Niek Groot takes on the topic of layer deposition in printing with resin, detailing his findings in ‘The influence of coater velocity on layer deposition in the 3D-printing process,’ a thesis submitted to Eindhoven University of Technology. With a focus on vat photopolymerization, the author investigates challenges that arise during layer deposition.
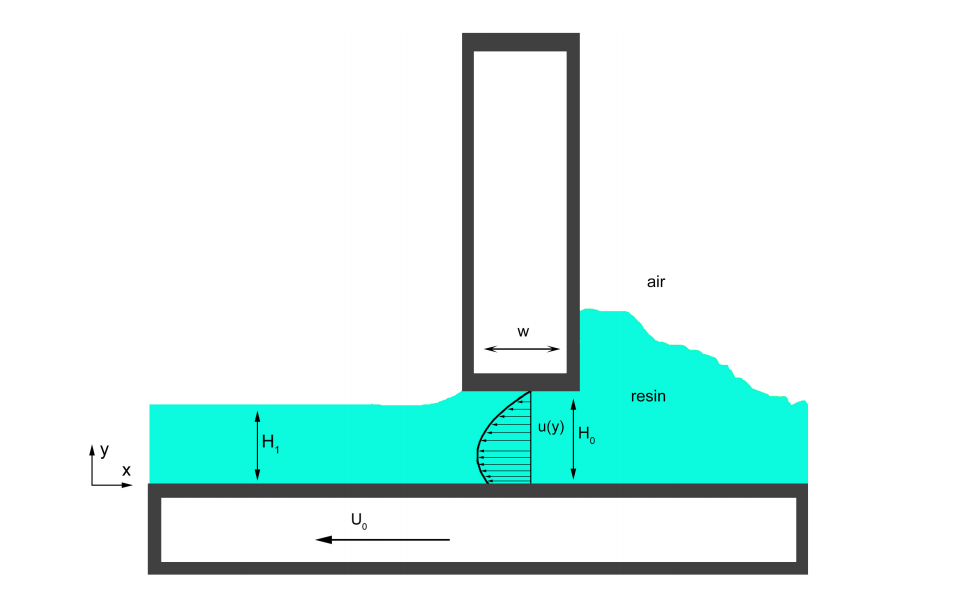
A schematic view of the process of layer deposition in which the velocity profile can be seen in between the coater blade and the bottom plate
Printing ceramics is becoming increasingly more popular with users around the globe, as they streamline techniques, experiment with new materials and composites, and create new molds and templates. Groot points out though that during printing, small deformations may occur. If this happens multiple times, leaving deformations stacked on top of each other throughout the 3D printed layers, there may be imperfections that threaten the integrity of the overall product.

An overview of the velocity profile beneath the coater and resin thickness depending on Π with courtesy to [3].
“The main parameters which are investigated are the coater height above the bottom plate and the coater velocity,” explains Groot, seeking to find setting adjustments that control flow and resin layers.
Layer adhesion is an issue many users must deal with, but when deformations are persistent throughout numerous layers there is greater concern due to the potential for structural failure and serious imperfections in shape.
“When looking at the effect of velocity on the height profiles for 100 µm, almost no difference can be seen when altering the coater velocity. However, when looking at the influence of the coater velocity on the height profile in case of a coater height of 150 µm and 200 µm, one can see a small decrease in the height profile for a faster coater velocity,” stated the author.
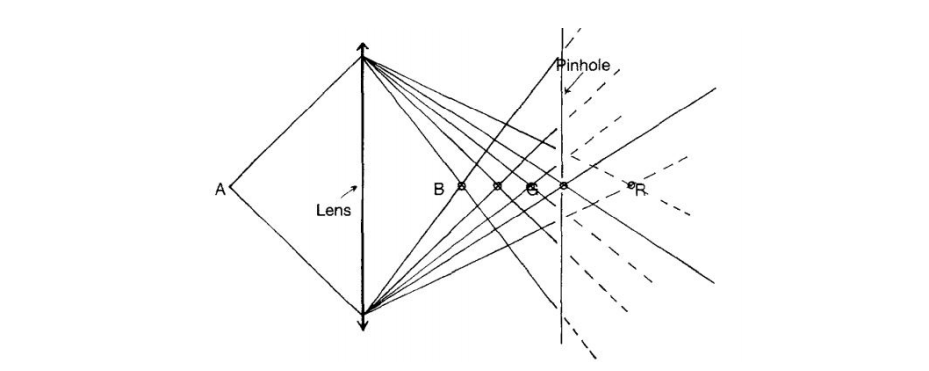
A schematic representation of chromatic aberration, where A is a polychromatic light source and B,G and R are the focal points of red, blue and green light. With courtesy to [2].

