We’ve seen 3D printed robots that are capable of completing a multitude of tasks, from tattooing a person’s arm and ringing a gong to vacuuming, building houses, and mowing the lawn. But robots that are able to perform complex motions, such as jumping, walking, and navigating different kinds of terrain, are either too expensive or too simple to do much good. But a new open source robot could change this.
Researchers from the NYU Tandon School of Engineering, its Machines in Motion Laboratory, and Germany’s Max Planck Institute for Intelligent Systems (MPI-IS) worked together to create a quadruped robot, named Solo 8, that’s roughly the size of a dog, quick and easy to assemble, comparatively low-cost, and not at all creepy. But the best thing about the robot is that it is open source, meaning other research labs can easily replicate and modify it.
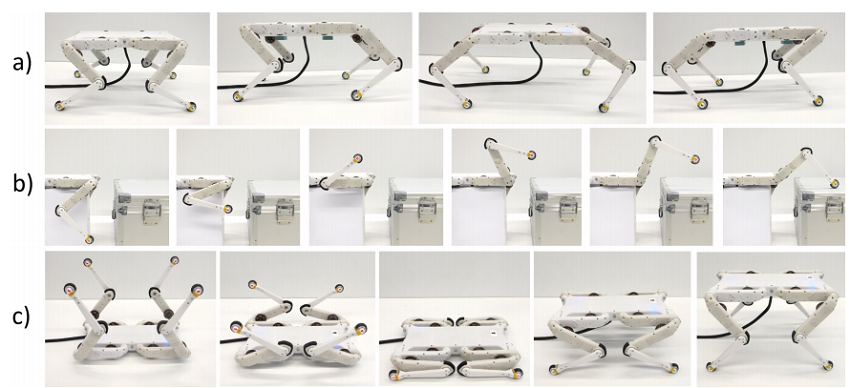
Example motion sequences: a) Legs can switch between all four knee configurations, b) with more than 360° hip joint rotation capability, and little space to navigate, legs can be rotated first backwards, and then onto a step, c) in case the robot falls onto its back, it can re-orient its legs, and stand up without rotating the trunk.
Ludovic Righetti, associate professor of electrical and computer engineering and mechanical and aerospace engineering at NYU Tandon, led the collaborative Solo 8 team in its mission to make teaching and researching robotics more accessible. Backed by the Open Dynamic Robot Initiative, Righetti and MPI-IS investigators Felix Grimminger and Alexander Badri-Spröwitz began the project in 2016 with funding from Righetti’s ERC Starting Grant.
Fast forward to present day, and a paper about their work, which was accepted for publication in the Robotics and Automation Letters journal, was recently presented at the virtual International Conference on Robotics and Automation (ICRA).
“We present a new open-source torque-controlled legged robot system, with a low-cost and low-complexity actuator module at its core,” the abstract states. “We also present a novel foot contact sensor suitable for legged locomotion with hard impacts. A 2.2 kg quadruped robot with a large range of motion is assembled from eight identical actuator modules and four lower legs with foot contact sensors. Leveraging standard plastic 3D printing and off-the-shelf parts results in a lightweight and inexpensive robot, allowing for rapid distribution and duplication within the research community.”
Solo 8 acts like a much costlier robot: its actuated joints and torque-controlled motors allow it to walk in several directions, jump, and pick itself back up if it falls over.
“Solo has some novel capabilities that we are interested to explore in the future. It has an extensive range of motion, for example,” Grimminger stated. “When the robot falls on its back, it can configure the legs the other way and just stand up. Or it can jump up to reach 65 cm from a standing height of 24 cm.”

Brushless actuator module (a) assembled, (b) individual parts. BLDC motor (1), two-part 3D printed shell structure (2), high resolution encoder (3), timing belts (4), and output shaft (5). Brushless motor (6), optical encoder (7), timing belts (8), bearings (9), fasteners (10), machined parts (11) and 3D printed parts (12). Except for 11, all parts are off-the-shelf or 3D printable. The motor shaft and the pulleys (11) can be machined from stock material. (c) Lower leg and foot contact switch components.
