Researchers from Universiti Tun Hussein Onn Malaysia continue the ongoing trend in exploring ways to improve the use of concrete in construction applications, releasing their findings in the recently published ‘Emerging Natural Fiber-Reinforced Cement Materials and Technology for 3D Concrete Printing.’
3D printers are being used in construction around the world today, from creating homes at rapid speed to endeavoring to create entire villages, experiment with self-healing properties in materials for better performance, and much more. In this latest research, the authors review the current trends and use of cement and composites.
Pointing out that construction in Malaysia has reached a slow-down due to affordability, lack of materials, and transportation cost, it becomes clear why the researchers are motivated to explore the benefits of 3D printing and additive manufacturing processes further. This makes building homes ‘prohibitive,’ and certainly does not allow for young people to buy first homes as they may do in other countries as a typical milestone.
To surpass these issues in Malaysia—as well as other countries—researchers have continued to delve into additive manufacturing and the refining of cement materials for improved extrusion and required properties. Referring to companies such as WinSun, the authors point out that they have had worldwide success in 3D printing—as well as Apis Cor. Currently the most common large-scale AM processes with cement include cranes, gantry systems, and large robotic arms.
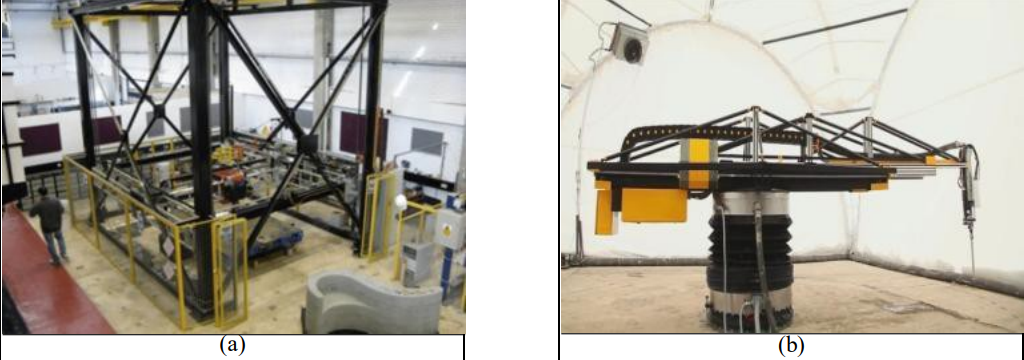
Type of machine used in structure printing for concrete material – (a) Gantry type build in Loughborough University for research activities [18]; (b) Crane type build by company name apis-cor [56]
“Since the cost of a robot arm is expensive, the usage of gantry type or crane type of machine is considered efficient technology for the development of concrete printing technology,” explain the authors.
For further development in construction 3D printing, the following requirements must be met in the hardware:
- Mechanism for concrete tank and pumping
- Nozzle for printing
- Movement control
Previous researchers such as Lim. S have added that for 3D printing with cement, the process of preparation is similar to any other in 3D printing, although there are required steps in post-processing to achieve suitable levels of optimization.
“The capability in reducing construction time depends on the complexity of the design structure where the greater structure complexity will provide more scope to minimize printing time. The printing element is modelled as a 3D CAD model and then converted into the STL file format. The printing path and the GCode file generated for printing each layer [18]. The printing process of concrete structure was explained by Mehmet and Izabela in their paper in the form of a work-flow diagram as in Figure 3 and can be seen that the printing process is the same [18 & 19],” stated the authors.

Illustration of the honeycomb (a) using 3D modelling design software then the mesh; (b) is appear once finish converting from drawing (dwg.) file to STL file [18]

Type of cement used in the industries based on their properties following cement standard ASTM C150 [24]

Extrudability is the very crux of 3D printing, allowing materials to flow, resulting in the desired designs and structures. Proper nozzle design is of utmost importance for performance, whether using circular, ellipse, square, or rectangular.
Natural fibers are used to bolster cement materials, forming composites meant to enhance properties and performance. Such enhancements are used in many industries, from automotive to packaging also, but in construction, they allow for reinforcement, better sustainability, and savings on the bottom line. Moisture content can be a problem too, as discussed in reviews by Geetanjali Das [6], A. Al-Maharma [7], and T. Alomayri [8], pointing out that there may be negative results such as cracking and poor thermal stability.“As freedom of printing activities, commonly the circular nozzle will have more freedom in doing printing activities without bothering in adjusting the printing angle for shape continuity at vertices or changes in the edge of the printed element,” stated the authors. “However, a study made by Kwon [28] says the surface finish created with a square orifice is better compared to an ellipse orifice and his statement supported by Anell [29].”
Studies performed by Mansur and Aziz [34] demonstrated that jute fibers can be effective, just as Savastano showed that ‘the workability of strengthened cement composites was reduced by the combination of eucalyptus pulp, coir or eucalyptus with sisal fibers.’
“The main factor influencing the loss of workability in natural fiber-reinforced cement mixtures is the fiber aspect ratio and volume fraction in mixtures. Fiber pre-treatment can act as remedy to reduced water-absorbing chemical fiber elements. Alternatively, workable natural fiber with improved cement mixtures could be produced by evaluating the water absorption characteristics of fibers in the mixture design,” concluded the authors.
“Using 3D printing provides access to complicated geometries and thus offers the option of printing hierarchical structures with the ability to provide sturdy and material-efficient structures for future buildings. The use of natural fiber perhaps can enhance more strength of mechanical properties for the concrete structure due to the pressure given during printing activities. So, the green concrete type will be produced by using natural fiber as reinforcement, which is cheaper and can be recycled.”
What do you think of this news? Let us know your thoughts; join the discussion of this and other 3D printing topics at 3DPrintBoard.com.
[Source / Images: ‘Emerging Natural Fiber-Reinforced Cement Materials and Technology for 3D Concrete Printing’]Subscribe to Our Email Newsletter
Stay up-to-date on all the latest news from the 3D printing industry and receive information and offers from third party vendors.
Print Services
Upload your 3D Models and get them printed quickly and efficiently.
You May Also Like
Metal Powder Supplier Elementum 3D Added to $46B Air Force Contract
Elementum 3D, a Colorado-based developer and supplier of metal powders used in additive manufacturing (AM), announced that the company has been added to the vendors list in the fourth on-ramp...
Ursa Major Lands $28.6M AFRL Deal for 3D Printed Draper Engine Flight Demo
The US Air Force Research Laboratory’s (AFRL’s) Rocket Propulsion Division at Edwards Air Force Base has awarded a $28.6 million contract to Ursa Major for follow-on work related to the...
3D Printing Financials: Rocket Lab’s Record-Breaking Year and Over 20 Launches Coming in 2025
Rocket Lab (Nasdaq: RKLB) closed 2024 with its best year yet. The company launched more rockets, signed more contracts, and expanded deeper into spacecraft and satellite production than ever before....
US Air Force Taps Beehive to Study 3D Printed Jet Engines
Propulsion 3D printing firm Beehive Industries secured a contract from the U.S. Air Force Life Cycle Management Center through SOSSEC. SOSSEC is a company that manages Other Transactions Authority (OTA)...