Evonik’s Sylvia Monsheimer “We Know the Right Buttons to Adjust Materials & Process to a Series Capable Solution”
Evonik has long had a light footprint but an outsized influence and revenue in 3D printing. The German $14 billion revenue group makes a significant portion of the sintering powders used worldwide. Evonik entered the 3D printng industry years ago and has engineered better powders all the while shoring up what has always seemed like an unassailable lead in sintering (powder bed fusion). Now many other chemical and polymer companies are making big splashes and investments in 3D printing, many have to be eyeing those many tonnes of powder being used in sintering. So what is Evonik’s next move? We got to interview with Sylvia Monsheimer, Head of New 3D Technologies Evonik Resource Efficiency GmbH, an engineer by trade who has spearheaded Evonik’s 3D printing effort for over two decades. Sylvia was also the person who first, along with a team, made Evonik PA 12 work on sintering machines which means she’s made her company enough money to buy Borussia Dortmund four times over (Borussia is sponsored by Evonik). From what we’ve grasped, she has true deep knowledge and understanding in 3D printing and will guide Evonik during this far more competitive era.
Why is Evonik interested in 3D printing?
The 3D printing market is booming, with growth rates in the double digits. Evonik is willing to support that growth actively offering its wide product portfolio of high-performance polymer materials and additives.
What kinds of products do you have now?
Evonik is the world’s leading manufacturer of polyamide 12 (PA 12) powders, which have been used in additive production technologies for over 20 years now. Our broader spectrum of polymer powder formulations for powder-based technologies includes everything from flame-retardants to elastic, ready-to-use materials like PA 12, polyamide 613 for applications in higher temperature range, thermoplastic elastomers of our PEBA grade as well our brand new copolyester powders based on the Structured Polymers technology Evonik acquired in January.
Beside our polymer powders, we offer a range of high-performance filament materials for medical implant and devices like our PEEK filament of the VESTAKEEP brand as well as our bioresorbable polymer of the RESOMER brand suitable for fused filament fabrication.
In addition, Evonik is one of the leading manufacturers of nano composites. Silica-based nanoparticle composites boost the performance of 3D printed products. They can be used in numerous 3D printing technologies like for example stereolithography.
Our portfolio of specialized additives such as powder flow control agents, rheology control agents or reactive modifiers complete Evonik’s contribution to the 3D printing market.
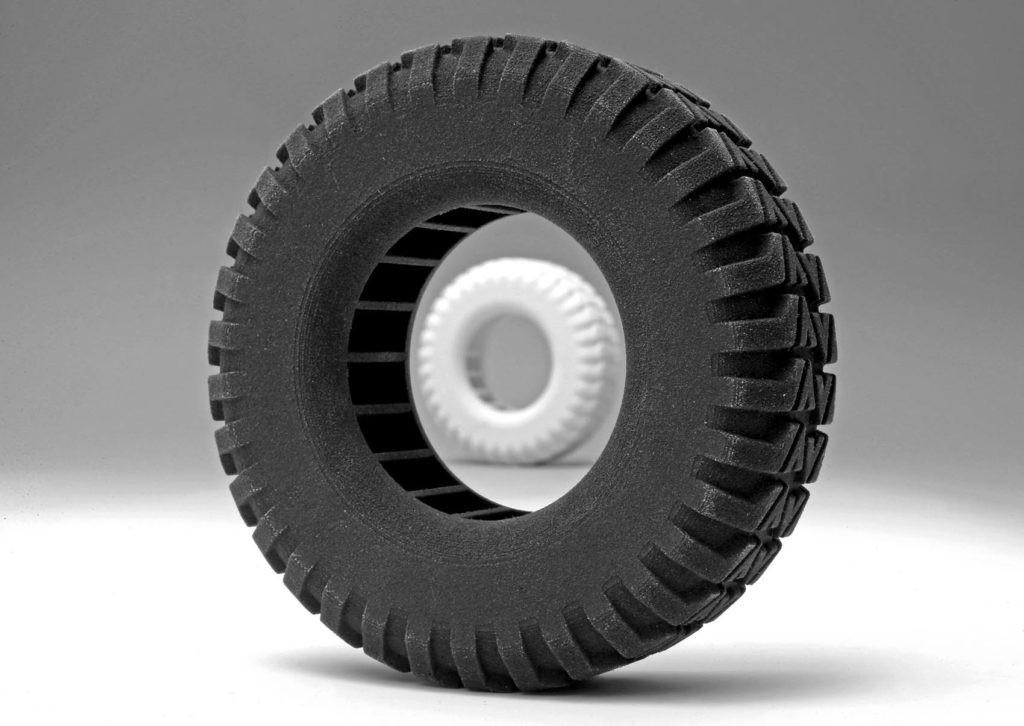
Evonik’s new copolyesters
What types of products will you develop?
Evonik keeps on developing new ready-to-use material systems for common technologies in order to move the process of 3D printing a big step closer to industrial manufacturing. We are targeting new applications – where new means new for 3D printing – and we are looking for partners who plan to set up the technology for their applications, always with the aim series production.
What are you doing with photopolymers?
Photopolymers are part of our innovation projects across the globe. For example, our Asia Research Hub which is located in Biopolis, the home for international and groundbreaking research in Singapore, focuses on ready-to-use photo resins for SLA in order to bring existing material portfolio into applications.
