3D printing has previously been employed to create passive mechanisms and machines, as well as the actuators used to make them go. According to a new paper, titled “A Miniature 3D Printed On-Off Linear Pneumatic Actuator and Its Demonstration into a Cartoon Character of a Hopping Lamp,” using 3D printing to create actuators can speed up design and development, save on time and money, and allow for greater customization. