This week, multidisciplinary partners GE Research, Oak Ridge National Laboratory (ORNL), and PARC, a Xerox company, were awarded a $1.3 million project to more than double the speed of the design and validation process for high-performance 3D printed turbomachinery components. If the speed can be increased by up to 65%, it could revolutionize turbomachinery product design, as 3D printing would be faster than many conventional manufacturing processes.
“It not only could help expand the broader application of additive; it also could lead to improved design of turbomachinery parts that deliver cleaner, more efficient energy solutions,” Todd Alhart, Media Relations Executive with GE Research, told 3DPrint.com.
The award was granted through DIFFERENTIATE (Design Intelligence Fostering Formidable Energy Reduction (and) Enabling Novel Totally Impactful Advanced Technology Enhancements), a program by the Advanced Research Projects Agency (ARPA-E), which GE Research has worked with before.
It takes many people, who are experts in fluid, structural, and thermal properties, to design new components for complex power products, like gas and wind turbines and jet engines. And while 3D printing itself can save time on production, a lot of time and effort are put into initially validating a part for 3D printing in these types of industries. You have to consider its aerodynamic performance, how the material responds to stresses and heat, how the design can impact the airflow, etc.
All of this work can take between two and five years to complete. But, this collaborative research team thinks they can cut this time by over half, down to 1-2 years – making it faster than traditional casting processes.
“One of the keys to enabling the widespread use and benefits of 3D printing is the reduction of the time it takes to create and validate defect-free 3D component designs,” explained Brent Brunell, leader of GE Research’s Additive efforts. “Using multi-physics enabled tools and AI, we think we can beat the timeline for some traditional manufacturing processes by automating the entire process.”

L-R: GE Research Principal Scientist for Machine Learning, Naresh Iyer; Lead Engineer for Structural Mechanics/Dynamics, Sathyanarayanan Raghavan; Principal Engineer for Additive Research, Dean Robinson; and Carlos Velez, Lead Engineer in Thermosciences group, converse on the 3D design tools in GE Research’s Information Works Lab. They are part of a multidisciplinary research team working to reduce the timeline for designing and validating 3D printed turbomachinery components from 2-5 years to 1-2 years.
He went on to say that “the optimization of structural characteristics has already been automated,” which has not yet been completed for the fluid and thermal properties of a part. GE and PARC researchers are now working to achieve this, using AI tools to generate surrogate models automatically from additive producibility data and “seamlessly integrate it with multi-physics design optimization techniques.”
The team will work together to create AI and machine learning (ML) technologies that will allow for millions of different design iterations in a much faster timeframe.
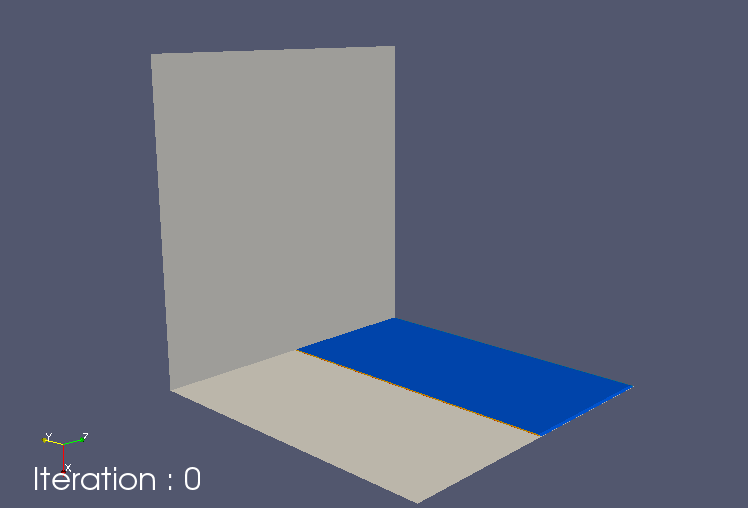
A sampling of the types of design tools GE, ORNL and PARC researchers will utilize to accelerate 3D part design of turbomachinery parts. This video illustrates the design evolution of a thermal optimum heat exchanger, using an enhanced multi-physics topology optimization tool.
“The combination of model-based and data-driven AI to accelerate generative design is a key innovation that will dramatically reduce the time to synthesize and fabricate quality parts,” stated Saigopal Nelaturi, the Manager of Computation for Automation in Systems Engineering for the System Sciences Lab at PARC.
“Surrogate models (built using machine learning) that encapsulate complex couplings between process physics and part quality will help guide the optimization models in feasible regions of very high dimensional design spaces. This combination of AI techniques enables automatic multi-functional part synthesis to meet real-world application demands, for which AM can provide truly novel solutions.”
The researchers will be using the Summit supercomputer at ORNL’s Computing Facility to fabricate precise, AI-based surrogate models. ORNL’s High Flux Isotope Reactor will also be put to work during this project, as a way to analyze 3D printed turbomachinery components and generate the necessary data to train, and later evaluate, these models.
John Turner, the Computational Engineering Program Director at ORNL, said, “This is the type of project that leverages the unique capabilities at ORNL – experimental and computational facilities – as well as expertise in computational science and additive manufacturing.”
The end result will be a high-performance, defect-free 3D printed multifunctional design that can stand up well under high temperatures and stresses, and perform better than parts made with conventional casting methods.
Discuss this story and other 3D printing topics at 3DPrintBoard.com or share your thoughts below.
Subscribe to Our Email Newsletter
Stay up-to-date on all the latest news from the 3D printing industry and receive information and offers from third party vendors.
Print Services
Upload your 3D Models and get them printed quickly and efficiently.
You May Also Like
Reinventing Reindustrialization: Why NAVWAR Project Manager Spencer Koroly Invented a Made-in-America 3D Printer
It has become virtually impossible to regularly follow additive manufacturing (AM) industry news and not stumble across the term “defense industrial base” (DIB), a concept encompassing all the many diverse...
Inside The Barnes Global Advisors’ Vision for a Stronger AM Ecosystem
As additive manufacturing (AM) continues to revolutionize the industrial landscape, Pittsburgh-based consultancy The Barnes Global Advisors (TBGA) is helping shape what that future looks like. As the largest independent AM...
Ruggedized: How USMC Innovation Officer Matt Pine Navigates 3D Printing in the Military
Disclaimer: Matt Pine’s views are not the views of the Department of Defense nor the U.S. Marine Corps Throughout this decade thus far, the military’s adoption of additive manufacturing (AM)...
U.S. Congress Calls Out 3D Printing in Proposal for Commercial Reserve Manufacturing Network
Last week, the U.S. House of Representatives’ Appropriations Committee moved the FY 2026 defense bill forward to the House floor. Included in the legislation is a $131 million proposal for...