Weighing in at a little over two kilograms, Solo 8 has a higher power to weight ratio than most other quadruped robots, which makes it safer and easier to handle in a laboratory, and you can even carry it in a backpack. All of its components can be purchased, or 3D printed, and the team has made the construction files available for free on GitHub under the BSD 3-clause license. Other researchers will benefit from the team’s decision to design the robot as an open source platform, as they will able to gather and share data from their own experiments, leading to faster progress in the field of robotics.
Righetti said, “Already many universities have approached us, and wish to make a copy of our robot and use it as a research platform.”
One example is the Empirical Inference Department at MPI-IS using the platform to develop robotics fingers capable of manipulating objects. Other potential research areas include extremely dynamic locomotion, such as parkour behavior; investigating animal-based limb movement; environmental manipulation, such as pushing buttons; integrating robots with advanced communication technology; and reinforcement learning for dynamic and complex behaviors.
“Our robot platform is a great base to quickly prototype and build high-performance hardware. In return we benefit, because other researchers can contribute to the project; for example colleagues at the LAAS-CNRS in France have developed an electronic board to help communicate with the robot over WiFi. Also, complex control and learning algorithms can be rapidly tested on the platform, decreasing the time from idea to experimental validation,” Righetti explained. “It greatly simplifies our research, and our open-source approach allows us to compare algorithms with other laboratories. In my lab here in New York, we have developed very efficient motion optimization algorithms, but testing them on a complex, heavy robot can easily take half a year of work for several researchers, while this can be done more easily with Solo. That was a big deal for us.”
So, how did the team go about creating Solo 8? Badri-Spröwitz said it took “a wide range of expertise” and several years of hard work:
“Our platform is the combined knowledge of several teams. Now any lab worldwide can go online, download the files and print the parts, and buy the remaining components from the catalog. And everybody can add extra features, within a few extra weeks. Done – you’ve got yourself a world-class robot.”
But all that work paid off, as Badri-Spröwitz estimates other research teams can easily create their own versions of Solo 8 for only a few thousand euros. The robot is named for its eight actuated joints, which allow each leg to change its length and angle; however, tests on the latest version of the robot were conducted with three degrees of freedom per leg, for a total of 12. This makes it much more versatile, and able to perform more complex behaviors, such as stepping sideways.
It also features torque-controlled motors, which act like an animal leg’s elastic tendons and muscles — this allows Solo 8 to move with “a spring-like behavior.”
“Note that the robot uses virtual springs, not mechanical springs. And as virtual springs, they can be programmed,” Badri-Spröwitz explained. “You can, for instance, adjust the spring stiffness from soft to hard, which is interesting because we see variable stiffness in humans and animals, and with adjusted stiffness the robot achieves adaptive and robust locomotion behavior.”
Open source projects like this one are really in line with the ethos of the maker community – by sharing our knowledge with others, rather than keeping it to ourselves, we can work together to achieve great things, and even save lives.
Subscribe to Our Email Newsletter
Stay up-to-date on all the latest news from the 3D printing industry and receive information and offers from third party vendors.
Print Services
Upload your 3D Models and get them printed quickly and efficiently.
You May Also Like
Nikon SLM Solutions Sells SLM 500 to Primary Weapon Systems to Expand Suppressor Production
Primary Weapons Systems (PWS) is a Boise, Idaho-based manufacturer of suppressors, firearms, and related components. A subsidiary of Vigilant Gear and a sister company to aftermarket Glock slide manufacturer Lone...
3DPOD 261: Tooling and Cooling for AM with Jason Murphy, NXC MFG
Jason Murphy´s NXC MFG (Next Chapter Manufacturing) is not a generalist service; instead, the company specializes in making tooling. Using LPBF and binder jet, the company produces some of the...
HP and Firestorm Labs Form Partnership to Use Multi Jet Fusion 3D Printers in Deployable Factories
HP Inc., maker of a range of additive manufacturing (AM) solutions including the Multi Jet Fusion (MJF) ecosystem, has announced a partnership with Firestorm Labs, a developer of containerized, deployable...
3D Printing News Briefs, July 2, 2025: Copper Alloys, Defense Manufacturing, & More
We’re starting off with metals in today’s 3D Printing News Briefs, as Farsoon has unveiled a large-scale AM solution for copper alloys, and Meltio used its wire-laser metal solution to...