As discussed at Additive Manufacturing Strategies, more advanced software is going to be key to driving the adoption of 3D printing in part by digitizing tribal knowledge, as Todd Grimm put it, so that our design software automatically performs tasks that formerly required hands-on experience with various production technologies to execute manually.
One important piece of that knowledge is understanding how to prevent build failure in metal 3D printing. In fact, even the tribal knowledge associated with avoiding build failure is far from perfect, with trial-and-error being the go-to strategy for successfully producing a metal part. This is where simulation is destined to play a crucial role.
Every variable in the build chamber of a metal powder bed fusion (PBF) system will impact whether a part will come out of the printer as it was designed: the orientation of the component, placement of support structures, scan strategy, laser spot size and more. If that can be accurately simulated and potential issues such as thermal stress and distortion can be accounted for, we can avoid trial and error and produce parts right the first time.
For this reason, ANSYS, Hexagon, VELO3D and more are developing simulation software for metal 3D printing. Autodesk, too, has addressed simulation via Netfabb Local Simulation, acquired by the CAD giant in 2016. Now, the company has begun the process of porting some of Netfabb’s advanced simulation tools into Fusion 360, the company’s popular CAD platform.
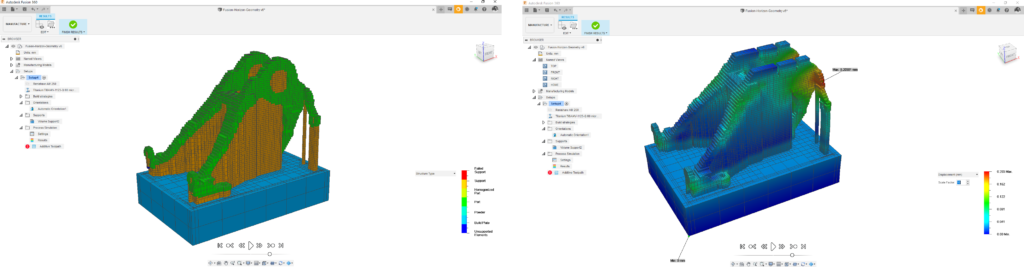
A model is opened in Fusion 360 on the left. On the right, the Simulation Extension shows displacement mid-print. Images courtesy of Autodesk.
Sualp Ozel, Senior Product Manager for 3D printing at Autodesk, joined the firm when ALGOR Inc. was purchased in 2009, bringing with it a host of finite element analysis (FEA) tools. When Netfabb was brought on board in 2016, Ozel switched to the 3D printing team to see how he could apply his expertise in simulation to 3D printing.
As his team improved the simulation capabilities of Netfabb Local Simulation over time, Autodesk set about turning Fusion 360 into a cohesive modeling platform that not only takes care of the design portion of production, but also the actual manufacturing tasks. Now, through various extensions, Fusion 360 can generate toolpaths for CAM and 3D printing, making it possible to go from design to production within a single interface.
At the beginning of this year, that integration grew to include simulation. At the moment, the Additive Simulation Extension for Fusion 360 can simulate laser PBF. Accessing the extension is as easy as clicking a couple of buttons within the software.
When you have a design that you want to print, you select how you want to manufacture the part from the Fusion 360 menu, choose additive manufacturing, the metal you’d like to use, orient the part and add support structures. From that point, you can either slice the file and generate a toolpath for your laser and print it or you can simulate the print procedure to see if it will be successful.
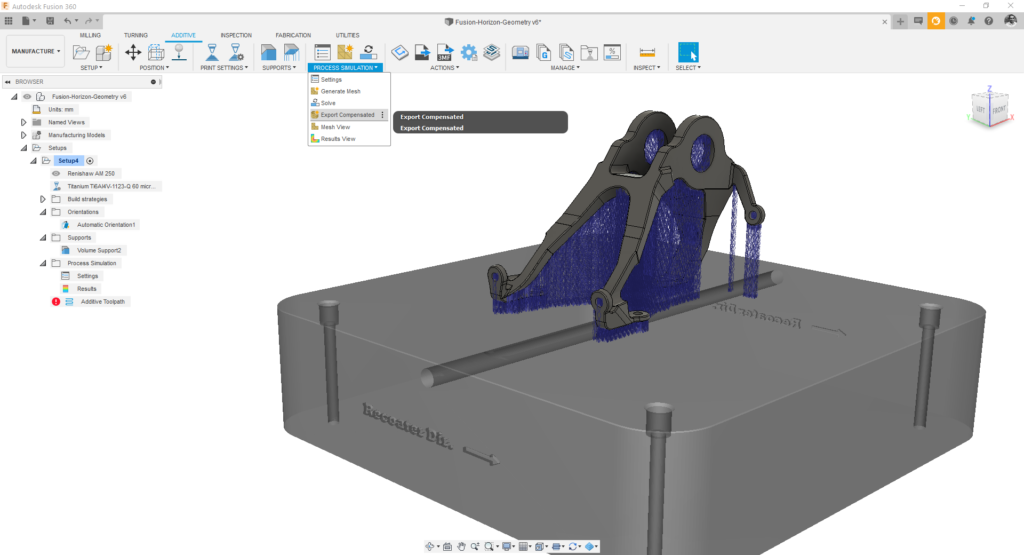
The problematic file has compensation applied to ensure proper printing. Image courtesy of Autodesk.
