Swiss researchers Marco Pelanconi and Alberto Ortona (both from Mechanical Engineering and Materials Technology Institute (MEMTI), University of Applied Sciences (SUPSI)) are testing 3D lightweight structures inspired by butterflies.
With their findings detailed in the recently published ‘Nature-Inspired, Ultra-Lightweight Structures with Gyroid Cores Produced by Additive Manufacturing and Reinforced by Unidirectional Carbon Fiber Ribs,’ Pelanconi and Ortona reach out to nature to understand more about the design and performance of one particular insect that continues to fascinate humans due to their enchanting, bright colors and their migratory habits. While many facets of nature inspire 3D printed architectures today—from fish to marine mollusks and more—here the butterfly was studied due to its optimized geometry and well-known design that allows them not only to beckon mates or evade predators but also to bend loads:
“In a cross section of a wing scale, the highly porous central region separates two outer regions that are realized by a frame in which load-bearing bars are connected to the porous core by perpendicular smaller bars,” stated the researchers. “The topology of the inner porous region maximizes the structure’s rigidity while minimizing its weight.
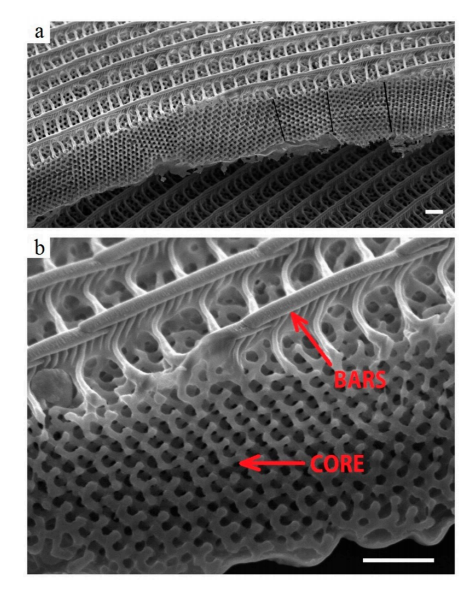
Scanning Electron Microscopy (SEM) micrograph on a cross sectional view of a butterfly wing scale [10]. (a) Highly porous central region supported by high-stiff bars. (b) The same structure at a higher magnification: Perpendicular smaller fibers make the connection between the porous core and the bars. Scale bar is 1.
“We performed our material selection based on the Ashby five inter-related criteria: (i) the function of the structural component that dictates (ii) the choice of materials and their properties, (iii) the shape and size of the components, and (iv) the process used to manufacture the components that interact with (v) the cost and availability (of both material and process).”
The new structure was also strengthened with carbon fiber-reinforced plastic (CFRP) rods, added to the 3D printed structures with glue. The structure involved a gyroid polymeric tube at the core of its simple architecture, and the researcher explained that beyond this work they would be working on development of stronger structures to carry more complex loads.
The sample gyroid was fabricated with the following measurements: length of 140 mm, a width of 30 mm, and a height of 15 mm. Connection tubes featured an external diameter of 3.25 mm, and with ‘variable internal diameters’ depending on the rod.
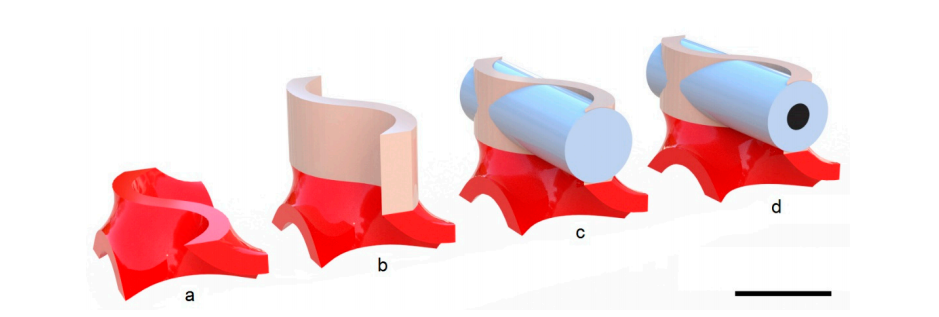
Schematic of the procedure to connect the gyroid with the unidirectional carbon fiber-reinforced plastic (CFRP) inserts. (a) Gyroid solid cell with surface thickness of 0.75 mm. (b) 3.25 mm extrusion of the cell upper surface. (c) Tube addition with diameter of 3.25 mm. (d) Addition of the CFRP inserts with a 1.20 mm diameter. Scale bar is 5 mm.
The 3D printed structures accompanied by the CFRP rods exhibited over two times the stiffness of samples that were not reinforced. The CFRP-enhanced structure was able to handle a maximum load of approximately 280 ± 10.05 N, although the authors notes that both types of structures failed at 10 mm displacement.

