As a team of skilled researchers outside of Geneva, Switzerland work to discover the physical principles underpinning our existence, they occasionally run into a snag here and there. Such was the case when engineers at CERN’s Large Hadron Collider (LHC) sought to develop a series of cool bars for reducing the temperature of the system for the LHC Beauty (LHCb) experiments for collecting and tracking particles from the LHC. When traditional manufacturing techniques weren’t suited for the task, CERN and the National Institute for Subatomic Physics (Nikhef) turned to 3D printing, from 3D Systems (NYSE: DDD).
The Large Hadron Collider is a 27-kilometer-long scientific experiment that accelerates particles and then smashes them against particle detectors. The LHCb is a series of eight experiments all trying to collect and track particles from the LHC, relying on what is called the LHCb SciFi tracker, a 140-meter-long, two-millimeter-wide photon detector strip.
The SciFi system itself is rather sci-fi, but the name actually stands for something, according to Phys.org:
“Scintillating fibres, as the name suggests, are optical fibres – with a polystyrene base, in this case – that emit tens of photons in the blue-green wavelength when a particle interacts with them. Secondary scintillator dyes have been added to the polystyrene to amplify the light and shift it to longer wavelengths so it can reach custom-made silicon photomultipliers (SiPM) that convert optical light to electrical signals. The technology has been well tested at other high-energy-physics experiments. The fibres themselves are lightweight, they can produce and transmit light within the 25-nanosecond window and they are suitably tolerant to the ionising radiation expected in the future.
“Each scintillating fibre making up the sub-detector is 0.25 mm in diameter and nearly 2.5 m in length.”
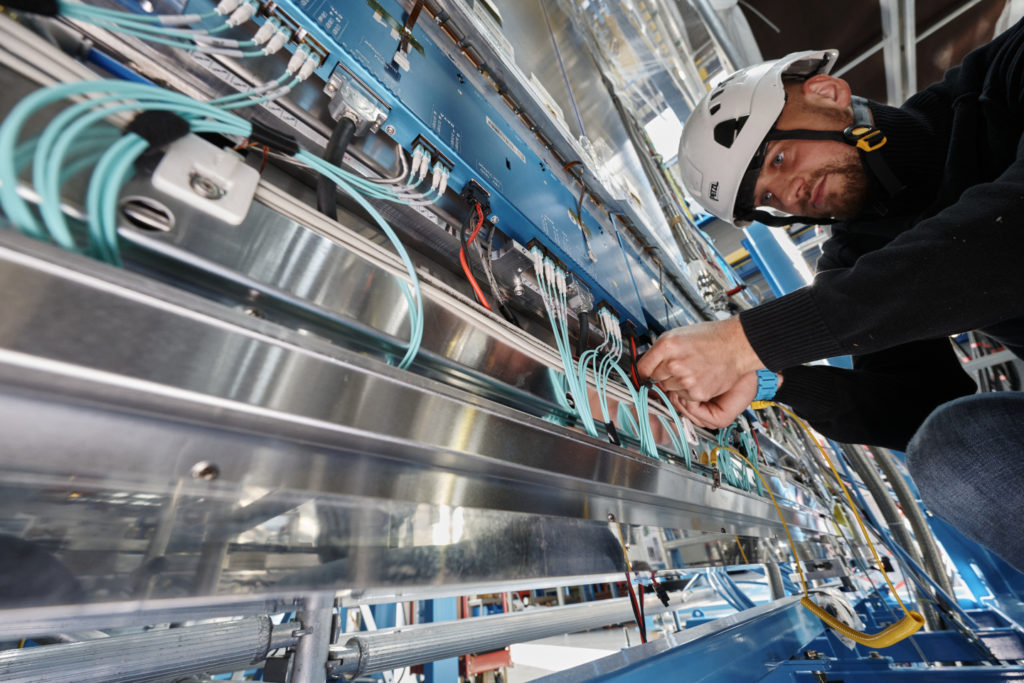
The SciFi detector of the LHCb
There are more than 10,000 km of scintillating fibers meant to be integrated into the LHCb that will be hit with neutrons made from nearby calorimeters. Radiation damage caused by this process will in turn create “dark noise”, in which thermally excited electrons push the SiPMs to generate a signal similar to those made by individual photons. To keep the SiPMs cool, shielding between the SciFi and the calorimeter is necessary.
Blake Leverington, a researcher coordinating part of the SciFi project, explained, “Measurements have shown that the rate of dark noise can be reduced by a factor of two for every 10 °C drop in temperature.”
