In the recently published ‘Improved performance of Differential Mobility Analyzers with 3D-printed flow straighteners,’ researchers from Cyprus and the Netherlands evaluated the development of a customized DMA meant to further streamline building enhanced flow straightening systems for aerosol management.
Combining both flow and an electrostatic field for classification, the DMA is a critical measurement tool for aerosol particles, whether at the nanometer or micron. Flow fields can be difficult to create due to the merging of two flows, often causing issues such as local eddies that may result in diminished performance. In attempting to overcome challenges, aerosol flow may be maintained ‘lower than ca. 10% of the sheath flow.’ Flow straighteners can also be made from a fabric mesh insulator that may cause disturbances but also prevent development of a comprehensive velocity profile.
In this study, the researchers fabricated nine different FSs samples, evaluating performance with a new 3D printed cylindrical DMA. Four were printed with ABS, and the others were made of small nylon meshes, to include Dacron (used as a reference).
“The performance of each FS was assessed by experimentally determining the Transfer Function (TF) of the DMA (i.e., the function giving the probability of a particle of a given electrical mobility, or size, that enters the instrument, to exit through its monodisperse particle outlet) when that was operated under different operating conditions,” stated the authors.
TF height corresponded to the greatest probability of particles entering the DMA, then exiting via the mono-disperse particle outlet. Deviations were measured in terms of height, with FWHM calculated for each FS and each sheath flow rate.
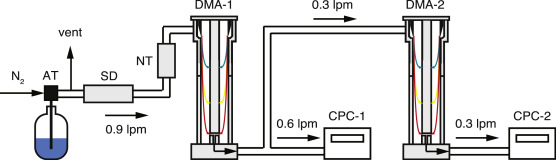
Schematic layout of the experimental set-up used to determine the performance of the test DMA (i.e., DMA-2) when different FS were employed. Key: AT: Atomizer; SD: Silica-gel diffusion drier; NT: Aerosol charge neutralizer; DMA: Differential Mobility Analyzer; CPC: Condensation Particle Counter.
Tests were performed with the following details:
- Use of nearly monodisperse particles, with diameter of ca. 50 nm
- Parametric version of the TF captured deviations between both measurements and predictions
- Fitting parameters affected TF regarding height and width
“In each TDMA experiment we obtain a set of N1 and N2 values, corresponding to the particle number concentrations measured downstream of DMA-1 and of DMA-2, respectively,” explained the authors. “Assuming that P0and CPCRatio remain constant throughout each experiment lasting for ca. 20 min, and that the TF of DMA-1 (i.e., Ω1 in Eq. 1) is constant and well-defined, the TF of DMA-2 (i.e., Ω2 in Eq. 1) is obtained by using a custom-made fitting algorithm (cf. supplement).
“It should be noted here that all FSs tested in this work created a small step (ranging from 0.7 to 1.0 mm in height) between their outer boundary (for the 3D-printed), or rings (for the fabric), and the walls of the inside electrodes of the DMA.”
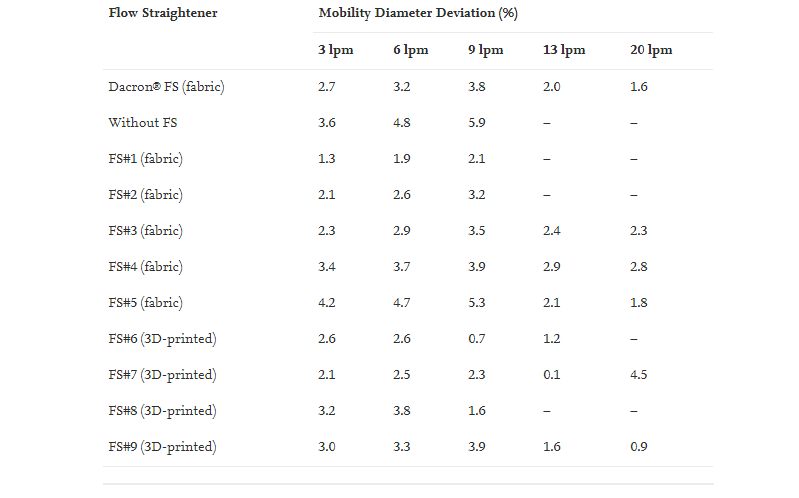
Summary of the results reflecting the sizing accuracy of the test DMA (expressed as % difference between measured and predicted particle size selected by the DMA) when using different FSs.
