3D printing is often viewed as one of the key sustainable technologies, primarily because it can produce complex structures in one single part, facilitates efficient designs, and creates less waste. Even more so, when this technology is combined with resources that are reused instead of being discarded, efficiency skyrockets. Based on this idea, a startup that makes artfully crafted furniture has taken the concept of a circular economy to new levels. By combining sustainably sourced agricultural material waste, California-based Model No. has been creating on-demand custom furnishings using 3D printing technology.
Every item is 3D printed from biopolymers and plant-based resins that provide the flexibility of customization without the need for harmful petrochemicals – commonly used during traditional manufacturing and finishing of furniture products. Model No.’s eco-friendly materials are sourced from the remains of food crops which further reduce waste and allow upcycling of unused resources. Because these biopolymers are made from plants that are continually re-planted, the oxygen produced even helps offset any carbon dioxide emissions in the production process.
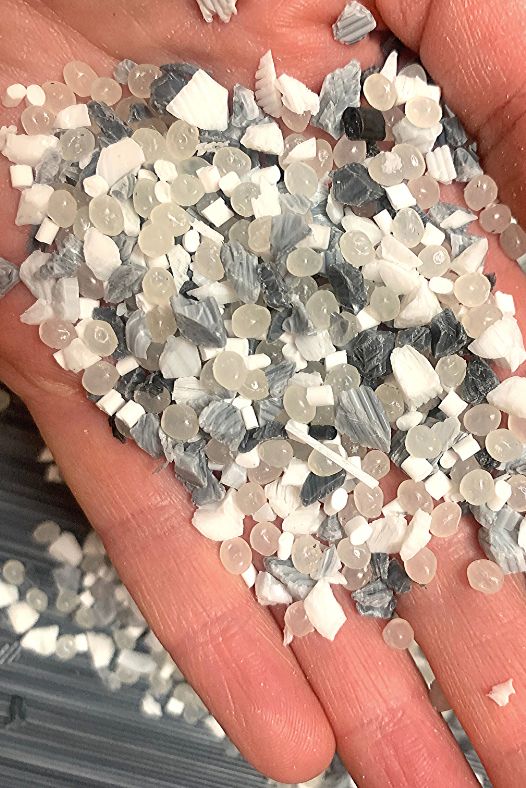
Model No. uses recycled and bio-resins to print every piece of furniture, as part of its commitment to eco-friendly furniture design. Image courtesy of Model No.
With the mission to redefine the future of furniture, co-founders Jillian Northrup, Jeffrey McGrew, and Vani Khosla created a company that is operating at the intersection of design, technology, and sustainability. Each one of the artfully crafted pieces is offered with a selection of pre-customized models created by the Model No. design team, which can be ordered just as they are, or can be fully customized to fit a particular style, budget, and home.
3D printed on large, custom-built 3D printers in Model No.’s facility, every furnishing can be produced in house and delivered in two weeks, eliminating long wait times and wasteful inventory. Each can be customized using the company’s computer numerical control (CNC) tools to create truly unique pieces, adjusting everything from the dimensions and contours to the color and finish materials.

Model No. uses customized 3D printers in-house to create its custom furnishings. Image courtesy of Model No.
Having the printing capability right in the manufacturing site also allows the design and manufacturing teams to make small scale models of each idea. Finding the right combination of form and customization options usually requires many iterations of sketches and small scale prototypes. Northrup stated in the Model No. site that making the smaller prototypes is a really good way to quickly and inexpensively make design decisions:
“Once we see the small version of the piece in hand, we can do preliminary stress tests and visual proportions analysis, letting us know what changes we need to make for the piece to be truly functional as well as beautiful.”

Model No. design and manufacturing process to create furniture using 3D printing technology and agricultural waste. Image courtesy of Model No.
Along with in-depth planning capabilities, the team relies on its six 3D printing machines to create some intricately complex designs that are inherently possible thanks to the technology. As the company continues to grow, it will continue to constantly develop new technology in-house to improve functionality as well as leverage and contribute to other open-source innovations and technologies from around the world.
Since founding the company in 2018, the team of designers has been working to produce a variety of tables, seating, and décor. With more than 35 product options, ranging from vases to coffee tables, customers have a wide variety of colors, designs, and budgets to choose from, which can result in one-of-a-kind pieces.

