Fashion designer Ganit Goldstein has teamed up with Stratasys to create unique pieces by combining embroidery craft methods with direct-to-textile 3D printing. The result was a distinctive Japanese-inspired patterned 3D printed collection called “WeAreABle” that the artist launched in October through a virtual reality fashion exhibition space on her website. By incorporating multi-material PolyJet technology and 3D scanning to produce 3D textiles, Goldstein is pioneering developments in novel textile production. The project is part of a European Union (EU) Horizon 2020 Re-FREAM grant that had ten designers teaming up with scientists to rethink the manufacturing process of the fashion industry.
During time spent at the Tokyo University of the Arts, Goldstein found inspiration in Asian craft embroidery and textile painting. Her kimono designs follow Japanese ikat weaving, a traditional folk technique produced since the mid-eighteenth century where unique patterns look as if they were splashed onto the fabric. Back in her London studio, the designer chose to integrate the crafting technique with 3D scanning technology to then 3D print it onto the fabric. Maintaining the identity of the technique while giving it a unique approach that could pave the way for the future of 3D printing in textiles.

3D Multi-color printed Kimonos inspired by traditional IKAT weaving, printed directly onto fabric in a collaboration with Stratasys. Image courtesy of Ganit Goldstein
For the “WeAreABle” project, Goldstein relied on 3D body scans and 3D parametric codes combined with multi-color 3D printing directly on the fabric for an entirely new way of manufacturing garments. Based on measurements from a 360-degree body scanner she was able to fit the garment to a person’s specific form and measurements. The resulting two outfits combine form, color, and flexibility in tailor-made pieces with unique materials and parametric patterns.

Ganit Goldstein used 3D body scans and 3D parametric codes to create the multi-color 3D printing directly on the fabric for an entirely new way of manufacturing garments. Image courtesy of Ganit Goldstein
