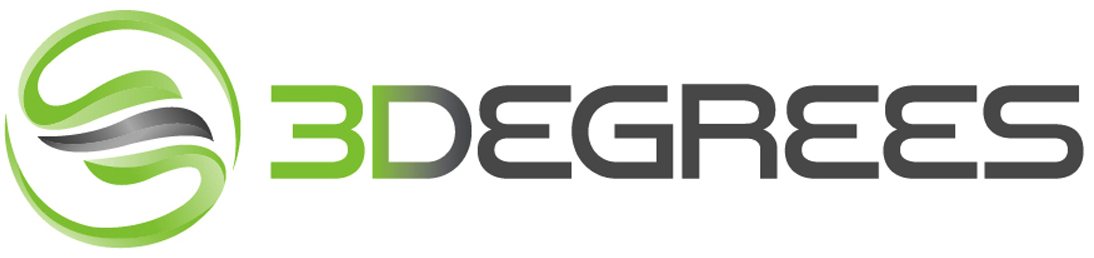
Mike Vasquez, PhD, will be speaking at 3DPrint.com’s upcoming AMS online industry summit (Feb 9-10, 2021). Register here.
It’s exciting to see the acceleration of adoption and acceptance of 3D printing in the manufacturing sector, which has been bolstered by the desire of many companies to have more direct control over their supply chain given the realities of COVID. Machine manufacturers are rapidly deploying new technology (SLM/VELO3D) and companies gained tremendous capital infusions (Desktop Metal/Relativity Space) based on the promise of the technology being production-ready. These events will continue to build momentum that will propel the industry forward.
One of the challenges users are experiencing as machines get faster and more sophisticated is the need to have a streamlined, efficient way to capture and use the significant amount of data that is generated at each stage of the workflow, including part design, materials management, build/machine data, post processing and inspection. The ability to view this data seamlessly has the power to provide critical metrics for both suppliers and customers to continue the push for production parts. Right now, this data is often generated and stored on different islands, whether from internal tests, vendor certification, in Word or PDF, or even stored only in the machine itself.
3Degrees spent over a year talking with 80+ users of production 3D printing equipment to understand this problem and see if there was an opportunity to create a “best practice” solution. From those conversations, I now joke that Microsoft is far and away the software leader in 3D printing because 90% of all technical 3D printing data on build outcomes lies on some sort of spreadsheet. From an ease of use perspective, that’s an adequate way to solve the data island problem, but it underutilizes the power of that data when looking to integrate bigger data sets, compare various builds or materials or ensure parts intended for consumer-use could be documented from the start of production to the actual delivery.
To address this challenge the 3Degrees team developed a software tool called TRACE, which is a digital platform that houses 3D printing data in an easy to use, streamlined, and searchable way for users of AM metals and polymers. This tool allows users to benchmark material properties, create work instructions, and digitally store and analyze data from all aspects of the 3D printing workflow.
As an early case study, we put data from the Renishaw Additive Manufacturing Solution Center on to TRACE via Renishaw’s InfiniAM API, which enabled the team together live machine data from 23 different sensors covering all aspects of the machine operation. For each build, TRACE tracked these sensor inputs (build chamber parameters like temperature and gas content) and tied these parameters to design inputs, material feedstock data, work instructions for operation, post production and inspection data. TRACE provided a platform to see how each machine was performing over time and analytics provided by these insights are being leveraged to improve aspects of repeatability and machine maintenance.
In 2021, TRACE is continuing to expand capabilities and will be deployed with an aerospace supplier to enable them to report critical findings and serialized qualification data in a way that helps their customers expand capabilities using 3D printing and get away from the data island mentality.
As 3D printing use cases grow, we anticipate we’ll see demand from many companies who realize the need to improve efficiency and ensure they meet all quality control and documentation requirements. We’ve built TRACE to be easy to customize, flexible and cost-efficient solution. Given our deep expertise in the space, we’d say it’s a much better option than Microsoft.
Subscribe to Our Email Newsletter
Stay up-to-date on all the latest news from the 3D printing industry and receive information and offers from third party vendors.
Print Services
Upload your 3D Models and get them printed quickly and efficiently.
You May Also Like
Reinventing Reindustrialization: Why NAVWAR Project Manager Spencer Koroly Invented a Made-in-America 3D Printer
It has become virtually impossible to regularly follow additive manufacturing (AM) industry news and not stumble across the term “defense industrial base” (DIB), a concept encompassing all the many diverse...
Inside The Barnes Global Advisors’ Vision for a Stronger AM Ecosystem
As additive manufacturing (AM) continues to revolutionize the industrial landscape, Pittsburgh-based consultancy The Barnes Global Advisors (TBGA) is helping shape what that future looks like. As the largest independent AM...
Ruggedized: How USMC Innovation Officer Matt Pine Navigates 3D Printing in the Military
Disclaimer: Matt Pine’s views are not the views of the Department of Defense nor the U.S. Marine Corps Throughout this decade thus far, the military’s adoption of additive manufacturing (AM)...
U.S. Congress Calls Out 3D Printing in Proposal for Commercial Reserve Manufacturing Network
Last week, the U.S. House of Representatives’ Appropriations Committee moved the FY 2026 defense bill forward to the House floor. Included in the legislation is a $131 million proposal for...