The U.S. Department of Energy’s Oak Ridge National Laboratory (ORNL) is the epicenter of a great deal of exciting research currently taking place in the 3D printing industry, much of it dedicated to further industrializing the technology. The latest partnership coming out of the U.S. lab is with nTopology, the New York-based software startup focused on topology optimization and generative design in additive manufacturing (AM).
nTopology and ORNL have signed a Cooperative Research and Development Agreement that will work toward improving AM capabilities via software “toolkits” and see ORNL’s expertise introduced into nTop software. These capabilities will then be made available commercially.
ORNL was responsible for the development of the Big Area Additive Manufacturing (BAAM) system now sold by Cincinnati Incorporated, which is able to deposit large volumes of polymer material very quickly. The partnership with nTopology will see nTop’s foundational software incorporated into such systems as the BAAM in order to create parts optimized for the printing process. In addition to improving design and modeling controls, the partners hope to develop reusable, configurable templates for use by ORNL’s Manufacturing Demonstration Facility.
The first phase of the project will see the partners develop an nTop toolkit for the BAAM system that will optimize geometries and print setup, connecting nTop to the ORNL slicer for 3D printing on BAAM machines. Phase two will involve the development of a toolkit for direct metal grain growth in electron beam melting (EBM), as well as a toolkit for designing a honeycomb infill based on circle packing and simulation for fused deposition modeling (FDM), and simulation-based optimization of support structures for BAAM, direct metal laser sintering (DMLS) and EBM.
Phase one sounds relatively straightforward (though definitely easier said than done), in that nTopology’s existing software tools will be applied to BAAM 3D printing, creating interoperability between nTop and ORNL’s slicer and learning how the physics of large, fast polymer deposition will impact the possibilities of topology optimization and generative design within nTop.
Phase two appears to be much more elaborate. Grain growth is a phenomenon associated with metallurgy, in which microscopic crystals within a material increase in size at higher temperatures. In particular, EBM and other 3D printing technologies suffer from a coarse, column-shaped grain structure along the vertical axis. The ability to control grain growth would mean being able to optimize the microscopic structure of a part, essentially taking what nTop software already does to the macroscopic geometry of an object (lightweighting it, improving its strength, etc.) and applying it to the microstructure.
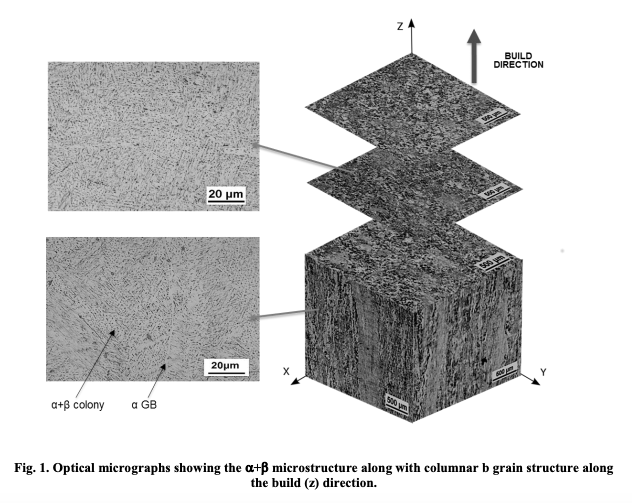
From an ORNL paper on grain growth and post-processing techniques in EBM.
The ability to design honeycomb infills using circle packing techniques for FDM would mean varying the sizes of the polygons used in infills in order to change the properties of a plastic part. Larger and smaller shapes could be mixed and packed more loosely or tightly to generate different macroscopic properties.

From an ORNL conference paper on the topic of circle packing and ORNL’s slicer.
Finally, the optimization of support structures for BAAM, DMLS and EBM would enable the creation of supports with unique shapes (and possibly microstructures as discussed) only where necessary, limiting the need for excess material and maybe even improving the support removal process, which accounts for a significant portion of post-processing labor and time.
The partners believe that the project could ultimately improve the build speed and material usage of large-scale 3D printing, which would in turn reduce costs associated with material usage and machine amortization. nTopology would then be able to introduce the new technology developed by the partnership to the market via the nTop platform and the portfolio of toolkits that it already licenses.
[Feature image courtesy of nTopology]Subscribe to Our Email Newsletter
Stay up-to-date on all the latest news from the 3D printing industry and receive information and offers from third party vendors.
Print Services
Upload your 3D Models and get them printed quickly and efficiently.
You May Also Like
U.S. Navy Lab Uses 3D Printing to Reduce Tooling Lead Time By Over 90%
The F-35 Lightning II Joint Program Office (JPO), responsible for life-cycle management of the key fifth-generation joint strike fighter (JSF) system used by the U.S., its allies, and its partners,...
Etsy Design Rule Change Reduces Selection of 3D Printed Goods
Online marketplace Etsy has implemented a rule change requiring all 3D printed goods on the site to be original designs. The update to the site’s Creativity Standards states, ¨Items produced using...
Honeywell Qualifies 6K Additive’s Nickel 718 for 3D Printed Aerospace & Defense Parts
6K Additive is renowned for manufacturing sustainable additive manufacturing (AM) powder, and offers a wide portfolio of premium metal and alloy powders that include titanium, copper, stainless steel, and nickel,...
MetalWorm Sells WAAM Systems to Research Institutes in Brazil and Malaysia
Turkish WAAM firm MetalWorm has sold a system in Malaysia and another in Brazil. This is an excellent example of a few emerging trends in additive. Firstly, WAAM was experimented...