Model No. coffee tables are 3D printed using agricultural waste and customizable. Image courtesy of Model No.
Traditional furniture manufacturing continues to have a heavy impact on the environment. According to the U.S. Environmental Protection Agency (EPA), the amount of furniture and furnishings that end up in a landfill rose from 7.6 million tons in 2005 to 9.7 million tons in 2015, and the rate of increase is accelerating. Wood was the largest material category in furniture, and ferrous metals were the second-largest category. Plastics, glass, and other materials were also found.
Furniture also has a significant carbon footprint, which includes everything from the materials used, to the manufacturing process, to the environmental costs of climate-controlled storage, to shipment. In fact, UK-based My Tool Shed reported in 2019 that the average piece of furniture consumes approximately 47kg of carbon dioxide equivalent, which is the same as 5.3 gallons of consumed gasoline or driving some 30 to 60 miles.
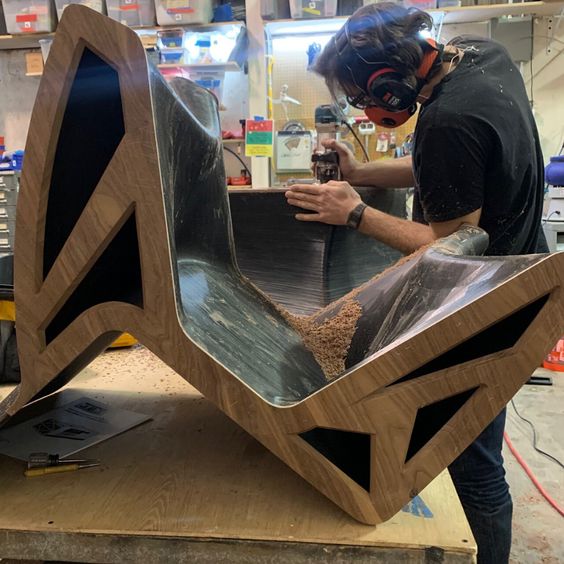
Model No.’s manufacturing team makes large furniture pieces using 3D printing and sustainable materials. Image courtesy of Model No.
Instead, Model No. hopes to do things differently. Aside from its biopolymers and plant-based resins, the company uses sustainably harvested wood for some of the larger furniture pieces, like the dining tables and particularly for an ergonomically designed curved chaise lounge – the flagship product of the company. When possible, the designers choose to use local species in all the wood details of its products, which means no deforestation or clear-cutting is involved.
Using local recyclable materials made in the U.S. helps avoid the negative environmental impact of importing materials from overseas, and has proven very practical during the 2020 COVID-19 pandemic that has shifted the world and turned global supply chains into a commercial nightmare. Model No.’s reliance on local resources and its proprietary 3D printing technology has proven an ideal solution as the world moves toward better manufacturing structures, systems, and in-house technologies that involve minimizing the amount of inventory held in global supply chains. The results are clear, browsing through the company’s site, the artfully designed pieces evoke clean cuts and minimalist elegance, capable of embellishing any living space, but best of all, they come with the added seal of sustainability and disruptive technology at its core.
Subscribe to Our Email Newsletter
Stay up-to-date on all the latest news from the 3D printing industry and receive information and offers from third party vendors.
Print Services
Upload your 3D Models and get them printed quickly and efficiently.
You May Also Like
The Dental Additive Manufacturing Market Could Nearly Double by 2033, According to AM Research
According to an AM Research report from 2024, the medical device industry, specifically in dentistry, prosthetics, and audiology, is expected to see significant growth as these segments continue to benefit from...
Heating Up: 3D Systems’ Scott Green Discusses 3D Printing’s Potential in the Data Center Industry
The relentless rise of NVIDIA, the steadily increasing pledges of major private and public investments in national infrastructure projects around the world, and the general cultural obsession with AI have...
AM Research Webinar Explores Continuum’s Sustainable Metal Additive Manufacturing Powders
Metal additive manufacturing (AM) powder supplier Continuum Powders is working to develop solutions that empower industries to reduce waste and optimize their resources. An independent life cycle assessment (LCA) of...
3D Printed Footwear Startup Koobz Lands $7.2M in Seed Round
California-based Koobz is focused on reshoring the U.S. footwear supply chain with advanced manufacturing processes, including 3D printing. The startup just announced that it has added $6 million to its...