Flow is not an industry; it’s not an established vertical; it’s not an established part; it’s not a thing you can buy at Sigma Aldrich or RS Components. Flow is not a market or part that you think of or can get and, yet, flow is one of the fastest-growing areas in 3D printing.
We tend to think of the world through categories and these categories help us because they allow us to organize our thinking and delineate and compare things against one another. Categorization is natural to the mind and helps us see patterns, details, and the bigger picture. But sometimes our automatic ability to see and make boxes and lists from unstructured data also confuses us. With our categorization habit, we obfuscate the important new breakthrough pattern. That which allows us to order the mundane may very well hide the new.
This is why it took me so long to see flow as the biggest new trend in 3D printing. It was only after working on 3D printed manifolds in cars and writing about them for a client in a short span of time that I noticed the trend. Through trying to differentiate the different manifolds—one, the intake manifold supplying air to the car, and the other, an industrial hydraulic part that moves liquid around a system—that I had my “aha Erlebenis“, as they say in Germany. It was actually more of an “expletive deleted” followed by childlike wonder as I exclaimed out loud, “But there’s, like, a lot more air and liquid flowing everywhere…like ev-ry-where.” The aircraft passenger next to me did not immediately share my enthusiasm. Eventually, however, they did—or at least pretended to.
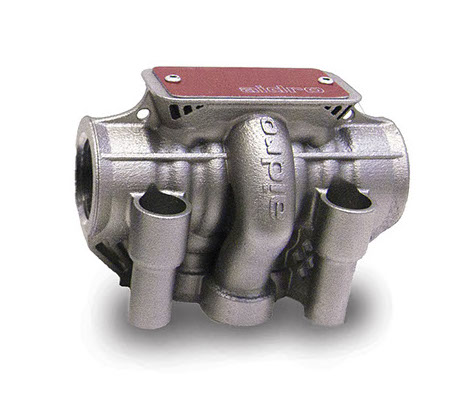
AIDRO ames valves, lower weight, better flow.
Flow is indeed everywhere and applications such as conformal cooling for molds that are the bedrock of many a failed 3D printing presentation are also flow applications. If we look at factories, oil & gas, chemicals, energy generally, nuclear, food processing & production, mining, cement, steel and other metals, a small optimization in flow could have a huge impact.
If you and I have the same $1billion dollar plant and yours is 0.5% more efficient because your oil flows faster or is mixed faster or is mixed more evenly, etc., then this will have a huge impact. If I can make just 1% more plastic than you because my crucial reaction happens in a chamber with the right texture on it or that is the perfect geometry, then this will also be huge. Any kind of internal channel optimization could bring benefits. If I can more reliably extrude pastry cream into my snacks, this will also be a gain. In rocket engines, it is already apparent that gas and liquid flow there can be optimized through 3D printing, This has also been the case in car manifolds and other flow-related car parts. We can make combustion engines faster and more efficient. Besides car engines, there are many other engines, from large ship diesels to turbines for industry, that we can make more efficient also.
Conformal cooling simulation and production by 3DSystems.
Optimizing internal topology or through optimizing the structure of the part itself affects flow as well. Adding heatsinks or spectacular twists and bends to parts can also impact flow. Integrating parts and functionality can make flow more efficient. Less brazes or welds could improve system flow. Overall, our greater geometric freedom lets us design and optimize flow through parts. Combine this with finite element analysis and other tools and you can optimize whole assemblies, systems or factories for flow. Now, at this point, you’re either thinking, “Duh,” or this is completely new to you. Also, I have repeatedly talked about internal topology optimization, but this is different. Internal topology optimization is a nice idea, thinking about flow lets you see where you can apply this idea.

GE Catalyst OPR
For some people, thinking like this comes naturally due to their training or how they think. An electrical engineering friend of mine was unmoved by my personal insight. He’d more or less thought like this all along. Another friend who designed extruders was also most unstirred. Most all others, however, tend to think of things from the outside-in or as a larger functionality—e.g., a car is many things, including a combustion engine.
Most tend to think in parts or in terms of functionalities or of things as discrete units that do their own thing. Or we think of a car holistically, or we think we do but, actually, we don’t conceptualize the entire object, but think only of its meaning as a whole—as an artifact. Like the automatic need for categorization, here we are distilling meaning while concealing wisdom.
