Saptarshee Mitra has recently published a doctoral thesis, ‘Experimental and numerical characterization of functional properties of sand molds produced by additive manufacturing (3D printing by jet binding) in a fast foundry.’ Delving into hybrid casting and improved methods for creating metal molds, Mitra analyzes varied printing parameters and their effects on mechanical properties.
Centered around improving production in foundries, the author investigates ways to create molds in a completely automated manner, taking advantage of some of the most classic benefits in 3D printing—from greater affordability and faster production time, to better quality in prototypes and parts.
“Besides, the absence of tooling costs makes this process particularly economical, and much complex geometry that cannot be manufactured using traditional sand casting can be reconsidered,” states Mitra. “3D printers are generally faster, easier to use and cheaper than other add-on technologies. It is also possible to make foundry sand molds of extremely small dimensions and very thin parts. Modern foundry industries gradually use this Hybrid Casting technology because they provide ease of sand molding with good surface finish.”
The goal of Mitra’s thesis is to create molds for metal casting with greater stiffness and permeability—ultimately, for use in both the aerospace and automotive industries—applications we have seen significantly impacted by AM processes from car parts to rocket engines, to the qualification of important end-use parts.

(a) Ancient Greece; bronze statue casting circa 450BC, (b) Iron works in early Europe: cast-iron cannons from England circa 1543 [4]
“Sand casting is the most widely used metal casting process in manufacturing, and almost all casting metals can casted in sand molds,” explained Mitra. “Sand castings can range in size from very small to extremely large. Some notable examples of items manufactured in modern industry by sand casting processes are engine blocks, machine tool bases, cylinder heads, pump housings, and valves.”
Metal casting requires:
- Proper design
- Suitable choice in material
- Production of patterns for molds and cores
- Selection of the casting process
- Post-processing
- Quality control
“Three-dimensional printing (3DP) of sand molds using binder jetting technology overcomes challenges faced in the traditional production method, e.g., limitations in terms of part complexity and size, production time and cost (which depends on the quantity and the part complexity, optimization in part design/design freedom for any castable alloys,” states Mitra.
A series of chemically bonded 3D printed samples were examined. While binder amounts were evaluated by Loss on ignition (LOI) experiments, mechanical strength was measured via standard 3-point bending tests. Permeability was measured by the air flow rate through the ‘samples at a given pressure.’
Mitra learned that molds could be stored extensively at room temperature, but permeability of samples did decrease as temperature was raised.
The author also noted that strength of the molds was ‘profoundly influenced’ by binder content, with increased amounts consequently increased mechanical strength.
“X-ray µ-CT images were used to compute the porosity, pore size, throat size and the permeability of the 3D printed specimens for different binder contents and grain sizes, using analytical and numerical methods,” concluded Mitra. “The permeability predicted in the steady-state was compared with experimental and analytical measurements for layered silica grain arrangement. A major advantage of using X-ray CT characterization is the nondestructive nature of the tests. The computed permeability can be used as input to numerical simulations of metal casting allowing the prediction of macroscopic defects.
“The present findings represent a step forward towards improved prediction of mass transport properties of the 3DP sand molds. However, further characterization of permeability of such additively processed sand mold should be performed with varying average grain diameter, to check the convergence of the present model. Also, samples printed with other printing process parameters should be studied.”
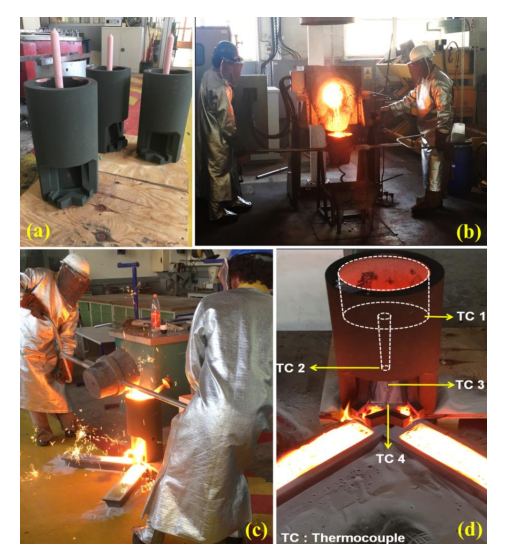
Steps involved, (a) 3D printing of sand mold, (b) melting iron, (c) casting process
and (d) eroded molded with the respective positioning of thermocouples.
What do you think of this news? Let us know your thoughts; join the discussion of this and other 3D printing topics at 3DPrintBoard.com.
[Source / Images: ‘Experimental and numerical characterization of functional properties of sand molds produced by additive manufacturing (3D printing by jet binding) in a fast foundry’]Subscribe to Our Email Newsletter
Stay up-to-date on all the latest news from the 3D printing industry and receive information and offers from third party vendors.
Print Services
Upload your 3D Models and get them printed quickly and efficiently.
You May Also Like
Making 3D Printing Personal: How Faraz Faruqi Is Rethinking Digital Design at MIT CSAIL
What if your 3D printer could think more like an intelligent assistant, able to reason through a design idea, ask questions, and deliver something that works exactly the way the...
Reinventing Reindustrialization: Why NAVWAR Project Manager Spencer Koroly Invented a Made-in-America 3D Printer
It has become virtually impossible to regularly follow additive manufacturing (AM) industry news and not stumble across the term “defense industrial base” (DIB), a concept encompassing all the many diverse...
Heating Up: 3D Systems’ Scott Green Discusses 3D Printing’s Potential in the Data Center Industry
The relentless rise of NVIDIA, the steadily increasing pledges of major private and public investments in national infrastructure projects around the world, and the general cultural obsession with AI have...
Formlabs Teams Up with DMG MORI in Japan
In late June, Nick Graham, Chief Revenue Officer at Formlabs, announced on LinkedIn that the company had partnered with DMG MORI, one of the world’s leading machine tool companies, to...