3D printing in construction continues to expand in Japan, driven by the need for more efficient, affordable processes, and higher-performance materials overall. In developing new technology for the construction industry, a research group from Gifu University (Gifu, Japan) has been joined by:
- Construction Technology Research Institute
- Sumitomo Osaka Cement
- Shimizu Construction
- NIPPO
- Maruei Concrete Industry
- FTS
Along with innovation in dry and wet spraying, the research and development group has now built a printer for on-site work, which the group states offers multiple benefits in combination with information communication technology (ICT) equipment. Typical modes of construction worldwide involve molding poured cement into shape using formwork. In Japan, the Ministry of Land, Infrastructure, Transport, and Tourism recommends pre-casting with factory-made products; however, the researchers continue to move forward in refining technology—allowing a shift and employing a novel technique.
Undoubtedly, the research and development group is headed in the right direction with a focus on 3D printing. For industrial users—and especially in construction—the benefits are considerable. Greater affordability is possible on numerous levels, due to less time spent in production, transportation, less waste in materials, and reduced need for human laborers as well (becoming even more relevant with the greater use of more complex robotics).
With dry spraying, materials must be ‘separately conveyed’ and then sprayed from the nozzle tip, while wet spraying involves premixed materials being sprayed from the nozzle tip. With the team’s unique hybrid system, they are able to bring together all the benefits of both.
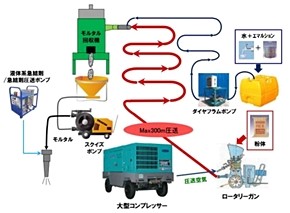
Outline of hybrid spraying system (Source: Gifu University, Research Institute of Construction Technology, Sumitomo Osaka Cement, Shimizu Construction, NIPPO, Maruei Concrete Industry, FTS)
The new process works in the following steps:
- 3D modeling is performed on-site with spray nozzle attached to bucket tip of the ICT construction machine.
- Infinite plane design data is created, controlling the horizontal axis.
- Height is adjusted with an offset function.

Experiments at the Construction Technology Research Institute. Formwork from the left, wall Source: Gifu University, Research Institute of Construction Technology, Sumitomo Osaka Cement, Shimizu Construction, NIPPO, Maruei Concrete Industry, FTS
“By using such ICT construction machinery technology, in the experiment of the Construction Technology Research Institute, we succeeded in directly outputting 3D concrete structures assuming a formwork (pillar) with a height of 1.5 meters and a wall with a height of 1 meter,” explained the researchers.
There are plans to deal with difficulties in transportation of materials, which is often an issue in the construction industry—for numerous applications. The team currently envisions “a buried formwork for construction of concrete structures” in their first phase, with newly applied accuracy and management in the second phase—to be used in abutments, piers, and more. In the third phase, they will be working on infrastructure like bridges, and other structures like railings.

Expected future application of bridge superstructure Source: Gifu University, Construction Technology Research Institute, Sumitomo Osaka Cement, Shimizu Construction, NIPPO, Maruei Concrete Industry, FTS
As the research and development group moves from the conceptual phase to actually completing all three phases, it will be interesting to see the end results. While there are true benefits for use in the building industry, many have expressed skepticism as projects are slow to get off the ground, whether in building homes or entire villages.
Subscribe to Our Email Newsletter
Stay up-to-date on all the latest news from the 3D printing industry and receive information and offers from third party vendors.
Print Services
Upload your 3D Models and get them printed quickly and efficiently.
You May Also Like
Havaianas Collaborates with Zellerfeld to Launch 3D Printed Flip-Flops
The shoe of the summer is undoubtedly the flip-flop. Easy on, easy off, your feet won’t get sweaty because there’s not much material, and they’re available in a veritable rainbow...
UCLA Researchers Develop 3D Printed Pen that May Help Detect Parkinson’s Disease
Diagnosing Parkinson’s disease is difficult. Often, early symptoms of the progressive neurological condition may be overlooked, or mistaken for signs of aging. Early diagnosis can help save lives and improve...
Printing Money Episode 30: Q1 2025 Public 3D Printing Earnings Review with Troy Jensen, Cantor Fitzgerald
Printing Money is back with Episode 30, and it’s that quarterly time, so we are happy and thankful to welcome back Troy Jensen (Managing Director, Cantor Fitzgerald) to review the...
Heating Up: 3D Systems’ Scott Green Discusses 3D Printing’s Potential in the Data Center Industry
The relentless rise of NVIDIA, the steadily increasing pledges of major private and public investments in national infrastructure projects around the world, and the general cultural obsession with AI have...