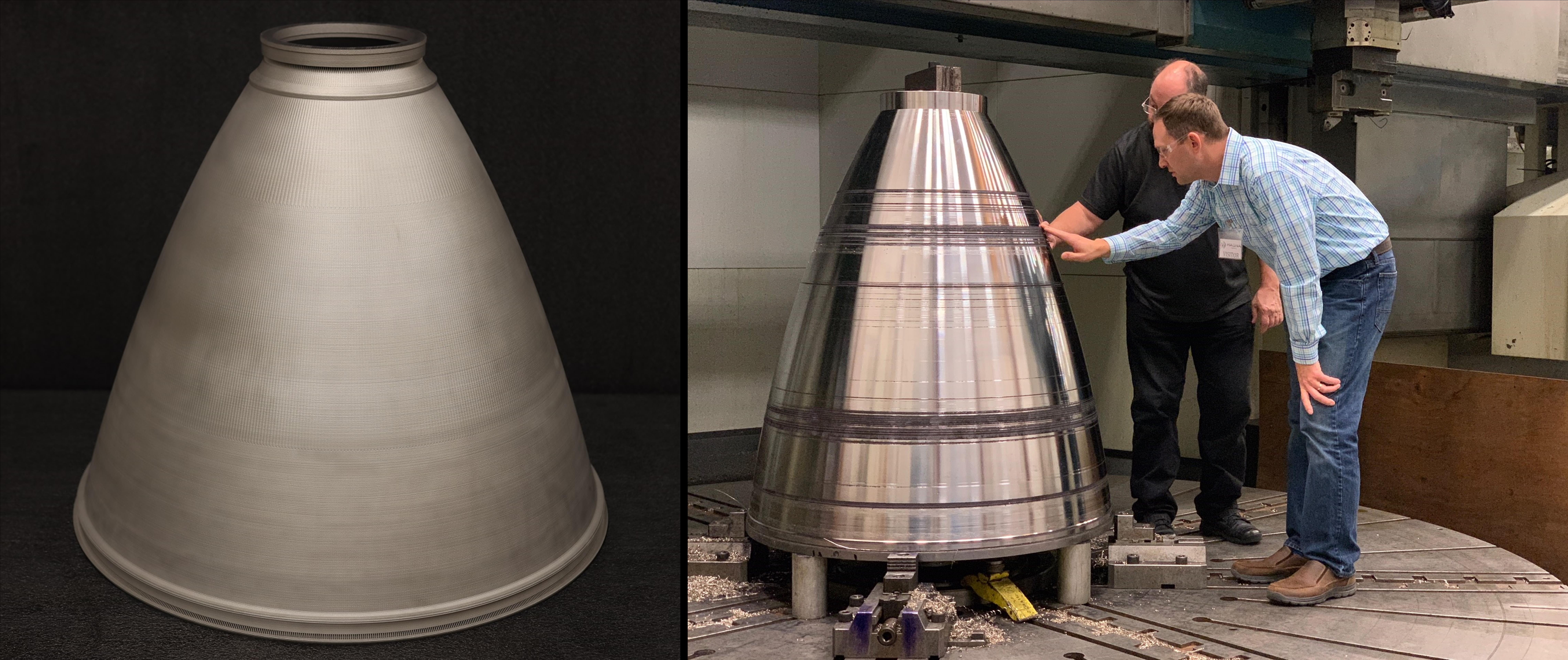
Also a nozzle.
Because, if you think of a car as a thing through which things flow, everything changes. You start to see shortcuts, wasted space, inefficiencies, great big blocks of stupid. You start to think that more parts could be interwound like intestines or compressed as lungs or filled with hidden geometries as gecko feet. You start to look suspiciously at rectangles, the heavy, the standard, and the always there. The world becomes a plastic thing.
And you start to realize that the problem with redesigning parts for DfAM and all of that jazz is the word “parts.” Imagine, that there is no such thing. Imagine parts don’t exist. That will free your mind so that you will design the future through flow.
Subscribe to Our Email Newsletter
Stay up-to-date on all the latest news from the 3D printing industry and receive information and offers from third party vendors.
Print Services
Upload your 3D Models and get them printed quickly and efficiently.
You May Also Like
Making Space: Stratasys Global Director of Aerospace & Defense Conrad Smith Discusses the Space Supply Chain Council
Of all the many verticals that have been significant additive manufacturing (AM) adopters, few have been more deeply influenced by the incorporation of AM into their workflows than the space...
EOS in India: AM’s Rising Star
EOS is doubling down on India. With a growing base of aerospace startups, new government policies, and a massive engineering workforce, India is quickly becoming one of the most important...
PostProcess CEO on Why the “Dirty Little Secret” of 3D Printing Can’t Be Ignored Anymore
If you’ve ever peeked behind the scenes of a 3D printing lab, you might have caught a glimpse of the post-processing room; maybe it’s messy, maybe hidden behind a mysterious...
Stratasys & Automation Intelligence Open North American Tooling Center in Flint
Stratasys has opened the North American Stratasys Tooling Center (NASTC) in Flint, Michigan, together with automation integrator and software firm Automation Intelligence. Stratasys wants the new center to help reduce...