Emmanuel Segura-Cárdenas (Tecnologico de Monterrey, Escuela de Ingenieria y Ciencias) and Luis Fernando Velásquez-García (MIT) detail the results of a recent study in ‘Additively Manufactured Robust Microfluidics via Silver Clay Extrusion,’ explaining how they created a proof-of-concept microfluidic capable of decomposing hydrogen peroxide.
While most microfluidics are composed of silicone, such materials are incapable of handling high temperature or pressure—and they are not very compatible with solvents. Metal could be considered a suitable choice for the development of sturdy microfluidic devices, but currently, most of that technology is geared toward the creation of thin films and wafer bonding.
“In addition, fabrication approaches such as electric discharge micromachining [9] and micro milling [10] have been explored to implement metal microfluidics, but these manufacturing processes are very expensive, very slow, and require specialized tooling.”
Today, microfluidics are often accompanied by a variety of different 3D printing techniques, featured in research developing new sensors, organs-on-chips, and enhancing other processes like bioprinting. More standard 3D printing techniques like FFF have been used to develop microfluidics; however, most lack catalytic properties and can, again, only manage a slight amount of pressure or increase in temperature.
In this study, the researchers endeavored to use metal extrusion with clay, relying on silver clay to produce sturdy, affordable microfluidics. Silver clay is known to be compatible with many different microfluidics, offering benefits such as:
- High thermal features
- Electrical conductivity
- Chemical resistance
- Catalytic properties
Green and annealed samples were fabricated for testing in the study, with some concern over shrinkage. While the authors mainly attributed that to the printing process, they found the ‘mismatch between actual dimensions and intended dimensions’ to also be possible due to pressure on the clay syringe, a lack of XY pixels, or high-temperature annealing.
The researchers 3D printed step pyramids in 150 μm-thick and 200 μm-thick layers. In all, 15 structures were 3D printed, with the team measuring them randomly in four points within each step.
“The steps were centered around the vertical axis of the pyramid, and the separation between the edges of adjacent steps was set at 400 μm in the CAD files,” stated the authors. “Metrology of the test structures evidences linearity between the CAD and printed in-plane features for both green and annealed structures. On average, the dimensions of the green structures are 93% the CAD values, while the dimensions of the annealed structures are 81% the CAD values (i.e. the in-plane features of the annealed structures shrink about 13 percent from the dimensions of the green structures).
“No significant difference between measurements in the X and Y directions was found, although the structures made with the coarser slicing (i.e. 200 μm layer height) have associated less size variation and closer correspondence to the CAD files.”
Stair-like structures were also fabricated, measured, and characterized. Each sample featured nine steps on a 1 mm-thick base plate.
“In all cases, we found that the height of the base of the printed stair structure was equal to 0.98 mm instead of 1 mm, probably reflecting the out-of-plane offset typically present in the first layer printed by an FFF 3D printer,” stated the authors.
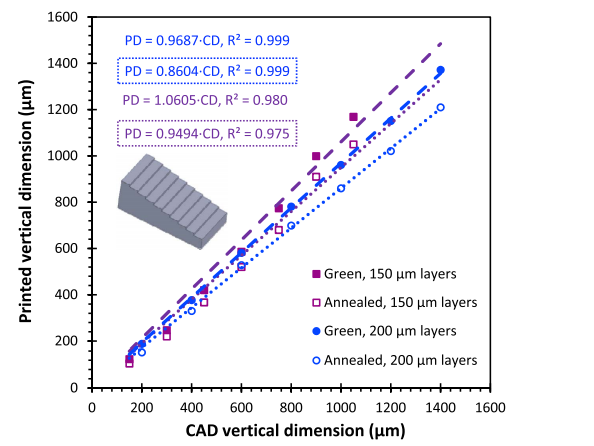
Out-of-plane printed dimension vs. corresponding CAD dimension, measured before and after annealing, of stairs-like test structures. In the least-squares fittings, PD = printed dimension, CD = CAD dimension. Solid markers denote data from green structures, while hollow markers denote data from annealed structures. Least-squares fittings of green data are dashed lines, while least squares fittings of annealed data are dotted lines.
Six long, narrow wire samples were printed and annealed for characterization of electrical resistivity.
“The least-squares fitting of the data shows a linear dependence between the length of the wire and its electrical resistance, in agreement with Ohm’s law,” stated the authors.
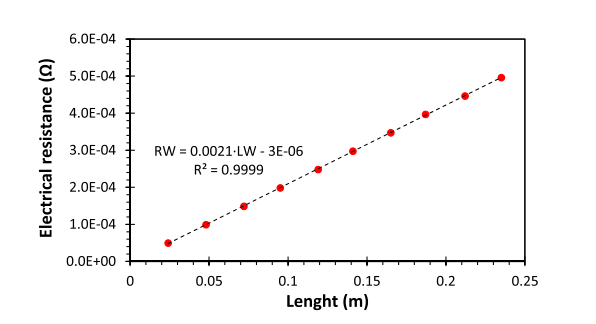
Electrical resistance versus probe separation for a printed and annealed wire. In the least-squares fitting, RW = electrical resistance, LW = wire length.
