People with conditions such as flat feet often turn to custom foot orthoses (FOs), which can be fabricated using 3D printing and scanning technologies at a reduced cost in less time. A team of researchers from Taiwan recently conducted a study, titled “Biomechanical Evaluation and Strength Test of 3D-Printed Foot Orthoses,” in order to evaluate the use of 3D printed FOs by people with flat feet.
“The purposes of this study were to fabricate FOs using low-cost 3D printing techniques and evaluate the mechanical properties and biomechanical effects of the 3D-printed FOs in individuals with flexible flatfoot,” the researchers wrote.
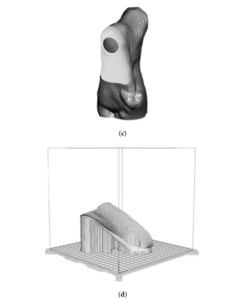
Figure 1: Fabrication of the 3D printed FOs. (c) Extraction of the FO shape from the foot model. (d) Solid FO model imported into Cura to be sliced and output as G-Code.
They 3D printed 18 FO samples, at orientations of 0°, 45°, and 90°, and subjected them to human motion analysis, with 12 flatfooted individuals, as well as mechanical testing to determine their maximum compressive load and stiffness.
The researchers 3D scanned the participants’ feet, and exported the result as an STL file, which was edited with Autodesk Meshmixer software and 3D printed out of PLA filament on an Infinity X1 FDM 3D printer. The build parameters of the FOs were defined using Ultimaker Cura 3.3 software.
“Because no standard tests for FOs exist, we designed a procedure to test the stiffness of the FOs,” the researchers explained. “A rectangular fixture measuring was placed on the lateral side of each FO.”
Then, six 3D printed FOs for each build orientation were put through dynamic compression, and the team collected displacement and reaction force data. An ANOVA, or one-way analysis of variance, test, and a post hoc Tukey’s test, were also completed in order to compare the maximum compressive load and stiffness of the FOs.

(e) FO 3D printed using an Infinity X1 3D printer. (f) Top view and (g) rear view of the 3D printed FO.
“The executed compressive tests revealed that the 45° and 90° build orientations engendered similar load and displacement behaviors in the FOs when the displacement was less than 5 mm,” they wrote. “The ANOVA revealed differences between groups. The Tukey test demonstrated that the maximum load in the FOs fabricated using the 45° build orientation ( N) was significantly greater than those in the FOs fabricated using the 90° ( N) and 0° ( N) build orientations.”
The participants were also subjected to a motion capture experiment, where both kinematic and kinetic data were collected by an eight-camera 3D Vicon motion analysis system. They had to “perform five trials of level walking at a self-selected speed” wearing standard shoes, and then the shoes embedded with 3D printed FOs.
The team again performed an ANOVA test to compare mechanical parameters of the FOs from each of the three build orientations; a paired-sample –test was also conducted in order to compare biomechanical variables from the motion capture tests.
“The results indicated that the 45° build orientation produced the strongest FOs. In addition, the maximum ankle evertor and external rotator moments under the Shoe+FO condition were significantly reduced by 35% and 16%, respectively, but the maximum ankle plantar flexor moments increased by 3%, compared with the Shoe condition. No significant difference in ground reaction force was observed between the two conditions,” the researchers wrote. “This study demonstrated that 3D-printed FOs could alter the ankle joint moments during gait.
“We can conclude that the low-cost 3D printing technology has the capability of fabricating custom FOs with sufficient support to correct foot abnormalities. We provide evidence that such FOs engender biomechanical changes and positively influence individuals with flexible flatfoot.”
Co-authors of the paper were
What do you think about this news? Discuss this story and other 3D printing topics at 3DPrintBoard.com or share your thoughts in the Facebook comments below.
Subscribe to Our Email Newsletter
Stay up-to-date on all the latest news from the 3D printing industry and receive information and offers from third party vendors.
Print Services
Upload your 3D Models and get them printed quickly and efficiently.
You May Also Like
3D Printing News Briefs, June 28, 2025: Defense Accelerator, Surgical Models, & More
In this weekend’s 3D Printing News Briefs, 3YOURMIND was selected to join an EU Defense Accelerator, and PTC has announced model-based definition (MBD) capabilities within Onshape. Finally, a study out...
3D Printing News Briefs, June 7, 2025: Digital Inventory, Thermal Management Solutions, & More
In this weekend’s 3D Printing News Briefs, UK-based 3D printing bureau 3D People responds to global instability, and AEWIN chose Fabric8Labs’ technology for advanced thermal management solutions. We’ll end with...
Low-Cost Binocular Indirect Ophthalmoscope Made with CAD Software & Bambu Lab X1C
3D printing is increasingly used in the fabrication of diagnostic equipment, including ophthalmology, which is a medical specialty that deals with the diagnosis and treatment of eye conditions and diseases....
3D Printing News Briefs, May 17, 2025: Color-Changing Materials, Humanoid Robot, & More
We’re covering research innovations in today’s 3D Printing News Briefs! First, Penn Engineering developed 3D printed materials that change color under stress, and UC Berkeley researchers created an open source,...