If industrialized society is determined to maintain its industrial activities, its engineers will need to completely rethink how parts are designed in order to improve energy efficiency. This is true regardless of whether or not this energy comes from fossil fuels (which must be phased out starting yesterday) or renewable sources.
For this reason, additive manufacturing (AM) may be the best technology suited for the production of these novel designs, given its ability to fabricate complex geometries impossible with other fabrication techniques. While flying will likely need to be reduced as much as possible in general, due to their contribution to energy usage, the use of AM in the aviation sector has demonstrated the outcomes possible with all energy intensive industries.
Weight and Performance Optimization
GE has performed a great deal of work to reduce fuel consumption in aircraft using AM by optimizing the strength-to-weight ratio of aircraft parts. The paradigm-shifting part in this instance is the LEAP fuel nozzle, which consolidated what was previously an assembly of 18 parts into just one. This resulted in an estimated fuel savings of 15 percent in jet engines, translating to an estimated 15 percent reduction in CO2 emissions and 50 percent reduction in NOx emissions.
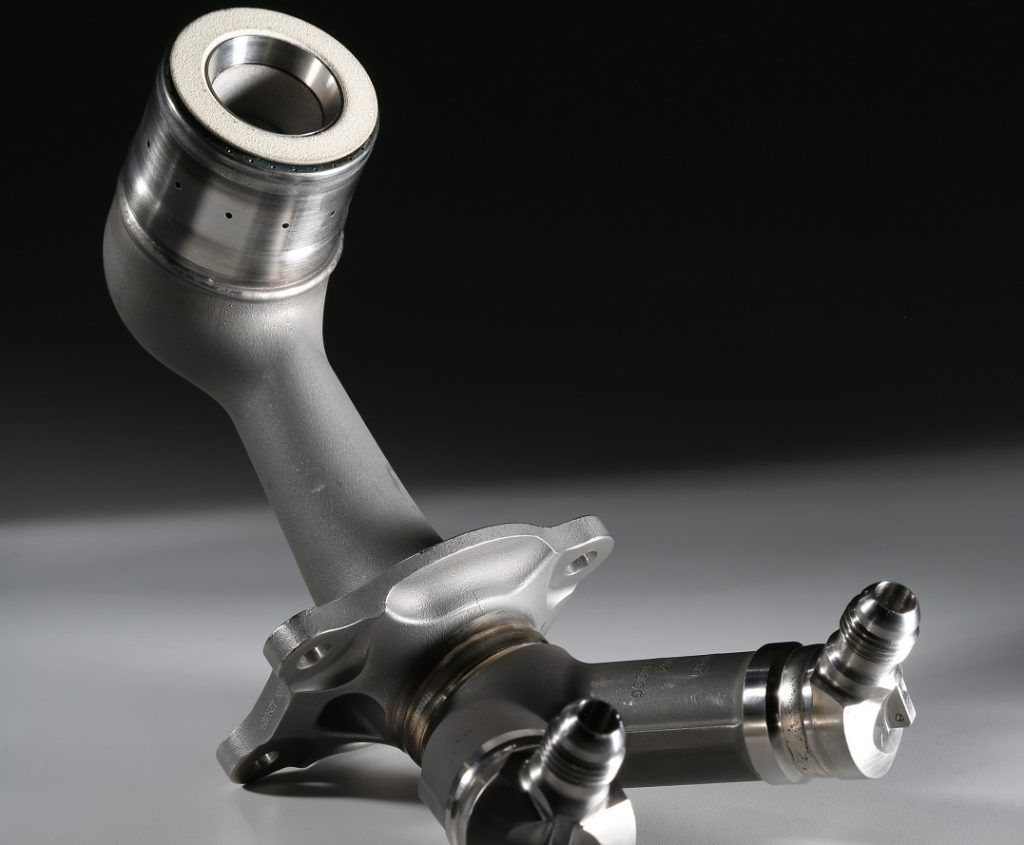
The LEAP fuel nozzle designed and manufactured by GE and Safran via CFM International. Image courtesy of GE Aerospace.
In 2014, Airbus and EOS performed an environmental lifecycle analysis study that compared metal casting with AM, determining that AM used 25 percent less material. By cutting the weight of an aircraft bracket by 10 kilograms, the 3D-printed was estimated to reduce CO2 emissions of the plane by 40 percent.
GE went on to develop the Catalyst turboprop engine for the Cessna Denali made up of 35 percent 3D-printed parts, which include the accelerator, a combustor swirler, a gearbox, and a large gearbox case. All of this, along with other innovations, reduce fuel burn by 20 percent and fuel consumption by 1 percent. This only translates to one percent reduction in CO2 emissions. Unfortunately, test flights for the aircraft have yet to be performed because the test engine has not yet been delivered to the aircraft manufacturer.
