Consumption of energy around the world and never-ending demand leads researchers to continue searching for clean, sustainable alternatives. In the quest to slow global warming, we must begin to prevent emissions, too. The list of options is actually quite long for avoiding extended pollution and making sweeping change, but the challenges lie in global awareness and the ability to act.
In recent years, 3D printing has been used far beyond its original intentions for rapid prototyping as researchers continue to harness the technology in a wide range of projects and innovations impacting the energy industry, from energy harvesting wearables to storing wind energy, and a variety of techniques for making 3D-printed batteries.
Now, expert market research shows that 3D-printed fuel cells—very similar to batteries but they convert fuel rather than storing it—are being developed for greater optimization and ruggedness in structures too. Fuel cells and electrolyzers may act as the catalyst for substantial change in the shift to zero emissions. While fuel cells can transform hydrogen into electricity, electrolyzers can change water into hydrogen, when accompanied by electricity.
These new systems offer enormous potential for energy change as they are capable of serving as ‘massive storage’ for electricity, and they can also decarbonize intense areas of energy usage. With 3D printing, industrial users are able to take advantage of savings on the bottom line, the ability to fabricate more complex geometries, and also the possibility to create products never before possible with conventional techniques.
While previously solid oxide fuel and electrolysis cells (SOFCs and SOECs) have been considered efficient for use, development and manufacturing is also cost-prohibitive, and it is difficult to produce complex geometries that may be desired. It looks like this is about to change, however, according to a recent press release from IDTechEx. The market researcher firm indicated that approval has been received for a novel SOFC system this year via a rapid assessment meant to fast-track development and subsequent use. Recent industry news from the same source also informs us that South Korea is accelerating its investments in hydrogen fuel cells for alternative energy.
Solid oxide electrolysis cells (SOES) are gaining ground as new sources of energy too. Also acting as streamlined converters of energy, they are known to offer better yields in production, and use less electricity. As of this year, a SOFC was fabricated via SLA 3D printing, marking a groundbreaking move not within digital fabrication, but also the energy industry.

V–j curves of the planar and corrugated cells measured in fuel cell (a) and co-electrolysis modes (b) at 900 °C. Corresponding Nyquist plots from EIS measurements are represented for the fuel cell at 0.7 V (c) and co-electrolysis cell at 1.3 V (d) [‘Image from ‘3D printing the next generation of enhanced solid oxide fuel and electrolysis cells’]
“Among others, electroceramic-based energy devices like solid oxide fuel and electrolysis cells are promising candidates to benefit from using 3D printing to develop innovative concepts that overcome shape limitations of currently existing manufacturing techniques,” state the authors.
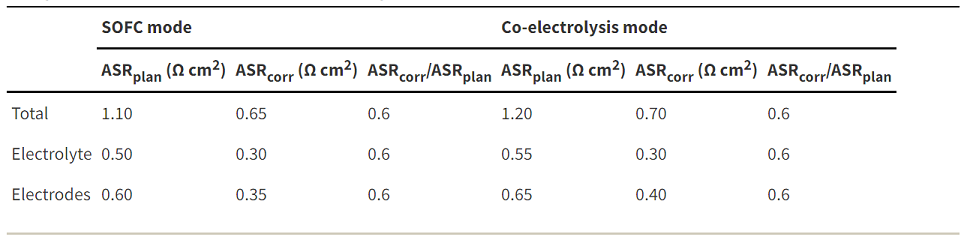
Values of area-specific resistance (total, electrolyte and electrode contributions) obtained from equivalent circuit fitting of the EIS spectra for both planar and corrugated cells measured in fuel cell and co-electrolysis mode at 900 °C. [‘Image from ‘3D printing the next generation of enhanced solid oxide fuel and electrolysis cells’]
“Not only did we demonstrate for the first time that we can 3D-print a battery, we demonstrated it in the most rigorous way,” said Jennifer Lewis, Ph.D., senior author of the recent study.
It’s also worth highlighting the work of Keracel, which claims to have developed a method for 3D printing solid state batteries using a binder jetting technique. The company has partnered with Musashi Seimitsu Industry, a Japanese automotive supplier.
What do you think of this news? Let us know your thoughts! Join the discussion of this and other 3D printing topics at 3DPrintBoard.com.
[Source: IDTechEx / Images: ‘3D printing the next generation of enhanced solid oxide fuel and electrolysis cells’]Subscribe to Our Email Newsletter
Stay up-to-date on all the latest news from the 3D printing industry and receive information and offers from third party vendors.
Print Services
Upload your 3D Models and get them printed quickly and efficiently.
You May Also Like
The Market and Industry Potential of Multi-Material 3D and 4D Printing in Additive Electronics
Additive manufacturing leverages computer-based software to create components for products by depositing either dielectric or conductive materials, layer by layer, into different geometric shapes. Since its birth in the 1980s,...
3DPOD 262: Bio-inspired Design for AM with Dhruv Bhate, Arizona State University
Dhruv Bhate is an associate professor at Arizona State University. There, he looks at structures, materials, and design. Previously, he worked at PADT as well as in the semiconductor and...
3DPOD 261: Tooling and Cooling for AM with Jason Murphy, NXC MFG
Jason Murphy´s NXC MFG (Next Chapter Manufacturing) is not a generalist service; instead, the company specializes in making tooling. Using LPBF and binder jet, the company produces some of the...
3DPOD 260: John Hart on VulcanForms, MIT, Desktop Metal and More
John Hart is a Professor at MIT; he´s also the director of the Laboratory for Manufacturing and Productivity as well as the director of the Center for Advanced Production Technologies....