Polymer powder bed fusion printers have been a mainstay of the 3D printing world for many years now. These highly productive machines dominate the service bureau installed base and are used for surgical guides, industrial parts, and prototypes.
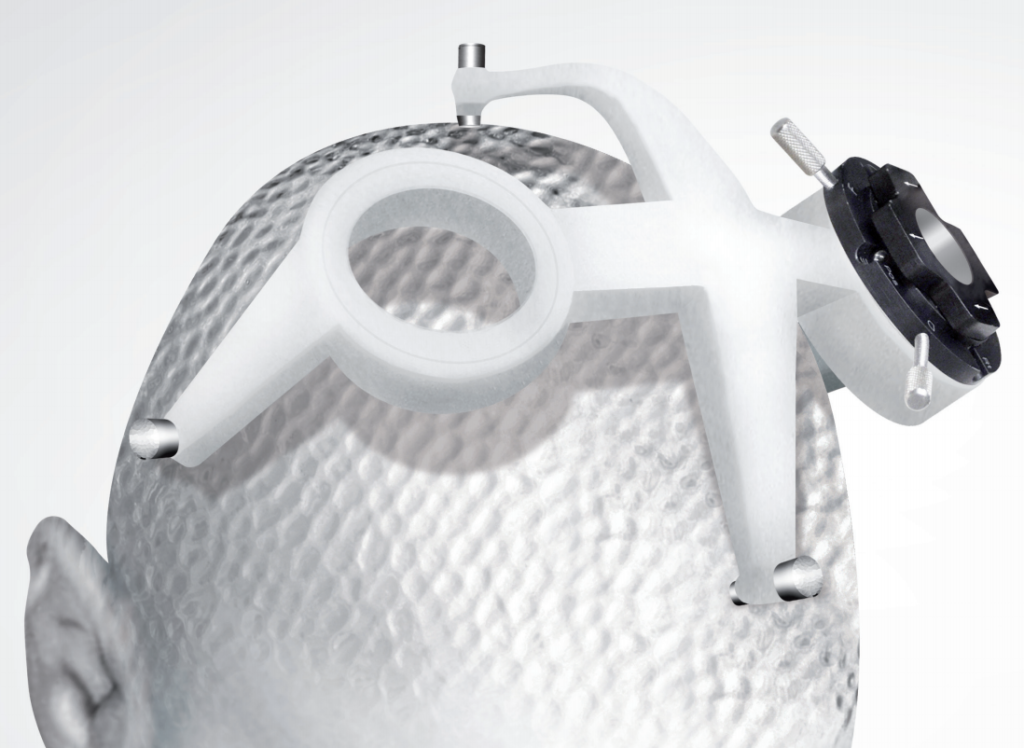
A custom Starfix fixture made on an EOS P100 in PA12
Compared to other technologies, powder bed fusion (PBF)—also referred to as laser powder bed fusion (LPBF) and selective laser sintering (SLS), or just “sintering”—is most suited to making many small parts at once. Parts tend to be porous, but post-processing is increasingly automated thanks to Post Process Technologies, Rosler, Dye Mansion, and others. Post-processing is also lower in cost than with stereolithography and parts are finer and more detailed than material extrusion (but less smooth and with less detail than SLA).
Material extrusion has many more materials, is cheaper, and is better for larger (especially flat) parts. Sintering on the other hand, lends itself well to mass-customization applications and is the ideal technology if you need 10,000 of something unique, tennis ball-sized each day. An analogous technology is Multi Jet Fusion (MJF) by HP. If you’re doing mass customization of end-use parts, end use parts generally, medical parts or consumer applications ,you’ll want to look at both of these technologies. MJF is significantly less expensive than powder bed fusion, but a less widely deployed technology.