If successfully produced, the Catalyst engine will become a core part of a hybrid fuel system for XTI Aircraft TriFan 600 plane. Naturally, we should be skeptical of the real-world impact of these endeavors, in particular for private planes such as the TriFan 600 and the Cessna Denali, which are reserved for business use.
However, if somehow large same weight reductions could be applied across the entire structure of more commercial passenger and freight aircraft, it would be possible to see the aviation sector have a far less significant impact on our collapsing ecosystem than it currently has. Perhaps more importantly, we could see electric planes actually become viable.
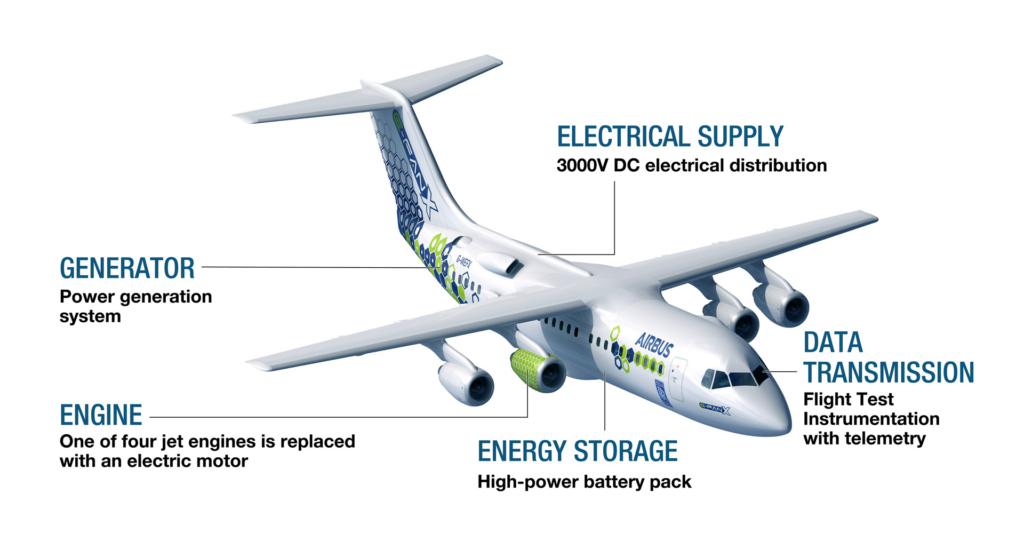
A rendering of a hybrid-electric aircraft designed by Airbus, with expected first flight in 2021. Airbus has a goal of achieving zero-emissions flights by 2040. Image courtesy of Airbus.
Boom Supersonic, which is investing in 3D printing for its supersonic planes, estimates that there are over 170 programs in place to create electric aircraft. Stepping stones along the way include hybrid electric planes, such as the E-Fan X from Airbus, and retrofitting existing aircraft with hybrid engines.
The U.N.’s Intergovernmental Panel on Climate Change (IPCC) reports that we have until 2030 to halve global greenhouse gas emissions, but research suggests that even that projection is underestimating the scope of the problem. Therefore, building new planes may not be enough to solve the problem or may even worsen it, due to the emissions associated with manufacturing and flying even hybrid aircraft.
Extrapolating Aerospace Lessons to Other Sectors
So, as electric aircraft are constructed and limited to only necessary flights or alternative modes of transportation are deployed, other industries may be able to learn lessons from the aviation sector and apply them to their own work. An increasing number of design and simulation tools are now available to more easily optimize part design for 3D printing, potentially reducing the weight of objects regardless of application.
If the U.S. does finally deploy high-speed rail (HSR) under a Green New Deal-type infrastructure plan, for instance, there may be opportunities to lighten the load of trains through weight-optimization design techniques. Unfortunately, at the moment, the most advanced application for AM in the rail industry is for the fabrication of spare parts, though this includes parts for HSR.
