Dutch chemical company Royal DSM has announced that it will be partnering with Nedcam, a spin-off company from the Maritime Research Institute Netherlands (MARIN), to add capacity and develop new applications for large-size 3D printing. Specifically, Nedcam, a provider of innovative 3D technology solutions, will be offering Fused Granulate Fabrication (FGF) 3D printing using DSM materials. Also, as part of the collaboration, the two companies will explore new applications in tooling, large-size, and circular end-use parts.
There has been an increase in the demand for large format printing across many industries. From aerospace to military and defense, upscaling large-format 3D printing has the potential to enhance the manufacturing industry by enabling low-cost, full-scale prototyping, and faster lead times. During the last few years, several companies have developed large-scale production technologies, anticipating a growing demand in the future, particularly from Asia Pacific countries, like China, India, and Japan, due to their booming economy, adaptability, technological advancements, and sustainable needs.
Through this new collaboration with DSM on material and 3D printing technology, Nedcam will offer commercial 3D printing production services to manufacturers looking for large-size applications, using DSM’s optimized pellet materials. The two companies will also collaborate to develop and test new materials, processes, and applications and will bring innovative solutions to markets requiring large-size 3D printing, such as marine, renewable energy, construction, and infrastructure. They are currently collaborating closely with Royal HaskoningDHV – an international, non-listed engineering consultancy firm with headquarters in Amersfoort, Netherlands – for slicing of structural elements.
“At DSM we believe that FGF is a critical technology to address the need for manufacturing structural and large-size components using highly filled polymers at competitive production lead times,” said Pieter Leen, Application Development Specialist Additive Manufacturing at DSM. “Nedcam provides an important link between product development and market demand and their printing activities will help accelerate the adoption of additive manufacturing.”
There is also an added sustainability benefit to the cooperation, as the two companies aim to drive production towards more sustainable and circular processes to realize their common ambition. Nedcam currently produces plugs and molds from various materials, including glass fiber reinforced composites and steel, often for single or limited use, resulting in tons of waste every year. Instead, FGF production using recyclable materials offers a route to a more sustainable process.
DSM considers the FGF 3D printing method, in which granular plastics are melted and fed through a nozzle onto a platform, ideal for large scale applications since FGF printers have been created to print products several meters high, wide and long. FGF technologies are considered more effective than the traditional Fused Filament Fabrication (FFF), since they use raw plastic particles or granules which are more easily available and cheaper, instead of filament, to 3D print objects.
In fact, the adoption of large-format polymeric pellet-based additive manufacturing (AM) systems is increasing. FGF 3D printing is expected to play an important role in the future of the 3D printing industry, studies indicate, especially since the technology has the potential to leverage more sustainable processes by increasing the use of recycled polymers in 3D printing. According to Michigan Technological University researchers, the advantages of printing with recycled particles rather than filament will also lead to lower costs, and easier to print large objects.
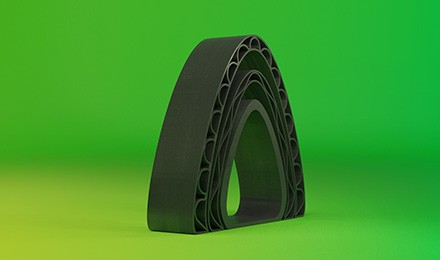
DSM’s Arnite AM8527, a sustainable PET material for fused granulate fabrication (FGF) AM. (Image courtesy of Royal DSM)
“We absolutely want to reduce the waste in our production process and go circular,” said Erwin van Maaren, Co-founder and Commercial Director at Nedcam. “By combining DSM’s 3D printing and thermoplastics expertise with our production knowledge and production facilities, we want to take the necessary steps toward a sustainable and fully circular model production process.”
Since its foundation, Nedcam has become the link between design and reality for many industries, by providing total solutions in shaping 3D technology, ranging from engineering, material selection, and tooling to special transport. Recently, the company added a CEAD AM Flexbot robotic 3D printer to its site in Heerenveen. Siemens and CEAD developed the hybrid 3D printing robotic arm as part of their ongoing partnership. The AM Flexbot, launched in November 2019 uses a large-scale industrial robotic arm as a motion platform and features CEAD’s single screw extruder unit mounted onto a Comau robotic arm, all controlled by Siemens’ Sinumerik CNC with Run MyRobot /Direct Control software.
Materials giant DSM has been forging collaborations and partnerships for years. Since announcing in 2017 that it was establishing a DSM AM organization, it became clear that the company was serious about 3D printing. DSM has gone on to collaborate with several companies to create 3D printing solutions for different industries, like its recently announced partnership with Youngstown, Ohio’s Juggerbot 3D to develop 3D printers and materials for pellet-based manufacturing. Continuing to design for circularity, by reducing waste, and pollution towards a more sustainable future, DSM and Nedcam’s collaboration will impact industrial large-format AM in the next decade.
Subscribe to Our Email Newsletter
Stay up-to-date on all the latest news from the 3D printing industry and receive information and offers from third party vendors.
Print Services
Upload your 3D Models and get them printed quickly and efficiently.
You May Also Like
The Market and Industry Potential of Multi-Material 3D and 4D Printing in Additive Electronics
Additive manufacturing leverages computer-based software to create components for products by depositing either dielectric or conductive materials, layer by layer, into different geometric shapes. Since its birth in the 1980s,...
3DPOD 262: Bio-inspired Design for AM with Dhruv Bhate, Arizona State University
Dhruv Bhate is an associate professor at Arizona State University. There, he looks at structures, materials, and design. Previously, he worked at PADT as well as in the semiconductor and...
3DPOD 261: Tooling and Cooling for AM with Jason Murphy, NXC MFG
Jason Murphy´s NXC MFG (Next Chapter Manufacturing) is not a generalist service; instead, the company specializes in making tooling. Using LPBF and binder jet, the company produces some of the...
3DPOD 260: John Hart on VulcanForms, MIT, Desktop Metal and More
John Hart is a Professor at MIT; he´s also the director of the Laboratory for Manufacturing and Productivity as well as the director of the Center for Advanced Production Technologies....