Market
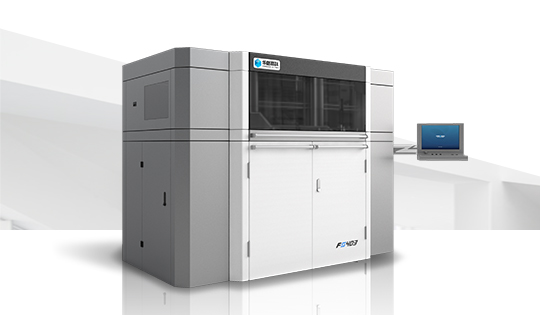
Farsoon 403P
The PBF market is almost completely dominated by EOS. A privately held firm from Krailing, Germany, EOS has been firmly in the driving seat of this technology almost from inception. Focused on the long-term and diligent, the company is steadily increasing global penetration and exploring more applications and materials. Clever in ring-fencing patents EOS has been greedy on the materials side, but not too greedy on the machine side. This has forestalled any real competition until recently.
3D Systems also makes industrial-sized sintering equipment. That firm has gotten a boost from being used for the U.S. military establishment and other firms in stateside industrial applications lately. HP is gaining with a growing installed base. Now, companies such as Farsoon are making credible powder bed fusion systems, as is Prodways. Along with primary equipment, the growth in ancillary equipment and automation is growing.
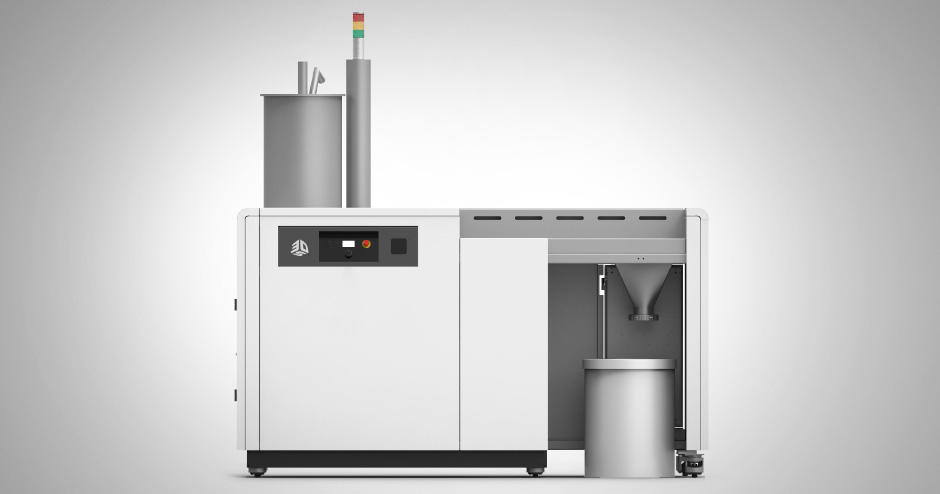
3D Systems’ ProX SLS 6100 Material Quality Control System recycles and transports powder for the machine.
Industrial systems are over $150,000 and they are complex to make and make well. This staves off competition. In the low end, we can see new entrants. But, Formlabs, with its formidable product development capabilities, has repeatedly pushed back the launch of its sintering offering: a warning to new entrants that sintering is far more complex than it may seem.