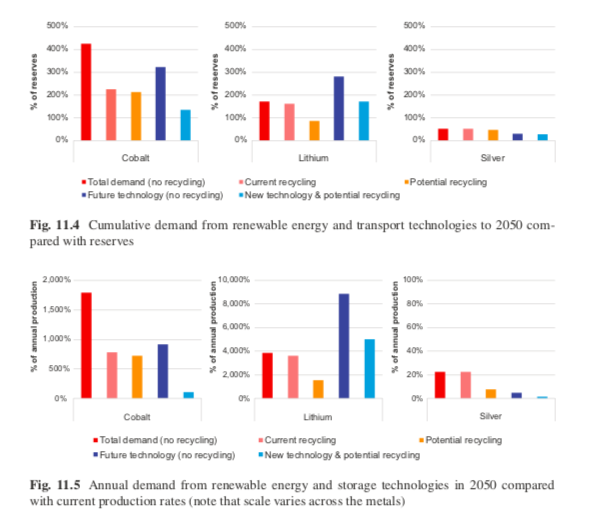
In these graphics, demand for metal doesn’t stem from electric vehicle projections alone, but from renewable energy and electric vehicle projections. Images courtesy of Achieving the Paris Climate Agreement Goals.
As for electric vehicles, the authors of Achieving the Paris Climate Agreement Goals project that, “The cumulative demand for cobalt from renewable energy and transport exceeds the current reserves in all scenarios, and for lithium, the cumulative demand is exceeded in all scenarios, except the ‘potential recycling scenario’.”
In other words, we might not have enough cobalt or lithium to meet the demand currently expected, meaning that, unless we can develop alternative battery solutions within 10 years, the promise of electric vehicles is tenuous. For those vehicles that are necessary to maintain some semblance of industrialized society, lightweighting will help extend their range.
Transportation accounts for about 19.5 percent of global greenhouse gas emissions, according to the IPCC. Energy production accounts for about 30 percent, general industrial processes and construction account for 19 percent.
Because a large part of construction emissions come from the fabrication of concrete, it’s possible that additive construction could reduce the sector’s CO2 footprint by using less material and unique recycled materials. Other sources of GHG emissions from this sector include combustion of fossil fuels for heat and power as well as the use of fossil fuels for non-energy use and metallurgical production. As we covered in our series on the use of AM in the general industry and tooling sector, minor efficiencies could potentially be gained in industrial manufacturing processes.
By far the biggest impact we could have to cut emissions is to replace fossil fuel energy generation with renewables. AM can be used to improve the production of wind turbines, whether that is for prototyping, molds, or production. It has been used, for instance, to create small-scale systems for low amounts of power generation.
In some cases, AM has been used to improve the efficiency of solar systems, as well. Sandia National Laboratories was able to 3D print fractal-like, concentrating solar power receivers for small to medium-scale use that were up to 20 percent more effective at absorbing sunlight than traditional designs. Lawrence Livermore National Laboratories formerly studied the ability to 3D print microfluidic devices used for sun tracking in solar power technologies.
The above graphic related to metal supply and demand, the researchers indicate that we do not have enough lithium or cobalt to reach the goals set out by the Paris Climate Agreement. This is not only the case for building electric vehicles, but for renewable energy as a whole. These authors and the authors of the IPCC reports, however, maintain a steady increase in economic growth and, therefore, do not consider potentially more dramatic and realistic cuts to emissions that don’t rely wholly on technological developments.
In these areas, AM may only play a small role due to the fact that our existing, centralized manufacturing system relies on mass production technologies to ship items globally from disparate locations. As we are now seeing with supply chain disruption caused by the global coronavirus pandemic, however, centralized production may not be the long-term method for manufacturing. If we move to a distributed manufacturing model, AM may be the production technology of choice and, therefore, could play a larger role. There may be ecological benefits to such a model as well. We will explore distributed production in our next section in this series.
Subscribe to Our Email Newsletter
Stay up-to-date on all the latest news from the 3D printing industry and receive information and offers from third party vendors.
Print Services
Upload your 3D Models and get them printed quickly and efficiently.
You May Also Like
The Dental Additive Manufacturing Market Could Nearly Double by 2033, According to AM Research
According to an AM Research report from 2024, the medical device industry, specifically in dentistry, prosthetics, and audiology, is expected to see significant growth as these segments continue to benefit from...
Heating Up: 3D Systems’ Scott Green Discusses 3D Printing’s Potential in the Data Center Industry
The relentless rise of NVIDIA, the steadily increasing pledges of major private and public investments in national infrastructure projects around the world, and the general cultural obsession with AI have...
AM Research Webinar Explores Continuum’s Sustainable Metal Additive Manufacturing Powders
Metal additive manufacturing (AM) powder supplier Continuum Powders is working to develop solutions that empower industries to reduce waste and optimize their resources. An independent life cycle assessment (LCA) of...
3D Printed Footwear Startup Koobz Lands $7.2M in Seed Round
California-based Koobz is focused on reshoring the U.S. footwear supply chain with advanced manufacturing processes, including 3D printing. The startup just announced that it has added $6 million to its...