Like many designers turning to 3D printing technology for bespoke creations, Goldstein is moving away from mass-produced fast fashions and toward an on-demand manufacturing platform, which could eventually become a collection for customers seeking artistic yet wearable pieces that are one of a kind. Stratasys’ direct-to-textile printing technology allowed her to fully digitize design workflows, all through to production.
This goes on to demonstrate that it is possible for localized manufacturing and mass customization to take the lead in fashion. The novel technique could eventually help reduce inventory and waste, a very relevant trend, especially as the industry moves towards more sustainable brands that create fashion without leaving a negative footprint.
Stratasys has already been working closely with a number of household fashion brands to optimize its novel PolyJet technology to meet the needs of modern-day apparel fabrication and make customized fashion design commercially viable. Partnerships with vanguard designers threeASFOUR and Travis Fitch at New York Fashion Week led to commercial possibilities of 3D printing directly on clothing. The pioneer 3D printing manufacturer also collaborated with Goldstein in 2019 on a fashion collection of 3D printed shoes and jewelry.
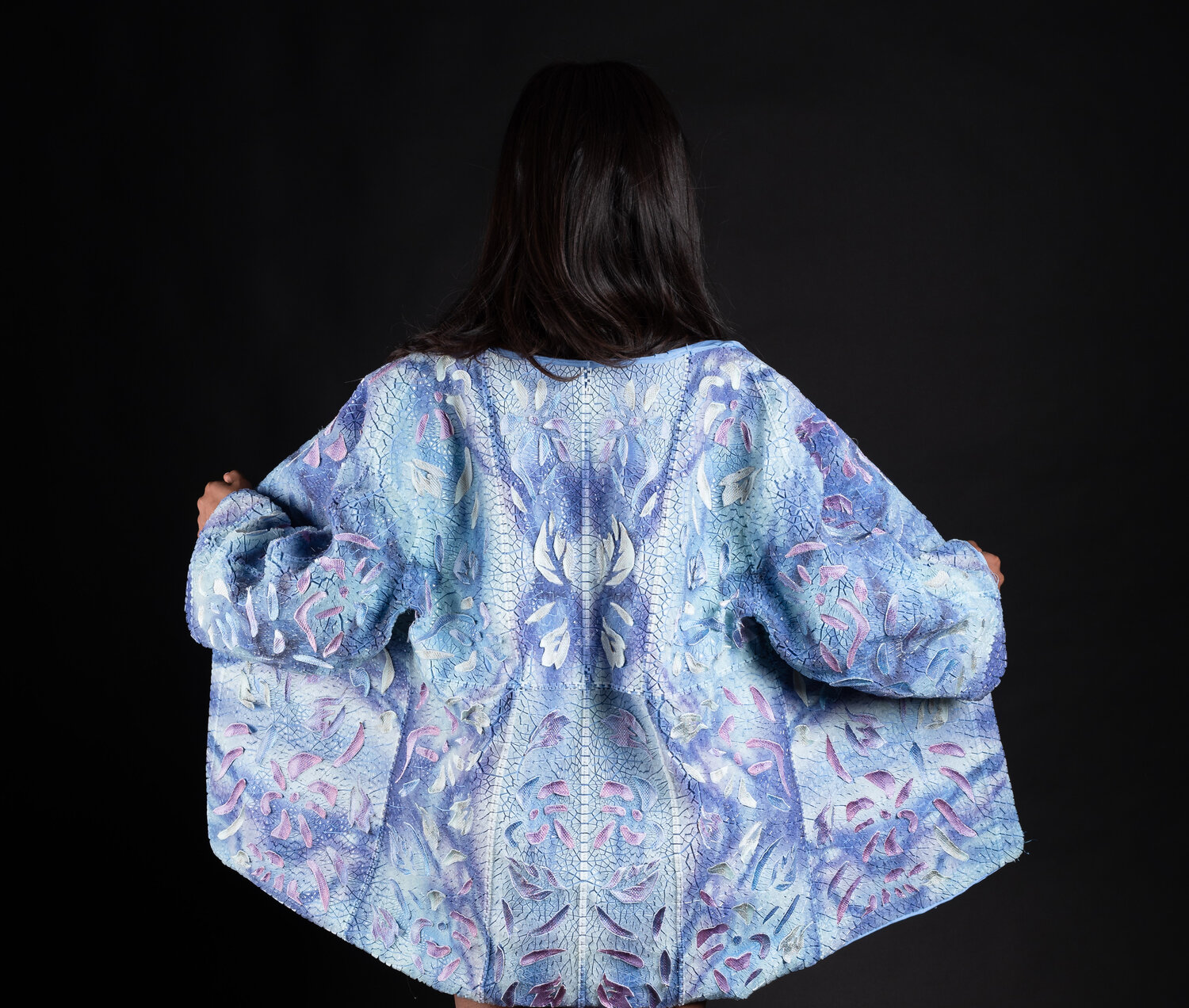
3D Multi-color printed Kimono inspired by traditional IKAT weaving, printed directly onto fabric in a collaboration with Stratasys. Image courtesy of Ganit Goldstein
For this project, Goldstein considered the human body as a platform for innovation and focused on developing smart textiles. Particularly fixating on the limits of technology and tradition by redrawing the boundaries between hand-made and machine-made by combining the two. While Japanese embroidery is the soul of the project, direct-to-textile multi-color 3D printing is at the heart of it. The kimono follows an algorithm that is composed of the 3D body scan and translated to the print surface during the printing process.
By using 3D printing, the designer and engineers at Stratasys were able to print the data from the scans and make a textile that “remembers” the 3D properties of a specific body, described Goldstein. The outcome consists of outfits that are fit-to-measure to the exact curves and unique body shape of the model.