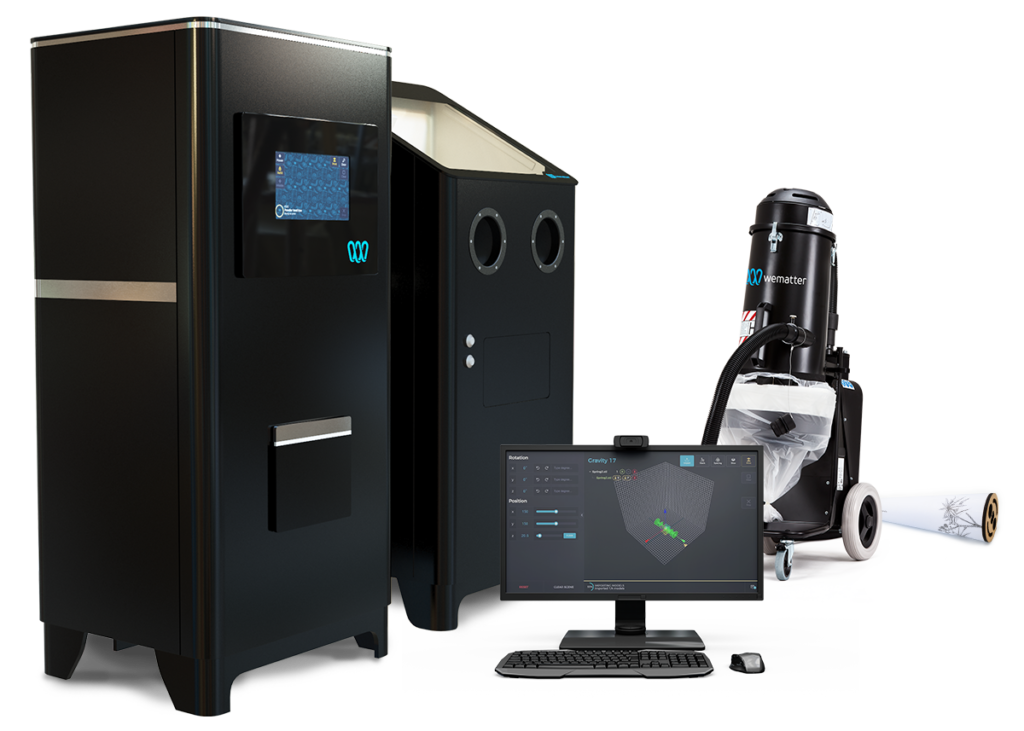
WeMatter also has a series of devices for its entry-level system.
Sinterit and Sintratec (in which the Langer family who owns EOS is an investor through AM Ventures) are growing in the desktop and inexpensive space, making machines between $5,000 and $20,000. There are also new entrants, such as WeMatter and NaturalRobotics.
Growth in desktop SLS has been painfully slow, however. All desktop firms have not excelled in making the business case for owning a sintering system. With many companies now shopping for Material Extrusion machines from $3,000 to $30,000, awfully few of them are even looking at sintering.
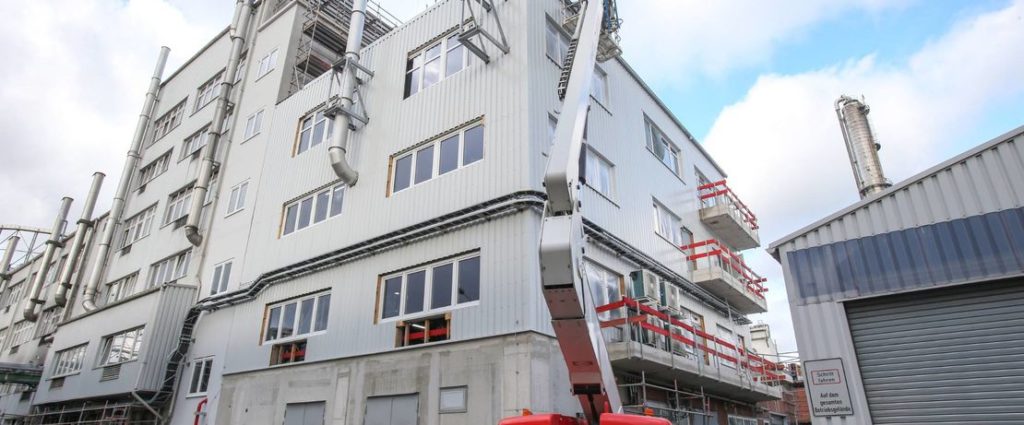
New Evonik PA 12 facility.
In materials, this market is almost exclusively into PA 12 (nylon) and variants of it, such as glass-filled PA 12. Evonik has dominated the materials space since inception, while Arkema has gained, as has Solvay. BASF and DSM (now Covestro), also have sintering offerings. LehmannVoss is an example of a firm that consistently punches above its weight with custom formulations of powders.