A schematic representation of the experimental setup which was used. The
confocal chromatic sensor, coater and resin injector are all mounted to the same movable stage (not to scale).
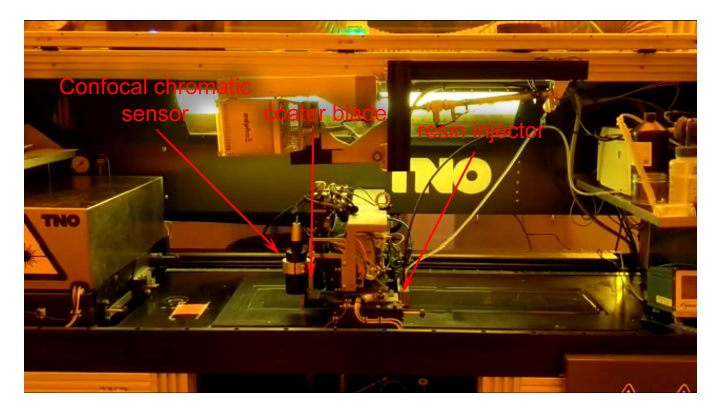
A picture of the Lepus Next Gen, where one can see the bottom plate and the movable stage containing the confocal chromatic sensor, coater and the resin injector. (Image: AMSYSTEMS)
“The results gathered by the Comsol model are very logical. The model resulted in a resin layer of exactly half the coater height above the bottom plate. This result is predicted by formula (8). This is also the case for most of the gathered data. Therefore, the model is in good accordance with the experimental data gathered,” concluded the researcher.
“As one can see, most results found during this thesis are not perfect. First, it can be clearly seen that the measurements for a coater height of 100µm, which can be found in Appendix B, are all negative. This is of course very unrealistic. Furthermore, it can be noticed that every measurement fluctuates more than what was expected. Sometimes these fluctuations were up to 50 µm. At first sight 50 µm does not seem a lot, however if it is stated that the thickest layer is 200 µm it can be easily seen that 50 µm is a very large fluctuation in this case.”
What do you think of this news? Let us know your thoughts! Join the discussion of this and other 3D printing topics at 3DPrintBoard.com.
[Source / Images: ‘The influence of coater velocity on layer deposition in the 3D-printing process’]Subscribe to Our Email Newsletter
Stay up-to-date on all the latest news from the 3D printing industry and receive information and offers from third party vendors.
Print Services
Upload your 3D Models and get them printed quickly and efficiently.
You May Also Like
3D Printing News Briefs, July 2, 2025: Copper Alloys, Defense Manufacturing, & More
We’re starting off with metals in today’s 3D Printing News Briefs, as Farsoon has unveiled a large-scale AM solution for copper alloys, and Meltio used its wire-laser metal solution to...
3DPOD 260: John Hart on VulcanForms, MIT, Desktop Metal and More
John Hart is a Professor at MIT; he´s also the director of the Laboratory for Manufacturing and Productivity as well as the director of the Center for Advanced Production Technologies....
3D Printing News Briefs, June 28, 2025: Defense Accelerator, Surgical Models, & More
In this weekend’s 3D Printing News Briefs, 3YOURMIND was selected to join an EU Defense Accelerator, and PTC has announced model-based definition (MBD) capabilities within Onshape. Finally, a study out...
EOS in India: AM’s Rising Star
EOS is doubling down on India. With a growing base of aerospace startups, new government policies, and a massive engineering workforce, India is quickly becoming one of the most important...