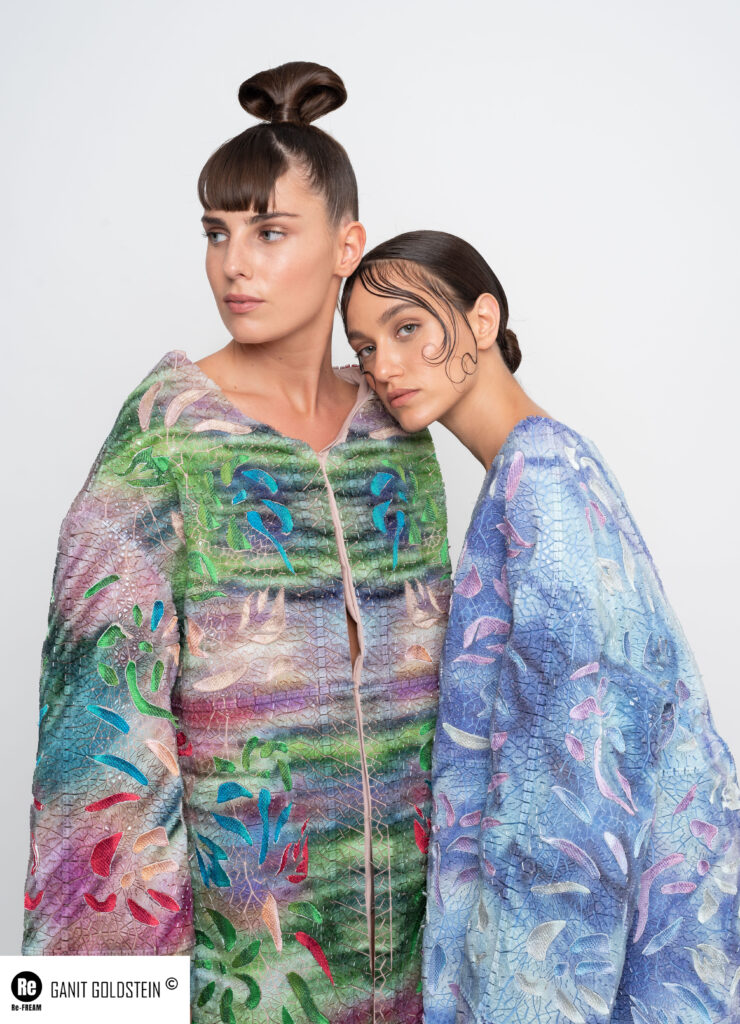
3D Multi-color printed Kimonos inspired by traditional IKAT weaving, printed directly onto fabric in a collaboration with Stratasys. Image courtesy of Ganit Goldstein
In the end, each garment crafted from 3D to 2D CAD manipulations and a 3D design workflow is a precise piece of fabric. The never-seen-before designs show a unique use of colors, textures, and dominant shades that can be appreciated from different angles, with a signature focal point in the back. The Kimono style fixates on floral-like patterns that cover the fabric entirely for a modern take on the centuries-old traditional dress of Japan.

Ganit Goldstein’s 3D printed Kimono inspired collection exhibiting in Milan. Image courtesy of Stratasys/Ganit Goldstein
Since launching, the 3D printed creations have already been presented in the prestigious “Linea Pelle” exhibition in Milan by the Stratasys team, along with several other outfits and textiles from Stratasys Art, Fashion & Design collections, which brings a closer look at the new technology for printed textiles thanks to PolyJet technology. The pieces will also be presented as part of the permanent exhibition for the following months in D-house, also in Milan.
Although the launch of the new collection was slated for Berlin’s annual “Wear It” summit exhibition, due to COVID-19-related restrictions and social distancing regulations, Goldstein had to reimagine the way she presented her work. Working with leading technology giant Intel, she created a virtual reality platform for a realistic 360 degree exhibition space to showcase her treasured creations. Allowing the audience to view the 3D collection in full virtual reality space and bridging the gap between our new reality of social distancing.

Ganit Goldstein working on the VR presentation of her garments. Image courtesy of Stratasys/Ganit Goldstein
Subscribe to Our Email Newsletter
Stay up-to-date on all the latest news from the 3D printing industry and receive information and offers from third party vendors.
Print Services
Upload your 3D Models and get them printed quickly and efficiently.
You May Also Like
3D Printing News Briefs, July 2, 2025: Copper Alloys, Defense Manufacturing, & More
We’re starting off with metals in today’s 3D Printing News Briefs, as Farsoon has unveiled a large-scale AM solution for copper alloys, and Meltio used its wire-laser metal solution to...
BCN3D Files for Bankruptcy Despite Recent Milestones—But Rescue Deal May Be Underway
For the latest updates (as of June 2, 2025), see the end of this article. Spanish 3D printer manufacturer BCN3D has filed for voluntary bankruptcy, according to Crónica Global. Based...
Nikon SLM Solutions Partners with ATI and Bechtel Plant Machinery on 3D Printed Hypersonics
One of the world’s most demanding technical challenges is the creation of maneuverable hypersonic vehicles. The country that does so well will command the ultimate high ground. They will essentially...
HAMR Industries Gets a FormAlloy X5R at Neighborhood 91
The Neighborhood 91 (N91) cluster of additive manufacturing firms in Pennsylvania has acquired a FormAlloy robot arm X5R Directed Energy Deposition (DED) system; specifically HAMR Industries. The X5R can work...