Arkema PEKK
PEEK, PEKK and flexible materials, such as TPE and PP, are fast-growing materials.
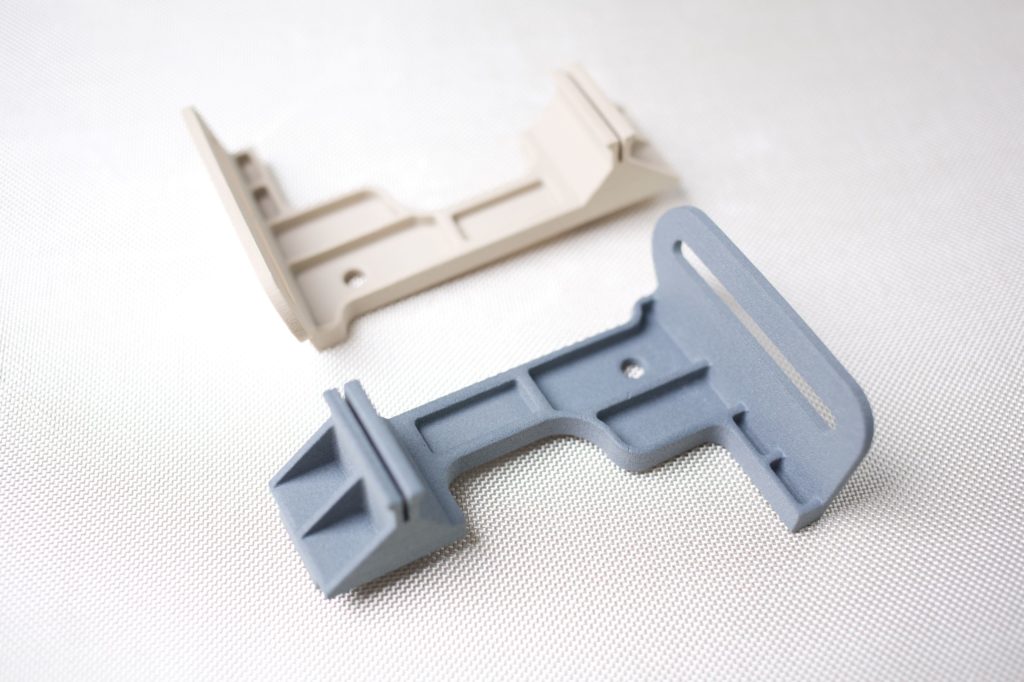
Victrex sintered PEEK parts
DSM’s PBT powders are an innovation, as are PEKK powders from Arkema. HP’s rollout of twin TPE powders from BASF and Lubrizol can really make a lot of new applications possible in several industries. HP’s low-cost PP material, however, can really shake up the industry with a huge span of applications and high recyclability. In sintering, unsused powder supports built parts. This can partially be recycled, but, generally, the industry throws away half the powder is buys. With the new PP material, high recycling rates make an already low-cost material much more economical still. A similar innovation from service and software company Materialise is its Bluesint powder, which could also shake things up.
