Exemplifying the wide-ranging versatility of 3D printing, researchers have integrated the technology for accompanying scientific photography, detailing their recent study in “Illuminating nature’s beauty: modular, scalable and low-cost LED dome illumination system using 3D printing technology.”
Research may be vital to scientific advancement, but without a suitable presentation, it could mean very little to anyone. This begins with excellence in photography but also relies heavily on lighting. Currently, dome-style illumination systems are most commonly preferred by scientists showing their work—whether in taxonomy, morphology, systematics, natural history collections, or more. There are drawbacks though, due to lack of affordability and ease in use, leading the authors to explore 3D printing for a less expensive, modular LED dome design with the following features:
- Sliding table for arranging objects inside the dome
- Optional iris diaphragm for improved lighting source
- Battery for use in the field

Dome parts: (A) small sized dome (sd), medium sized dome (md), large sized dome (ld); (B) dome powered by battery box; (C) bottom cover plate (bcp), inlays black and white (ib, iw), iris diaphragm dome (idd), light shielding ring (lr), plain baseplate (pb), plain dome (pd), sliding table (st), sliding table baseplate (stbp); (D) small dome with LED ring; (E) power supply unit.
Samples were 3D printed on the Prusa i3 MK3S using PLA. After discarding and re-working several iterations for the dome, the authors added an LED strip for lighting that was flexible, adhesive, and fitted to the baseplate. Much less assembly was required, and “little to no” soldering was necessary. Ultimately, one SMD LED ring (40 mm diameter) was used for lighting, powered by a DC coaxial connector:
“We tried to design our own LED setup to assemble as many LED’s as possible in the small sized dome, by connecting single SMD LED’s with enameled copper wire and the needed resistors. However, this procedure is not beneficial and too time consuming,” explained the authors.
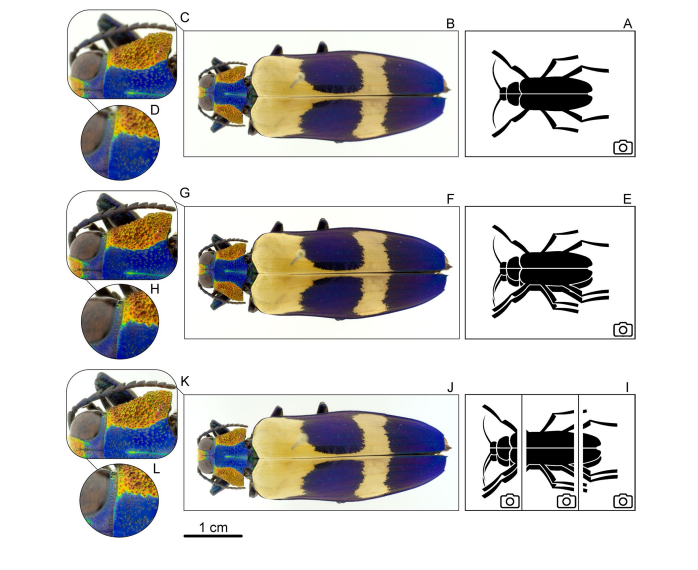
The beetle Chrysochroa buqueti (Coleoptera: Buprestidae), dorsal overview and two further magnifications respectively, left is anterior: (B–D) single image (as pictogram in A); (F–H) 5 focus-layer images stacked (as pictogram in E); (J–L) 3 images stacked, 5 focus layer-images stitched respectively (as pictogram in I)
In comparison to similar lighting created in recent, previous research, this technique for creating a 3D printed dome provides the necessary affordability, accessibility, and reproducibility. The researchers expect it to be helpful for students and labs, and especially when there is an emphasis on budget.
FDM 3D printing is recommended, with printer settings provided by the researchers; however, users engaged in 3D printing these parts may need to adjust the temperature for the printer bed or extruder, as well as experimenting with settings for the extrusion multiplier to control the amount of filament used. Layer thickness must be taken into consideration too: while higher thickness means decreased resolution, 3D printing is faster. Lower layer thickness means better resolution but more time in production.
“If no 3D-printer is at hand, there are many local or online 3D-printing services, that can be commissioned, to print our provided models from a wide range of materials and in customized sizes,” stated the authors.
