International researchers continue the trend toward overcoming challenges in bone regeneration, sharing the results of their study in the recently published “Tough magnesium phosphate-based 3D-printed implants induce bone regeneration in an equine defect model.” When doctors take on the task of rebuilding human bone, there is usually a need for material that can not only mimic human tissue but is also biodegradable, making it suitable for use with implants. Such materials must possess the proper mechanical properties, presenting further difficulty in many cases.
With current data pointing toward an annual increase of 10% for bone grafting procedures, medical scientists and researchers are more motivated than ever to develop new techniques and experiment with new materials—usually related to scaffolding. Typical scaffolds are composed of materials that can degrade like:
- Ceramics like hydroxyapatite, tricalcium phosphate, or bioglass
- Polmer-based materials like polycaprolactone, pollactide-co-glycolide
- Composites
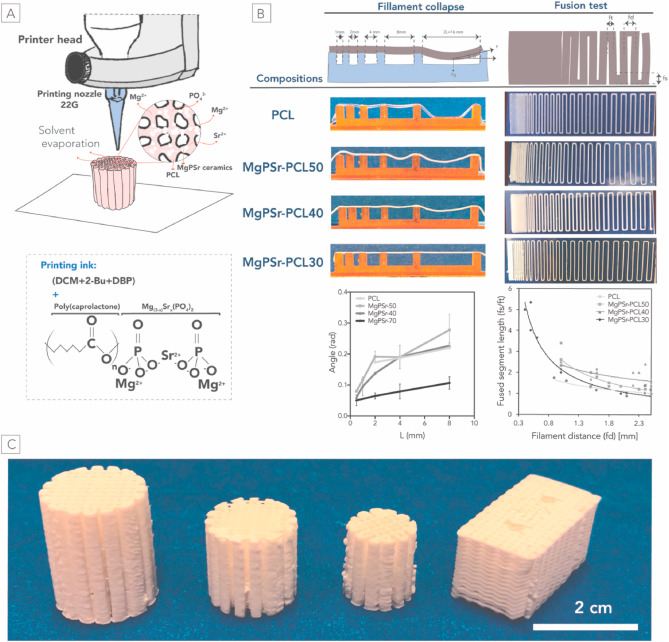
Preparation and printability characterization of the bioactive materials. A) Schematic illustration of the low temperature printing process and the composition of the ink. B) Printability evaluation. Filament test: different compositions extruded over a pillar support with different spacings. Effect of ceramics concentration on the angle of deflection θ, in radians, as a function of half the gap distance L, in mm (n = 3 for each group). Fusion test: Pictures from stereo microscopy after deposition on the glass slides (n = 3). The exponential fitting of the fused filament length is normalized by filament thickness as a function of the filament distance for the tested compositions. C) Designed and printed scaffolds with various shapes of MgPSr-PCL30.
A variety of different traditional techniques are generally used, leaving researchers still to deal with obstacles like inferior structures, constrictions related to mechanical properties, and challenges in creating scaffolds for defects above 10mm. In this study, the researchers turned to extrusion-based 3D printing with ceramics, while exploring previous work in 3D printing with bioceramics with hydroxyapatite and polycaprolactone or poly(lactic-co-glycolic acid).
Previous materials may have presented challenges due to a lack of load-bearing properties, leading the researchers to explore polymer-ceramic composites due to better mechanical properties; however, there can be issues with decreased osteoinductivity because of polymer masking and lower solubility. Magnesium phosphate cement (MPC) and metal ions in calcium phosphate (CPC) show better potential for bone regeneration though:
“Recently, magnesium phosphate (MgP) materials have captured increasing attention due to their high in vivo solubility and low tendency to transform into lower soluble CaP phases at physiological conditions,” stated the researchers.