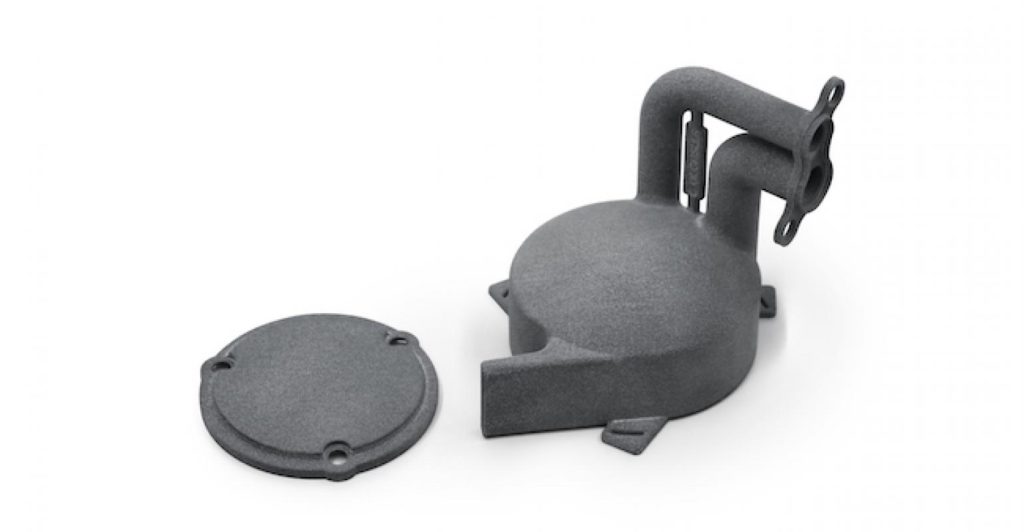
BASF PP for HP made by Oechsler.
Everyone is waiting for the Godot of the sintering market, the market entry of Xaar’s HSS technology. Assisted by Stratasys, this could, if it happens soon, really impact the market. It will take some time for them to find validation, however.
Typically we can see an expansion of post-processing as the biggest impact trend on this segment of the industry. Automation can really bring down costs here in a way that is hereto not possible in SLA and FDM. This could really move the needle for these firms into more mass customization applications and deeper into industry. Especially technologies that improve surface finish and reduce moisture uptake can really change things. There are some unsolved issues with the long-term use of sintered parts in mechanical applications and the degradation of the mechanical performance of those parts. Generally, however, sintering is the one technology that is set to make the biggest leap, if and when they develop a completely automated toolchain from file to finished part.
Sales
Sales of entry-level systems have always been sluggish when compared to FDM and now SLA too. There are no signs of building buzz or momentum around entry-level sintering systems. This is in stark contrast with the march of FDM in enterprise penetration and renewed interest in SLA. Perhaps Formlabs can change this. Notably, a Chinese firm has not come out in force with a low-cost sintering system. This is a question of time. Surprisingly as well, there has been comparatively little activity of Kickstarter, and VC funding generally, in entry-level sintering.
In mid-market sintering systems, EOS continues to grow and expand significantly. The slowdown in automotive and hesitation by corporates has lead to slower adoption in new industries than previously anticipated.
In the next installment in this series, we will look more closely at trends related to machines, recommendations for the segment and competitors, as well as the critical issues that need to be resolved for PBF and MJF technology.
Subscribe to Our Email Newsletter
Stay up-to-date on all the latest news from the 3D printing industry and receive information and offers from third party vendors.
Print Services
Upload your 3D Models and get them printed quickly and efficiently.
You May Also Like
Reinventing Reindustrialization: Why NAVWAR Project Manager Spencer Koroly Invented a Made-in-America 3D Printer
It has become virtually impossible to regularly follow additive manufacturing (AM) industry news and not stumble across the term “defense industrial base” (DIB), a concept encompassing all the many diverse...
Inside The Barnes Global Advisors’ Vision for a Stronger AM Ecosystem
As additive manufacturing (AM) continues to revolutionize the industrial landscape, Pittsburgh-based consultancy The Barnes Global Advisors (TBGA) is helping shape what that future looks like. As the largest independent AM...
Ruggedized: How USMC Innovation Officer Matt Pine Navigates 3D Printing in the Military
Disclaimer: Matt Pine’s views are not the views of the Department of Defense nor the U.S. Marine Corps Throughout this decade thus far, the military’s adoption of additive manufacturing (AM)...
U.S. Congress Calls Out 3D Printing in Proposal for Commercial Reserve Manufacturing Network
Last week, the U.S. House of Representatives’ Appropriations Committee moved the FY 2026 defense bill forward to the House floor. Included in the legislation is a $131 million proposal for...