If you close your eyes and meditate hard enough, plunging yourself into a deep transtemporal trance, you may be able to conjure up your ancient ancestors wielding a mighty hammer to smash and shape a hot piece of iron against an anvil. The world’s oldest recorded metalworking process, forging, still exists today, albeit in a form somewhat removed from its inception over 6,000 years ago.
Forging processes apply force to shape metal. Most often, modern forging is associated with high temperatures heating metal workpieces to the point that they can be formed by machine-driven hammers or presses, sometimes using a die to smash the material into a specific geometry. However, there are other forging techniques that use warm or cold temperatures that ensure that metal parts don’t expand as a result of high heat and then shrink, thus resulting in better tolerances.
In the additive manufacturing (AM) industry, we love to talk about the various traditional manufacturing processes that are already being disrupted by 3D printing and forging is no different. Exactly how AM will disrupt the world of forging, however, is different from how it is impacting, say, casting and machining.
Forging has its major advantage in the physical strength of forged parts, which, due to the fact the internal grain structure deforms to follow the general shape of the part, are stronger than cast or machined parts. The cost of materials for forging processes is usually cheaper, but forging presses and dies can be costly, and parts usually require secondary processes, such as CNC machining, to achieve final tolerances.
Therefore, forging is usually reserved for less geometrically complex parts that need to be manufactured in a highly repeatable way from less expensive metals, such as iron and steel. This might mean wheel spindles, kingpins, axle beams and shafts for automotive parts; valves and fittings in oil and gas; pliers, hammers, sledges and wrenches in hardware and tools; connecting rods, cylinders, discs in general industry; shells, triggers, and other artillery parts; and bulkheads, spars, hinges, engine mounts, brackets, and beams in aerospace. Obviously, some of these parts can crossover from one vertical to another (e.g., brackets and hinges)
Those familiar with AM technologies may start to get a feel for where AM is best situated for impacting the forging market: low-geometric complexity, yet high strength material properties. If you’re thinking like we are, you are starting to consider the possibility of directed energy deposition (DED) for the fabrication of near-net-shape parts.
DED offers many of the same benefits and fits many of the same applications as forging, while providing some additional advantages. Using blown powder or a metal wire, DED can rapidly form a medium-to-large sized part to near-net-shape. Often referred to as “blanks”, these components are then finished using CNC machining.
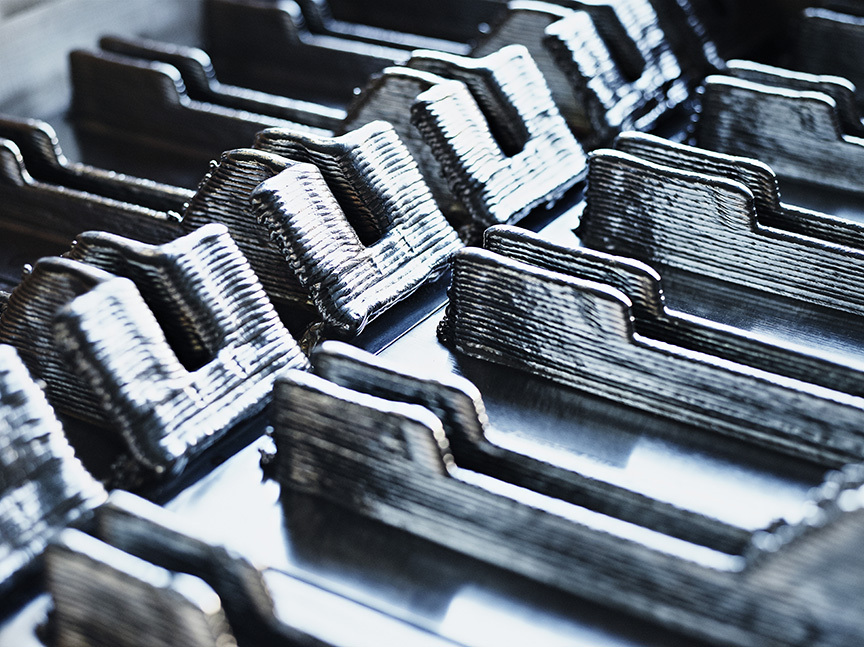
Blanks 3D printed using Norsk Titanium’s Rapid Plasma Deposition process. Image courtesy of Norsk Titanium.
DED can create a metal part closer to the final desired shape than forging, without the need for tooling. And, when it comes to more expensive materials like titanium, DED can potentially be more cost effective. For forged parts that would typically require dies, DED can be significantly faster. In turn, DED has the potential to reduce die, material and machining costs for certain components.
Specifically, those components will be low in number, when mass manufacturing doesn’t make sense and AM will actually be cheaper than forging. This means short runs of specialty components and prototypes. In other words, aerospace is the primary sector for DED as an alternative to forging at the moment. There are numerous DED companies targeting the aerospace industry, with aircraft manufacturers qualifying the processes and parts for installation on aircraft.
When it comes to part strength, DED components experience large thermal gradients during the deposition process that result in residual stresses that can lead to distortion and negatively affect the overall strength of the part. In some cases, heat treatment may even need to be implemented during the actual production of a part in order to relieve stress.
Naturally, systems manufacturers are working to overcome these issues, including closed-loop quality control and monitoring, as well as simulation software capable of compensating for stresses that will be experienced in a printed part.
Due to the issues discussed here, forging is not likely to be threatened by AM, but complemented by it. Forging is still the go-to choice for mass manufacturing sturdy, geometrically simple components, while DED can be used for small numbers of (often medium-to-large) specialty parts that would otherwise require tooling or must be made from high-performance, expensive metals. This might include structural components for the Boeing 787 Dreamliner or titanium brackets for the A350 XWB.
Once a DED system is brought in for such projects, auxiliary applications can then be found for the technology. For instance, DED machines can be used to repair dies for forging or to deposit additional features onto forged parts. Arconic actually developed a novel additive process called Ampliforge in which DED parts are first manufactured and then finished with forging to ensure the proper material properties of the components.
[Feature image courtesy of AMETEK.]Subscribe to Our Email Newsletter
Stay up-to-date on all the latest news from the 3D printing industry and receive information and offers from third party vendors.
Print Services
Upload your 3D Models and get them printed quickly and efficiently.
You May Also Like
The Market and Industry Potential of Multi-Material 3D and 4D Printing in Additive Electronics
Additive manufacturing leverages computer-based software to create components for products by depositing either dielectric or conductive materials, layer by layer, into different geometric shapes. Since its birth in the 1980s,...
3DPOD 262: Bio-inspired Design for AM with Dhruv Bhate, Arizona State University
Dhruv Bhate is an associate professor at Arizona State University. There, he looks at structures, materials, and design. Previously, he worked at PADT as well as in the semiconductor and...
3DPOD 261: Tooling and Cooling for AM with Jason Murphy, NXC MFG
Jason Murphy´s NXC MFG (Next Chapter Manufacturing) is not a generalist service; instead, the company specializes in making tooling. Using LPBF and binder jet, the company produces some of the...
3DPOD 260: John Hart on VulcanForms, MIT, Desktop Metal and More
John Hart is a Professor at MIT; he´s also the director of the Laboratory for Manufacturing and Productivity as well as the director of the Center for Advanced Production Technologies....