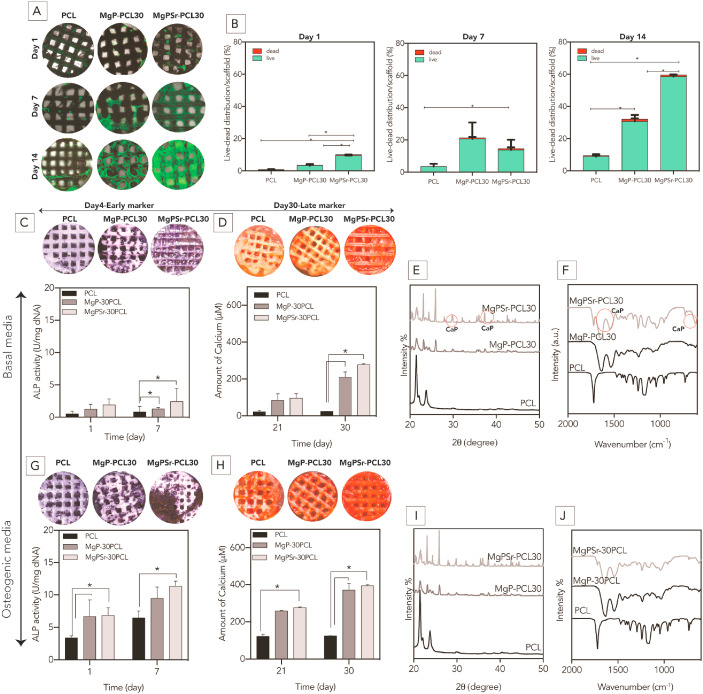
In-vitro assessment of bioactivity of the printed scaffolds. A) confocal images from the live-dead staining assay during 14 days culturing of eMSCs in basal media. B) Quantified results of the distribution of live and dead cells per scaffold. C and G) alkaline phosphatase (ALP) images of the printed samples. ALP activity levels were normalized to DNA content. D and H) Formation of calcified matrix by eMSCs investigated using Alizarin Red S staining after 30 days of culture. Quantified amount of calcified matrix evaluated by Alizarin Red S content on the 3D printed scaffolds using a colorimetric assay. Scale bars represent 1 mm. E and I) XRD and F and J) FTIR analysis of the scaffolds after culturing of eMSCs. Peaks corresponding to hydroxyapatite are marked with red circles. (For interpretation of the references to color in this figure legend, the reader is referred to the Web version of this article.)
Other ions like Sr2+, into CaP and MgP. materials may also allow for regeneration. In this study, the authors were able to 3D print scaffolds made from magnesium phosphate, controlling the necessary properties with the use of PCL, a common thermoplastic material used in bone regeneration. They also added small amounts of biologically active Sr2+ ions, evaluating the materials first in a basal and osteogenic medium (in vitro) and then in an equine tuber coxae defect model (in vivo).
The researchers used a 3D Discovery printer for extruding paste through a 22G conical nozzle, with dispensing pressure of 0.9 bar for continuous printing at room temperature. Cylindrical and rectangular samples of varying sizes were 3D printed for the study.
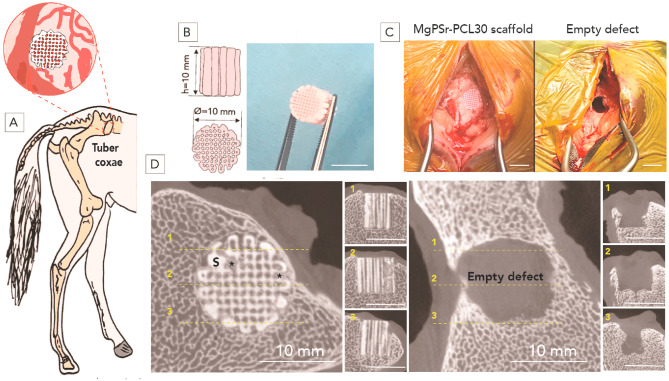
In vivo study preparation and implantation. A) Schematic representation of the implantation of cylindrical constructs in the equine tuber coxae. B) Drawing and photograph of the large-size printed implants (10 mm × 10 mm). C) Intra operative views of the surgical procedure, showing empty defect and defect filled with construct. D) μ-CT analysis of new bone formation after 6 months. Representative reconstructed images of longitudinal and transverse cross-sections of defects implanted with the MgPSr-PCL30 and empty defect after 6 months in vivo (scale bar = 10 mm).
Ultimately, MgPSr and PCL were found to substantially improve osteogenic response for the in vitro culture, and noted as “capable of effectively repairing a critical sized bone defect,” with the implant inside the equine tuber coxae models for six months. The 30 wt% PCL eliminated cracks and premature failure, a benefit of using ceramics in the presence of load-bearing sites. One of the most successful points of this study, however, was compressive mechanical properties of the MgPSr-PCL30 composites acting “in the range of native cancellous bone.”
