In the recently published ‘3D printed mesh reinforcements enhance the mechanical properties of electrospun scaffolds,’ US researchers explore the use of tissue engineering structures for both regeneration and repair, using innovative materials to strengthen mechanical properties.
As research continues regarding scaffolding in clinical applications such as repair of the bladder or ligaments or grafting for bone or skin, scaffolds are being 3D printed and employed more often to mimic the extracellular matrix, scale up structures, and provide good cell adhesion and movement.
“To improve biocompatibility, methods have been developed to incorporate endogenous ECM molecules and/or growth factors to promote cell differentiation, survival, and/or proliferation,” state the researchers. “However, one of the major disadvantages of electrospun scaffolds is that they have relatively poor mechanical properties (low strength and stiffness, high ductility) compared to many of the tissues they are designed to heal. This limits their use in applications that require a material with relatively high mechanical strength and stiffness, such as bone or tendon repair.”
Scaffolds are often also used as composites, blended with synthetic polymers such as poly(ε-caprolactone) (PCL). This is a biodegradable, FDA-approved, well-established material. Other popular composites are:
- poly (3-hydroxybutyrate-co-3-hydroxyvalerate) (PHBV)
- poly (vinylidene fluoride) (PVD)
- poly (lactic acid) (PLA)
“For many regenerative therapies, it is thought that the mechanical properties of an implanted scaffold should match that of the target tissue. Accordingly, new approaches are needed to enhance the mechanical properties of electrospun scaffolds to make them more suitable for applications in musculoskeletal repair and regeneration,” state the researchers.
PLA was used for printing directly onto electrospun scaffolds. The researchers noted that tensile strength and elastic modulus were increased, with ductility decreased, in using PLA meshes. They upheld their matrix structure after being strengthened with PLA, with no issues regarding rejection of implants when tested on rats. Two types of PLA were used—one with 6mm between the struts, and another with an 8mm distance between struts.
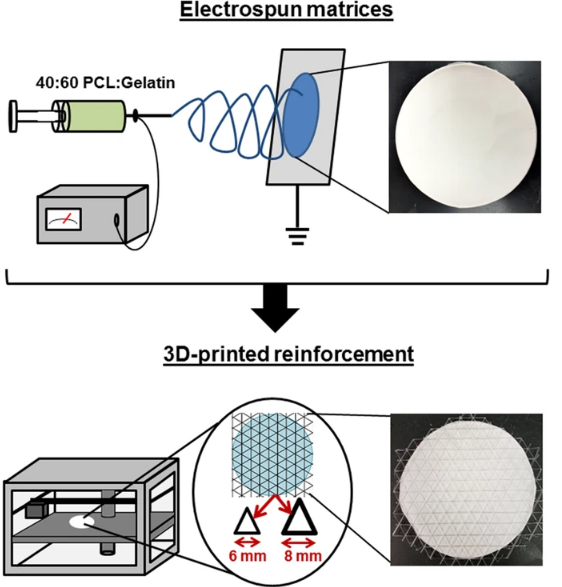
Fabrication of reinforced electrospun scaffolds. Electrospun scaffolds were produced from a 40:60 ratio of PCL:gelatin. The scaffolds were then placed in a 3D-printer and a PLA mesh was deposited onto one side of the scaffold. Two types of 3D-printed meshes were generated, one with a 6 mm distance between PLA struts, and the other with an 8 mm distance between struts
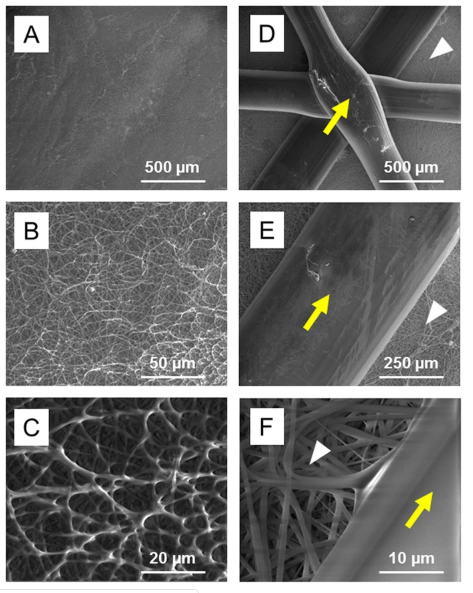
SEM imaging of reinforced electrospun scaffolds. a-c SEM images of the electrospun side of the reinforced scaffolds. Images show a uniform distribution of randomly oriented fibers. d-f SEM images of the 3D-printed side of the scaffolds. High magnification images (f) show that there is minimal damage to the electrospun fibers in the immediate vicinity of the 3D-printed PLA mesh. Yellow arrows depict the 3D-printed PLA. White arrowheads depict the PCL:gelatin scaffold
“When visualized under high magnification, it is apparent that deposition of the 3D printed layer did not compromise the woven structure of the electrospun scaffold. The electrospun fibers proximal to the PLA mesh were not melted from the heat of the 3D printing process,” stated the researchers.
Scaffolds were assessed by the research group as they used an in vivo bone graft model, which ultimately ‘suggested’ biocompatibility of the electrospun scaffolds. The scaffolds did not show a boundary separation between the electrospun and 3D printed layers; however, the mesh reinforcement was attached to the scaffold without interrupting the ‘architecture of the layer.’
“The addition of the 3D printed mesh is technically straightforward and can be applied to any type of electrospun scaffold, highlighting the adaptability of this approach to scaffolds of varying biochemical composition or structure,” concluded the researchers. “Furthermore, the differences in the mechanical properties imparted by the 6 mm vs. 8 mm reinforcements point to a potential strategy for tuning the strength and stiffness of electrospun scaffolds using meshes with different sizes and shapes.
“In sum, the current investigation suggests that the mechanical properties of electrospun scaffolds can be markedly improved by the addition of tunable 3D printed meshes, while preserving the desirable aspects of the electrospun material.”
Scaffolding in 3D printing is an area of fabrication that just continues to grow, especially in the areas of tissue regeneration, bone replacement, cartilage regrowth, and more.
What do you think of this news? Let us know your thoughts! Join the discussion of this and other 3D printing topics at 3DPrintBoard.com.
[Source / Images: ‘3D printed mesh reinforcements enhance the mechanical properties of electrospun scaffolds’]Subscribe to Our Email Newsletter
Stay up-to-date on all the latest news from the 3D printing industry and receive information and offers from third party vendors.
Print Services
Upload your 3D Models and get them printed quickly and efficiently.
You May Also Like
U.S. Navy Lab Uses 3D Printing to Reduce Tooling Lead Time By Over 90%
The F-35 Lightning II Joint Program Office (JPO), responsible for life-cycle management of the key fifth-generation joint strike fighter (JSF) system used by the U.S., its allies, and its partners,...
Etsy Design Rule Change Reduces Selection of 3D Printed Goods
Online marketplace Etsy has implemented a rule change requiring all 3D printed goods on the site to be original designs. The update to the site’s Creativity Standards states, ¨Items produced using...
Honeywell Qualifies 6K Additive’s Nickel 718 for 3D Printed Aerospace & Defense Parts
6K Additive is renowned for manufacturing sustainable additive manufacturing (AM) powder, and offers a wide portfolio of premium metal and alloy powders that include titanium, copper, stainless steel, and nickel,...
MetalWorm Sells WAAM Systems to Research Institutes in Brazil and Malaysia
Turkish WAAM firm MetalWorm has sold a system in Malaysia and another in Brazil. This is an excellent example of a few emerging trends in additive. Firstly, WAAM was experimented...