is that traditional manufacturing methods only make it cost-effective to produce high volumes of spare parts, even though an operator may only need a few obsolete train parts replaced. In addition, lead times can take months. This is why we have teamed up with DB ESG and Stratasys, showing how operators can overcome these hurdles by using 3D printing to produce the exact amount of parts they need at a fraction of the time and cost of traditional methods,” said Brown.
Brown also explained that parts like the armrest usually take around four months to make with traditional technology; however, they were created in one week (showing a decrease in the production time of nearly 94 percent) via Stratasys FDM 3D printing. Brown also projects a savings of up to 50 percent on parts.
“This is an exciting time for the UK rail industry,” said Brown. “With this technology, train operators can be much more responsive to replacing passenger-facing parts that get damaged or vandalized. A 3D printed replacement part can be produced on-demand and installed immediately. With low-volume production now achievable, we’re also starting to explore how we can leverage 3D printing to customize interiors that are better suited to the passenger commute. For example, we’ve tested 3D printing seat back tables with braille informing the passenger that the toilet is ten rows back from that particular seat.
“This level of customization is unprecedented and can only be enabled by 3D printing, offering the potential to significantly improve both the servicing of trains and the passenger experience in the future.”
The parts were comprehensively tested not only for strength and reliability but also for safety and compliance with UK rail industry standard EN45545-2 for 3D printed parts. Afterward, the final version of the components were printed on a Fortus 450mc Production 3D Printer using ULTEM™ 9085 resin, which is made to stand up to fire, smoke, and toxicity.
“Achieving certification removes a major barrier that has prevented more widespread implementation of 3D printing across UK trains,” said Martin Stevens, Mechanical Engineering Manager DB ESG. “Our role in this project has been to investigate the design, production and finishing of FDM parts, verifying whether the parts comply with rail standards and checking whether they work in the operating environments. We have also optimised the component design of FDM manufacture.”
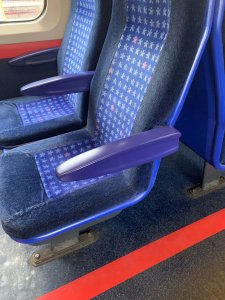
3D printed armrest on Chiltern Railways train – produced 94% faster compared to traditional manufacturing methods
With this project, the group has successfully created a viable and repeatable process, manufacturing 3D printed parts that comply with industry standards and can be used in trains. After receiving such a great response regarding this initial project, the group will be performing another trial of 3D printed parts for the Great Western Railway.
“Having successfully proven the viability of 3D printed parts within trains in the UK, the impact on the traditional rail industry supply chain can be transformative. Train operators can eradicate the issues associated with physical inventories by building a library of digital inventory that can be 3D printed as and when they need it, wherever they need and in the exact quantity required. We are witnessing a new era of true on-demand production with no waste,” concluded Yann Rageul, Head of Strategic Accounts for EMEA at Stratasys.
When it comes to 3D printing today—and transportation, ‘train, planes, and automobiles’ definitely come to mind as so many industrial parts are being printed. Automotive manufacturers like BMW and aerospace leaders like NASA have been using 3D printing and additive manufacturing in their practices for decades, and this technology has begun to play a part in creating and replacing older and newer components for trains around the world too.
What do you think of this news? Let us know your thoughts! Join the discussion of this and other 3D printing topics at 3DPrintBoard.com.
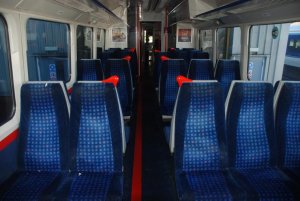
3D printing can help train operators accelerate the replacement of obsolete parts, enabling them to get vehicles back into service quicker and better maintain their trains – improving the quality of service for passengers.
Subscribe to Our Email Newsletter
Stay up-to-date on all the latest news from the 3D printing industry and receive information and offers from third party vendors.
Print Services
Upload your 3D Models and get them printed quickly and efficiently.
You May Also Like
Heating Up: 3D Systems’ Scott Green Discusses 3D Printing’s Potential in the Data Center Industry
The relentless rise of NVIDIA, the steadily increasing pledges of major private and public investments in national infrastructure projects around the world, and the general cultural obsession with AI have...
3DPOD 260: John Hart on VulcanForms, MIT, Desktop Metal and More
John Hart is a Professor at MIT; he´s also the director of the Laboratory for Manufacturing and Productivity as well as the director of the Center for Advanced Production Technologies....
Etsy Design Rule Change Reduces Selection of 3D Printed Goods
Online marketplace Etsy has implemented a rule change requiring all 3D printed goods on the site to be original designs. The update to the site’s Creativity Standards states, ¨Items produced using...
E-Beam OEM Wayland Additive Partners with USC Racing to 3D Print Titanium Exhaust Collector
Every year, standards organization SAE International holds a competition called Formula SAE, in which students from both undergraduate and graduate programs design, build, and race small formula-style race cars. For...