The researchers followed the Dacron FS used for reference, working to maintain suitable comparability, but noting that because all the samples resulted in steps of similar heights, results were ‘highly intercomparable.’ FS#9 outperformed most of the samples—even the one made from Dacron.
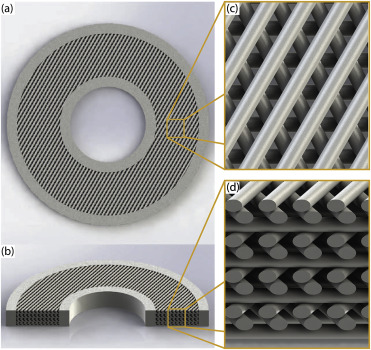
Render illustrations of FS#9, including top view (a), 3D cross-sectional view (b), as well as zoomed in views of the top (c) and of the cross-section (d) of the porous part of the FS.
“The good performance of the DMA when using FS#9, which was better even from the case when the reference Dacron® FS was employed at sheath flow rates up to 20 lpm, warrants for further investigating the use of 3D printed straighteners to run conventional and/or low-cost DMAs (Barmpounis, Maisser, Schmidt-Ott, & Biskos, 2015) at substantially higher sheath flow rates (e.g., up to 20 lpm) or with high-flow DMAs (Fernandez de la Mora & Kozlowski, 2013),” concluded the researchers. “For the latter, which are used for classifying nanoparticles (Wang et al., 2014) and even atomic clusters (Maisser, Barmpounis, Attoui, Biskos, & Schmidt-Ott, 2015) with high resolution, flow laminarization is rather important, typically requiring an additional pre-laminarization stage (Amo-Gonzalez & Perez, 2018).
“In summary, the measurements reported in this work show that 3D printing can be used to manufacture flow straighteners that exhibit better performance compared to traditional systems made of nylon fabrics. This has been verified by assessing deviations between the measured and the theoretical transfer function of a custom-made DMA employed in the tests. Interestingly, the 3D-printed straightener, having a triangular pore shape combined with a high surface density and larger pores compared to the other FSs investigated here, attributed to the test DMA a performance that compared better with theory. Considering the flexibility and ease of manufacturing of 3D printing, our results show that employing this technology to build flow straightness for DMAs, can improve their performance and thus is a better alternative compared to existing practices.”
What do you think of this news? Let us know your thoughts; join the discussion of this and other 3D printing topics at 3DPrintBoard.com.
[Source / Images: ‘Improved performance of Differential Mobility Analyzers with 3D-printed flow straighteners’]Subscribe to Our Email Newsletter
Stay up-to-date on all the latest news from the 3D printing industry and receive information and offers from third party vendors.
Print Services
Upload your 3D Models and get them printed quickly and efficiently.
You May Also Like
The Market and Industry Potential of Multi-Material 3D and 4D Printing in Additive Electronics
Additive manufacturing leverages computer-based software to create components for products by depositing either dielectric or conductive materials, layer by layer, into different geometric shapes. Since its birth in the 1980s,...
3DPOD 262: Bio-inspired Design for AM with Dhruv Bhate, Arizona State University
Dhruv Bhate is an associate professor at Arizona State University. There, he looks at structures, materials, and design. Previously, he worked at PADT as well as in the semiconductor and...
3DPOD 261: Tooling and Cooling for AM with Jason Murphy, NXC MFG
Jason Murphy´s NXC MFG (Next Chapter Manufacturing) is not a generalist service; instead, the company specializes in making tooling. Using LPBF and binder jet, the company produces some of the...
3DPOD 260: John Hart on VulcanForms, MIT, Desktop Metal and More
John Hart is a Professor at MIT; he´s also the director of the Laboratory for Manufacturing and Productivity as well as the director of the Center for Advanced Production Technologies....