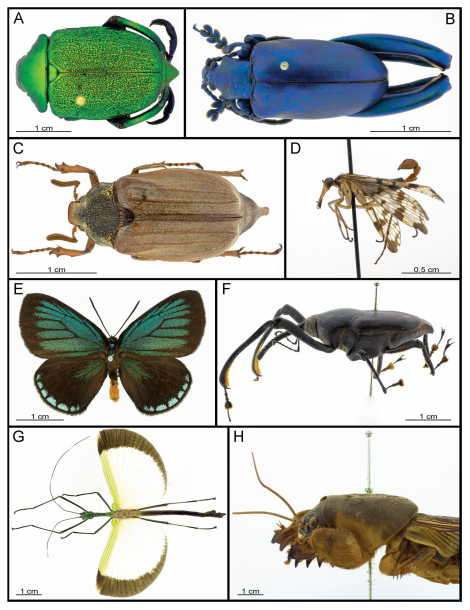
Insect specimens, lef is anterior, except for E (up is anterior) : (A) Chrysophora chrysochlora (Coleoptera: Scarabaeidae), dorsal view; (B) Sagra longicollis (Coleoptera: Chrysomelidae), dorsal view; (C) Melolontha melolontha (Coleoptera: Scarabaeidae), dorsal view; (D) Pannorpa communis (Mecoptera: Panorpidae), lateral view; (E) Eumaeus atala (Lepidoptera: Lycaenidae), dorsal view; (F) Macrochirus vittatus (Coleoptera: Dryophthoridae), lateral view; (G) Eurynecrosia nigrofasciata (Phasmatodea: Lonchodidae), dorsal view; (H) Gryllotalpa gryllotalpa (Orthoptera: Gryllotalpidae), lateral view.

Other specimens: (A) Perca fuviatilis (Perciformes: Percidae), lateral view, left anterior; (B) Psammechinus miliaris (Camarodonta: Echinidae), aboral view; (C) Scyliorhinus canicula (Carcharhiniformes: Scyliorhinidae) egg; (D) Argyropelecus spec. (Stomiiformes: Stemoptychidae), lateral view, left anterior; (E) Talpa europaea (Eulipotyphla: Talpidae), lateral view, left anterior; (F) Jackdaw egg (Passeriformes: Corvidae); (G) Epitonium (Gastropoda: Epitoniidae) spec.
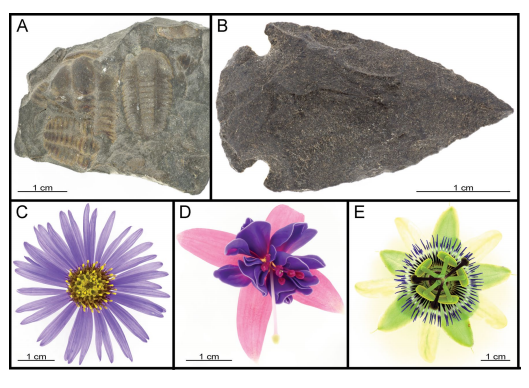
Objects and fowers: (A) Ellipsocephalus hof (Ptychopariida: Ellipsocephalidae); (B) Replica of the tip of an arrow; (C) Aster alpinus (Asterales: Asteraceae); (D) Fuchsia spec. (Myrtales: Onagraceae); (E) Passifora spec. (Malpighiales: Passiforaceae).
Subscribe to Our Email Newsletter
Stay up-to-date on all the latest news from the 3D printing industry and receive information and offers from third party vendors.
Print Services
Upload your 3D Models and get them printed quickly and efficiently.
You May Also Like
The Market and Industry Potential of Multi-Material 3D and 4D Printing in Additive Electronics
Additive manufacturing leverages computer-based software to create components for products by depositing either dielectric or conductive materials, layer by layer, into different geometric shapes. Since its birth in the 1980s,...
3DPOD 262: Bio-inspired Design for AM with Dhruv Bhate, Arizona State University
Dhruv Bhate is an associate professor at Arizona State University. There, he looks at structures, materials, and design. Previously, he worked at PADT as well as in the semiconductor and...
3DPOD 261: Tooling and Cooling for AM with Jason Murphy, NXC MFG
Jason Murphy´s NXC MFG (Next Chapter Manufacturing) is not a generalist service; instead, the company specializes in making tooling. Using LPBF and binder jet, the company produces some of the...
3DPOD 260: John Hart on VulcanForms, MIT, Desktop Metal and More
John Hart is a Professor at MIT; he´s also the director of the Laboratory for Manufacturing and Productivity as well as the director of the Center for Advanced Production Technologies....