The software runs on the same solvers and engines as Netfabb Local Simulation, which is a multi-scale thermal-mechanical modeling approach to FEA of the print area. Whereas analyzing the entire laser path across the entire build would take millennia, the software simulated a 1 mm x 1 mm area and scales that up across the print process to estimate how the object will distort and how stress are going to build up.
If it’s going to fail, due to distortion, recoater blade interference or problematic support structures, you can address those issues. That is to say that those are the three problems that Fusion 360 can currently detect with the Additive Simulation Extension. At the moment, the software can then compensate for the distortions that may occur in the part. In the future, however, more features from Netfabb will become available within Fusion 360, such as support and orientation optimization.
As a professor in mechanical engineering at Carnegie Mellon, Ozel pointed out that, not only is simulation increasingly important to outcome success in metal 3D printing, but it’s even aiding in the education of metal 3D printing to engineering students.
“A lot of the education facilities in manufacturing quickly went virtual with COVID. A lot of folks who were 3D printing metal in their labs, wanted to know ‘Hey, how can we explain additive manufacturing, but in a virtual setting?’ And simulation is the first thing that immediately jumps to everyone’s mind. Fusion 360 is very accessible to education. So now with the release of Additive Simulation Extension, those folks can do all the picks and clicks and get all the results out of the box with Fusion 360.”
Now that SLM have been taken care of, the next process that Ozel’s team plans to tackle is directed energy deposition. Simulation is free as a tech preview to commercial and educational users at the moment, though hobbyists can only access FDM, given the likelihood that they do not have their own PBF machines.
Also at the moment, simulation does not run in the cloud and requires the same computing power of FEA generally, which means that you might need a solid amount of RAM if you want to run these simulations quickly. However, the plan is to be able to run this in the cloud when the tool is ready to move beyond tech preview and into commercial release, hopefully this year.
According to Ozel, the most important aspect of the tool is accessibility, which is why cloud-driven simulation will be key.
“At the end of the day, somebody that’s printing something on a metal printer should be able to do a quick check without having to have a PhD in simulation, right?” Ozel said. “I want them to set it up, choose their print settings and hit simulate. Of course, somebody with a little more advanced background can access more advanced settings, but, out of the box, we want it to give some guidance about whether or not the print will succeed, fail and, if it fails, fix it for me.”
From the perspective of someone who is inexperienced with CAD, Fusion 360 always strikes me as the most user friendly of the bunch. Now that simulation is being brought into that friendly environment, it seems as though, not only will metal 3D printing become a more repeatable process, but one that will be accessible to much wider range of users, as well.
Subscribe to Our Email Newsletter
Stay up-to-date on all the latest news from the 3D printing industry and receive information and offers from third party vendors.
Print Services
Upload your 3D Models and get them printed quickly and efficiently.
You May Also Like
The Market and Industry Potential of Multi-Material 3D and 4D Printing in Additive Electronics
Additive manufacturing leverages computer-based software to create components for products by depositing either dielectric or conductive materials, layer by layer, into different geometric shapes. Since its birth in the 1980s,...
3DPOD 262: Bio-inspired Design for AM with Dhruv Bhate, Arizona State University
Dhruv Bhate is an associate professor at Arizona State University. There, he looks at structures, materials, and design. Previously, he worked at PADT as well as in the semiconductor and...
3DPOD 261: Tooling and Cooling for AM with Jason Murphy, NXC MFG
Jason Murphy´s NXC MFG (Next Chapter Manufacturing) is not a generalist service; instead, the company specializes in making tooling. Using LPBF and binder jet, the company produces some of the...
3DPOD 260: John Hart on VulcanForms, MIT, Desktop Metal and More
John Hart is a Professor at MIT; he´s also the director of the Laboratory for Manufacturing and Productivity as well as the director of the Center for Advanced Production Technologies....