Three-point bending finite element simulations of the structure with different configurations. (a) Gyroid thickness variation. (b) CFRP diameter variation. (c) Stiffness–bending deformation against gyroid thicknesses. (d) Stress–gyroid thicknesses chart. (e) Stiffness-bending deformation against CFRP diameters. (f) Stress-CFRP diameters chart. Scale bar is 5 mm.
“Some parameters like gyroid thickness do influence the mechanical properties of the bare cores, because adding thickness means adding mass to the structure,” concluded the researchers. “This parameter, though, is much less influent when the fiber-reinforced structure is considered. This is because, in general, cores are much less loaded than the skins in a sandwich structure under bending. Indeed, the influence of the CFRP bar diameter is much significant.
“One advantage of this solution over the standard sandwich structures is that it directly connects the solid part of the porous core to the mating reinforcing element and thus further minimize its mass. The proposed topological approach can be applied to many materials as long as there is a difference in the elastic modulus between the core and the ribs. Our work aimed at demonstrating the feasibility of this concept, which is why we used the well-known stereo lithography as an AM technique and commercial CFRP rods as ribs.”
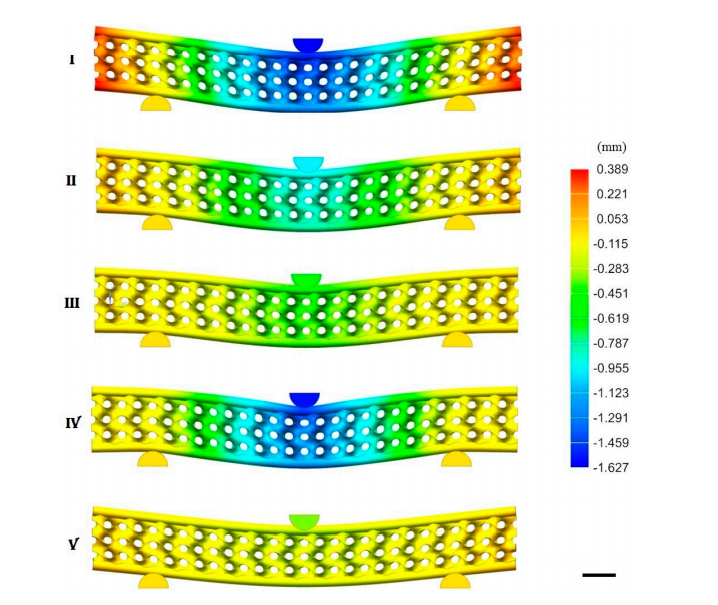
Finite element simulations of the structures: displacement results. (I) t = 0.375 mm; d = 1.2 mm. (II) t = 0.75 mm; d = 1.2 mm. (III) t = 1.5 mm; d = 1.2 mm. (IV) t = 0.75 mm; d = 0.6 mm. (V) t = 0.75 mm; d = 2.4 mm. t is the gyroid thickness and d is the CFRP diameter. Scale bar is 10 mm.
What do you think of this news? Let us know your thoughts! Join the discussion of this and other 3D printing topics at 3DPrintBoard.com.
[Source / Images: ‘Nature-Inspired, Ultra-Lightweight Structures with Gyroid Cores Produced by Additive Manufacturing and Reinforced by Unidirectional Carbon Fiber Ribs’]
Subscribe to Our Email Newsletter
Stay up-to-date on all the latest news from the 3D printing industry and receive information and offers from third party vendors.
Print Services
Upload your 3D Models and get them printed quickly and efficiently.
You May Also Like
Havaianas Collaborates with Zellerfeld to Launch 3D Printed Flip-Flops
The shoe of the summer is undoubtedly the flip-flop. Easy on, easy off, your feet won’t get sweaty because there’s not much material, and they’re available in a veritable rainbow...
UCLA Researchers Develop 3D Printed Pen that May Help Detect Parkinson’s Disease
Diagnosing Parkinson’s disease is difficult. Often, early symptoms of the progressive neurological condition may be overlooked, or mistaken for signs of aging. Early diagnosis can help save lives and improve...
Printing Money Episode 30: Q1 2025 Public 3D Printing Earnings Review with Troy Jensen, Cantor Fitzgerald
Printing Money is back with Episode 30, and it’s that quarterly time, so we are happy and thankful to welcome back Troy Jensen (Managing Director, Cantor Fitzgerald) to review the...
Heating Up: 3D Systems’ Scott Green Discusses 3D Printing’s Potential in the Data Center Industry
The relentless rise of NVIDIA, the steadily increasing pledges of major private and public investments in national infrastructure projects around the world, and the general cultural obsession with AI have...