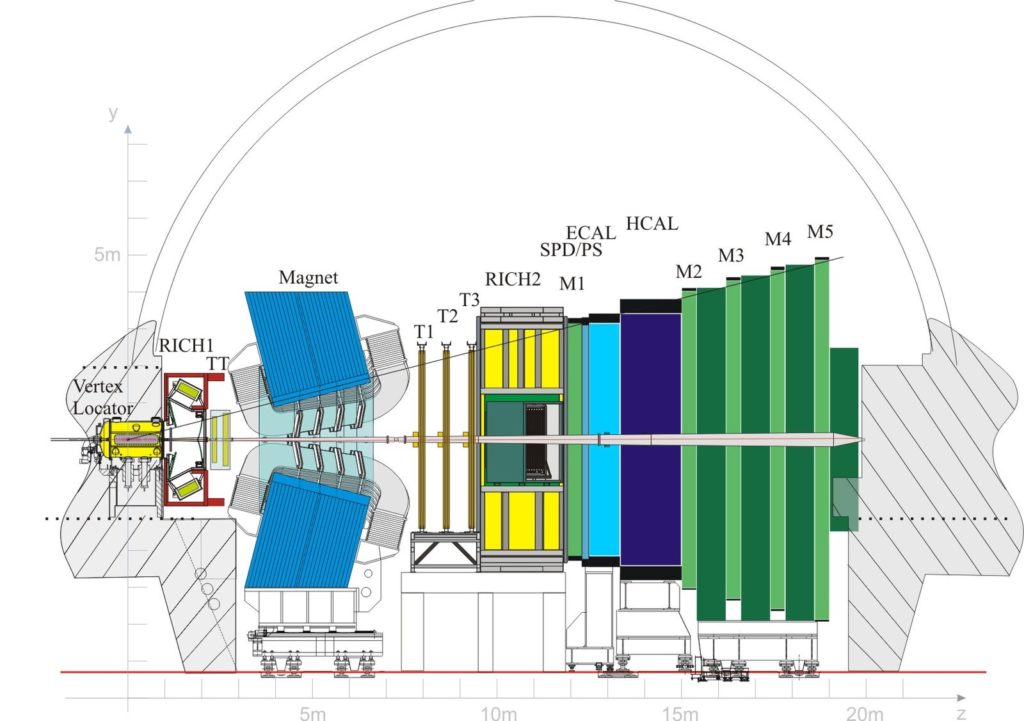
A side view of the LHCb
To design the complex cooling system necessary for the project, Nikhef’s Anthony Pellegrino underscored a series of constraints:
“limited space in which the cool-bars are required to fit, the heat that needs to be dissipated within that short space, the temperature uniformity required over the length of the entire photon-detection strip, and the flatness of the cool-bars necessary to preserve the detector efficiency and resolution. The effect of this is that you have to be very efficient in how you construct your cooling.”
Ultimately the resulting “design was so beautiful, but it was not producible in the usual ways.” Unable to make the part conventionally they turned to 3D printing. The Nikhef team then worked with 3D Systems’ Customer Innovation Center (CIC) in Leuven, Belgium to transform their design into one optimized for 3D printing. The resulting design was printed vertically and the team took special care to assure that it was designed so that loose powder could be extracted from the channels.
The resulting strip has cool-bars that have been topology optimized and 3D printed to help cool the detector. 3D Systems designed and produced 300 cool bars for CERN, capable of cooling the system to -40˚C. The team had to adjust some parameters to achieve the required wall thickness of 0.25mm. Each 263mm part needed “flatness to have a precision of 50 microns” over its entire length, as well. The cool bars themselves are welded together out of two mirrored 3D printed parts made in TiGr23 (Ti6Al4V ELI). Each cool-bar has parallel cooling channels and is rated to last a decade.

The bars
Recently, we interviewed 3D Systems CEO Jeff Graves on the 3DPOD. He was ambivalent about 3D Systems’ 3D printing service, but was very positive about this kind of application development work whereby 3D Systems would help customers design completely new parts or develop new solutions. There is still much out there that 3D printing could solve and much to which the technology could be applied. A few years ago a Beam Position Monitor part for the LHC was 3D printed, as well. It is nice to see when 3D printing solves problems that no other technology can. When we are a solution like this one, for a complex part with exacting tolerances and requirements ,it proves that we can walk the walk, not only talk the talk.
Conformal cooling channels and other cooling related parts have long been a part of 3D printing lore. I still think that we’ve seen more PowerPoint slides on conformal cooling channels than we have parts, but 3D printing for cooling is a very exciting topic. As each year goes by, we see more and more people turn to 3D printed heatsinks and other cooling solutions as well. With new materials such as copper and aluminum becoming available, we should see an increase in the performance of and use of 3D printing for heat sinks. Optimized designs, textures, and consolidated parts or lower mass parts could make a significant impact on electric engines and all sorts of industrial equipment.
A slight improvement of a 3D printed heatsink or cooling element could mean that an electric car can go further, a computer could operate quicker, a rocket could be faster or a boat could be cheaper to run. Cooling is an area that is being looked at across many industries. Time and time again, people come to our industry because we’re the only one that can make their exact solution.
But, apart from these moonshots, there is no startup or company leveraging a lot of effort or money toward optimized heating and heat-dissipating solutions for all manner of industries. If you’re looking for a new application area to invest in or an application to develop I’d suggest looking at topology optimized parts for heating and cooling in automotive, aerospace and industrial. Startups such as Additive Drives can really ensure that adequate solutions for things such as electric engines can be 3D printed more quickly and are making the case for more of these companies to be created. With both 3D Systems and startups chasing solutions for applications in cooling, could become a much hotter area.
Subscribe to Our Email Newsletter
Stay up-to-date on all the latest news from the 3D printing industry and receive information and offers from third party vendors.
Print Services
Upload your 3D Models and get them printed quickly and efficiently.
You May Also Like
Reinventing Reindustrialization: Why NAVWAR Project Manager Spencer Koroly Invented a Made-in-America 3D Printer
It has become virtually impossible to regularly follow additive manufacturing (AM) industry news and not stumble across the term “defense industrial base” (DIB), a concept encompassing all the many diverse...
Inside The Barnes Global Advisors’ Vision for a Stronger AM Ecosystem
As additive manufacturing (AM) continues to revolutionize the industrial landscape, Pittsburgh-based consultancy The Barnes Global Advisors (TBGA) is helping shape what that future looks like. As the largest independent AM...
Ruggedized: How USMC Innovation Officer Matt Pine Navigates 3D Printing in the Military
Disclaimer: Matt Pine’s views are not the views of the Department of Defense nor the U.S. Marine Corps Throughout this decade thus far, the military’s adoption of additive manufacturing (AM)...
U.S. Congress Calls Out 3D Printing in Proposal for Commercial Reserve Manufacturing Network
Last week, the U.S. House of Representatives’ Appropriations Committee moved the FY 2026 defense bill forward to the House floor. Included in the legislation is a $131 million proposal for...