At the marl chemical site in Germany, we team up with Cubicure, a spin-off company of Vienna University of Technology, to jointly develop innovative radiation-curing resin systems.
You seem to have a strong SLS focus, will you make more products for FDM or other technologies?
Evonik bundles its competencies in 3D printing within the group’s Additive Manufacturing innovation growth field. Our strategic focus is on developing and manufacturing “ready-to-use” high-performance materials to meet the requirements of major technology lines. We’re strongly focusing our overall activities on SLS/HSS/MJF, FFF/FDM and SLA. Our existing portfolio of materials and additives align to our strategy.
How did Evonik first come to be involved with 3D Printing?
It is more than 20 years ago that we started selling materials for the SLS technology, and nearly for the same time we started to use SLS machines for development, Quality assurance, and the exploration of base understanding. Of course, in the meantime we added a lot of other technologies, commercial and not yet commercial, to our lab.
How about you personally, how did you first enter this market?
I personally started more than 20 yrs ago, with PA12 powder that had to be adjusted to the SLS process. With the machine progress over so many years also the materials have to be tweaked. And still, the PA12 is a success story.
What has changed over the time you’ve been involved?
The most relevant changes had come when the base technology patents expired during the past 10 years. That opened opportunities for new players. And, last but not least, the media hype we saw helped to boost creativity everywhere around additive manufacturing and led to programs in order to establish series production. All technologies are getting faster and faster, and completely new technologies are entering the market. This is an exciting development!
Will you be releasing more PAEKs and other high-performance polymers?
Evonik keeps on developing new ready-to-use material systems for common technologies in order to move the process of 3D printing a big step closer to industrial manufacturing. Like I mentioned before: if there is any potential for series application which requests a new material, also in the area of PAEK, we are open to develop new high-performance materials for additive manufacturing. It always starts with a market request.
Everyone seems very application focussed now, developing materials for specific applications? Are you?
That is definitely the way to go. It is the right signal to establish series production using 3D printing technologies. But the development and optimization for a certain technology that is used is a prerequisite. And here Evonik can use years of experience; we know the right buttons to adjust materials and process to a series capable solution.
What will you be doing with copolyesters for SLS? Why is this needed?
Our aim is to provide new material systems in order to further diversify the market for 3D printing materials and drive it towards industrial production. This is the first copolyester material for powder bed fusion processes in the market and we are excited to broaden our portfolio again.
You also have made new flexible SLS materials?
As the first product of the Structured Polymers technology, which was acquired in the spring of 2019 for the production of specialty polymer powders, Evonik has developed thermoplastic elastomers based on innovative copolyesters for powder-based 3D printing technologies. The new ready-to-use material is both highly elastic and tough and can be produced in white or black, depending on the application case. It expands the company’s flexible thermoplastics product range for powder-based 3D printing technologies, supplementing the existing PEBA powder. All polymer powders are suitable not only for SLS but also HSS and other powder-based technologies.
What is holding back 3D printing?
We aim for the use in series production: but production is not only the 3D printing step – what is lacking for many series applications is the integration and automatization within a production chain. And this has to be solved application by application and for each customer. The transfer of pre- and postprocessing steps which are known from injection molding has to be modified and set up for 3D printing parts. Finally, new materials sometimes require new machines!
What advice do you have for a company that wants to manufacture using 3D printing?
The most important thing is support from the top management through the organization. The use of 3DP might affect organizational topics if you want to address the full potential – it might change the way how you produce. And new or redesigned parts are important to use the technology efficiently.
What do you hope to achieve over the next five years?
“I would like to see exciting new series production applications.”
Will you offer products for desktop 3D printers?
“We already cater to that! There are already small desktop printers on the market using powder bed fusion technologies with Evonik’s material.”
How do you see the 3D printing market evolving?
We are seeing a major shift toward real production, and our aim is to be an established supplier for this new production technology. Beyond fulfilling technical needs, it also makes sense for us to offer scale-up skills, quality assurance, and reliability. However, for the technology to really take off, machine availability is crucial—and here I am talking about machines capable of production. Evonik is prepared to supply material after 3D printing takes off.
Subscribe to Our Email Newsletter
Stay up-to-date on all the latest news from the 3D printing industry and receive information and offers from third party vendors.
Print Services
Upload your 3D Models and get them printed quickly and efficiently.
You May Also Like
Could 3D Printing for Biocomputing Make Wetware Aware?
As an AI arms race consumes ever more electricity, and every ChatGPT search query costs $0.36, the search for new ways of computing has intensified. One answer could be in better...
Bambu Lab Launches Software to Manage 3D Printer Fleets—No Cloud Needed
Bambu Lab has introduced a new software tool, Bambu Farm Manager, designed to help users manage large fleets of 3D printers over a local network, without relying on the cloud....
Consolidation in AM: How 2025 Is Shaping the Industry’s New Normal
The first half of 2025 has been marked by a clear shift in the additive manufacturing (AM) industry. Companies are no longer just focused on developing new tech by themselves....
3D Printing News Briefs, July 2, 2025: Copper Alloys, Defense Manufacturing, & More
We’re starting off with metals in today’s 3D Printing News Briefs, as Farsoon has unveiled a large-scale AM solution for copper alloys, and Meltio used its wire-laser metal solution to...