Metal 3D printing materials developer and supplier Elementum 3D, founded in 2014 by Dr. Jacob Nuechterlein, works to expand the selection of metal materials for additive manufacturing (AM) through the introduction of advanced composites, metal alloys, and superalloys, along with development of optimized processes, such as its core Reactive Additive Manufacturing (RAM) technology. Now, the company has announced that it has been granted patents in the United States, Canada, and Australia for its RAM process.
“Our revolutionary technology advances metals development for additive manufacturing at an unprecedented pace,” explained Dr. Nuechterlein in a press release. “It gives engineers an extra degree of freedom they’ve never experienced, inspiring them to bring into existence new and innovative applications.”
In order to increase adoption of AM, the industry needs more choices when it comes to 3D printable metal materials. That’s where companies like Elementum 3D—which recently received its ISO 9001:2015 certification for quality management practices and systems—come in. The Colorado-based firm has a knack for creating custom materials that work for applications in different industries. It also sells feedstock powders with accurate printing parameters that can be customized for even more applications.
“We’re continuously looking for new solutions to help companies around the world, in their quest to increase product strength, durability, and reduce weight,” the Elementum 3D website states.
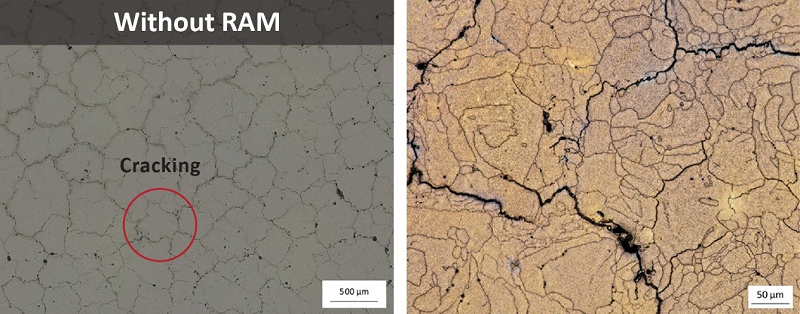
Unmodified “standard” 6061 aluminum alloy after printing by laser powder bed fusion showing large grains and an extensive network of intergranular cracking. The left image is unetched and the right micrograph is etched with Weck’s reagent and taken at higher magnification.
The company’s RAM process is used to make high-performance metal alloy powders for 3D printing based on previously established wrought alloys, such as aluminum 1000, 2024, 6061, 7050, and 7075, which was not possible with conventional manufacturing. So, RAM technology actually helps grow the library of possible AM materials, and, in using it, Elementum 3D has come up with a new range of laser powder bed fusion (LPBF) materials that have much better properties in comparison to their corresponding wrought alloy materials.
Because of the risk of hot tearing, or solidification cracking, it was impossible to 3D print many popular, strong, wrought aluminum alloys; the end parts would have poor mechanical properties. But, with RAM, sub-micron inoculants form in the melt pool. These, in turn, nucleate the aluminum grains in order to create an equiaxed microstructure (having approximately equal dimensions in all directions), which results in high performance and good printability.
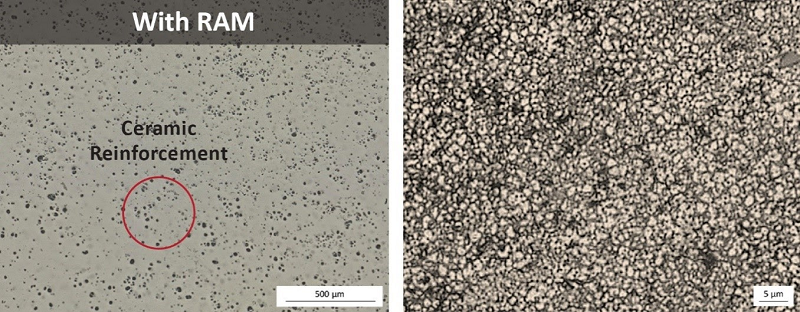
L-R: Elementum 3D’s A6061-RAM2 aluminum alloy showing a crack-free microstructure with the darker phase comprising reinforcing particles, and the very fine (1-2 µm) aluminum grains revealed after etching with Weck’s reagent in the higher magnification image.
In the image above, you can easily see that the A6061-RAM2 3D-printed material has a microstructure with no cracks, and as the company states in its release, “a dispersion of nucleating and reinforcing particulates.”
With the issuance of these patents, Elementum 3D is purporting to democratize materials freedom, and getting rid of material compromises, by making the 3D printable versions of its alloys easily available to the industry. By combining popular traditional materials that previously could not be 3D printed and new materials, like those enabled by RAM technology, with additive manufacturing, the company is speeding up the establishment of new applications for the 3D printing world.

L-R: Unmodified “standard” 2024 aluminum alloy without RAM addition exhibits columnar grain growth, and Elementum 3D’s A6061-RAM2 aluminum alloy with RAM addition exhibits ductal behavior.
Discuss this story and other 3D printing topics at 3DPrintBoard.com or share your thoughts in the Facebook comments below.
(Source/Images: Elementum3D)
Subscribe to Our Email Newsletter
Stay up-to-date on all the latest news from the 3D printing industry and receive information and offers from third party vendors.
Print Services
Upload your 3D Models and get them printed quickly and efficiently.
You May Also Like
The Market and Industry Potential of Multi-Material 3D and 4D Printing in Additive Electronics
Additive manufacturing leverages computer-based software to create components for products by depositing either dielectric or conductive materials, layer by layer, into different geometric shapes. Since its birth in the 1980s,...
3DPOD 262: Bio-inspired Design for AM with Dhruv Bhate, Arizona State University
Dhruv Bhate is an associate professor at Arizona State University. There, he looks at structures, materials, and design. Previously, he worked at PADT as well as in the semiconductor and...
3DPOD 261: Tooling and Cooling for AM with Jason Murphy, NXC MFG
Jason Murphy´s NXC MFG (Next Chapter Manufacturing) is not a generalist service; instead, the company specializes in making tooling. Using LPBF and binder jet, the company produces some of the...
3DPOD 260: John Hart on VulcanForms, MIT, Desktop Metal and More
John Hart is a Professor at MIT; he´s also the director of the Laboratory for Manufacturing and Productivity as well as the director of the Center for Advanced Production Technologies....