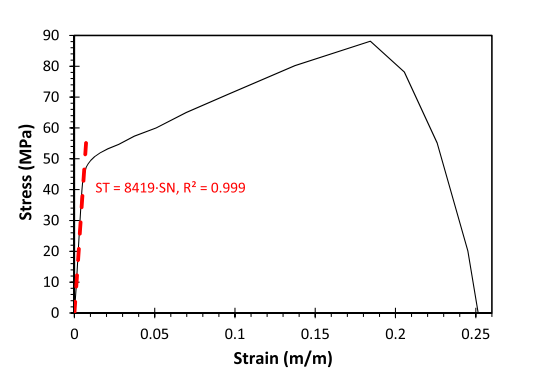
Stress vs. strain curve of printed and annealed sample. In the least square fitting, ST = uniaxial stress, SN = strain
In fabricating the microreactor, the researchers reported 12 minutes for printing, four hours for annealing, and a total cost of $25.
“The microreactor operates as predicted by the reduced-order modeling, attaining 87% decomposition efficiency for 5 μL/min flow rate of hydrogen peroxide with 30% w/w initial concentration,” stated the authors.

Summary of the effectiveness of hydrogen peroxide decomposition by the catalytic microreactor, i.e. final hydrogen peroxide concentration vs. initial hydrogen peroxide concentration. In all cases, the flow rate is 5 μL/min.
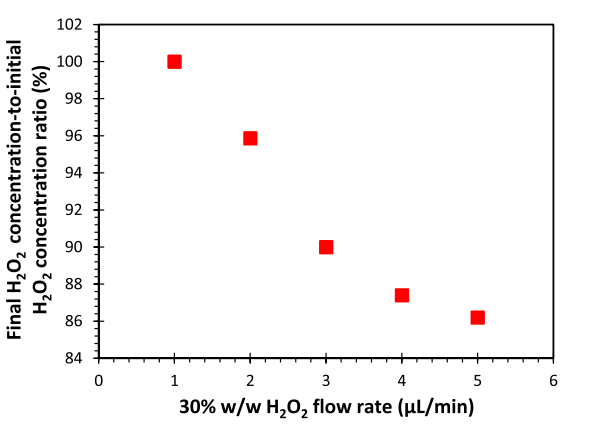
The ratio between final and initial hydrogen peroxide concentrations versus 30% w/w hydrogen peroxide flow rate for a microchannel with 600 μm by 600 μm cross-section and 2.5 cm length. Full decomposition of the hydrogen peroxide is achieved at 1 μL/min flowrate.
“The experimental results are in agreement with our modeling, including the complete decomposition of hydrogen peroxide with initial w/w concentration up to 1.8 % and 5 μL/min flow rate, and 87% decomposition efficiency when the initial hydrogen peroxide w/w concentration is increased to 30%,” concluded the researchers.
“The reported 3D printing method is compatible with heat transfer and microreactor microfluidic applications, e.g. compact heat exchangers, nanosatellite monopropellant rockets, and handheld steam generators for biological decontamination.”
What do you think of this news? Let us know your thoughts; join the discussion of this and other 3D printing topics at 3DPrintBoard.com.
[Source / Images: ‘Additively Manufactured Robust Microfluidics via Silver Clay Extrusion’]
Subscribe to Our Email Newsletter
Stay up-to-date on all the latest news from the 3D printing industry and receive information and offers from third party vendors.
Print Services
Upload your 3D Models and get them printed quickly and efficiently.
You May Also Like
Making 3D Printing Personal: How Faraz Faruqi Is Rethinking Digital Design at MIT CSAIL
What if your 3D printer could think more like an intelligent assistant, able to reason through a design idea, ask questions, and deliver something that works exactly the way the...
Reinventing Reindustrialization: Why NAVWAR Project Manager Spencer Koroly Invented a Made-in-America 3D Printer
It has become virtually impossible to regularly follow additive manufacturing (AM) industry news and not stumble across the term “defense industrial base” (DIB), a concept encompassing all the many diverse...
Heating Up: 3D Systems’ Scott Green Discusses 3D Printing’s Potential in the Data Center Industry
The relentless rise of NVIDIA, the steadily increasing pledges of major private and public investments in national infrastructure projects around the world, and the general cultural obsession with AI have...
Formlabs Teams Up with DMG MORI in Japan
In late June, Nick Graham, Chief Revenue Officer at Formlabs, announced on LinkedIn that the company had partnered with DMG MORI, one of the world’s leading machine tool companies, to...