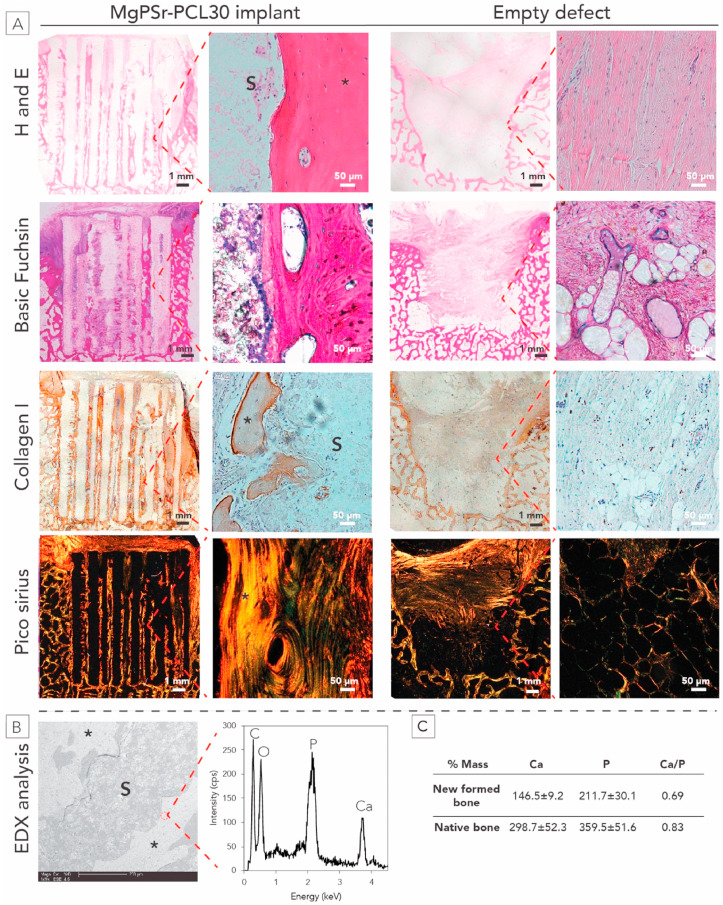
Histology assessment after 6-months in vivo study for equine model. A) Histological assessment of new bone (*) within the MgPSr-PCL30 scaffolds after 6 months. Representative hematoxylin and eosin, Basic fuchsin/methylene blue-stained MMA samples, immunohistochemical staining for collagen type I (brown region), and picrosirius red–stained tissue sections of defects filled by MgPSr-PCL30 scaffolds (S) and of empty defects. The scale bar is 50 μm. B) EDX analysis of newly formed bone. Representative BSE image of newly formed bone adjacent to the scaffold strut. C) Calcium and Phosphorous analysis for newly formed bone and native one. (For interpretation of the references to color in this figure legend, the reader is referred to the Web version of this article.)
Even after noted and rapid degradation in vitro, the implants exhibited suitable load bearing capacity. The scaffolding was found to be both osteoconductive and osteoinductive, supporting bone regeneration around the implant, while also “bridging” the bone defect.
“Interestingly, EDX analysis of the newly formed bone revealed a mineral composition and Ca to P ratio similar to the native equine bone, which confirmed the osteopromotive properties of the develop scaffold materials,” stated the researchers.
The results reflected strong, stable scaffolds and a viable system for tissue engineering and bone regeneration. Many other studies have been promising too—despite difficulties in bone regeneration activity—from research targeting areas like the jaw bone for regeneration, using other materials like titanium, and fabricating other complex scaffolds.
[Source / Images: “Tough magnesium phosphate-based 3D-printed implants induce bone regeneration in an equine defect model”]Subscribe to Our Email Newsletter
Stay up-to-date on all the latest news from the 3D printing industry and receive information and offers from third party vendors.
Print Services
Upload your 3D Models and get them printed quickly and efficiently.
You May Also Like
Johns Hopkins University Researchers Develop HyFAM Technology
Two scientists from Johns Hopkins University, Nathan C. Brown and Jochen Mueller, have developed a hybrid manufacturing technology they call HyFam, or Hybrid Formative Additive Manufacturing. Their work on this technology...
3D Printing G-Code Gets an Upgrade: T-Code
Good old G-Code still manages many 3D printers, great and small. Just like the STL, it’s a standard that enables collaboration while also holding the additive manufacturing (AM) industry back....
AM Rewind: The Biggest News and Trends of 2024
After a sluggish 2023, driven by persistent inflation and geopolitical tensions, 2024 has seen some recovery. Economic growth climbed from about 2.8 percent in 2023 to a modest 3.2 percent...
Metal Wire 3D Printer OEM ValCUN Announces Plans for 2025 Expansion
ValCUN, a Belgian original equipment manufacturer (OEM) of wire-based metal additive manufacturing (AM) hardware, has announced that the company has entered the next phase of its growth trajectory, making key...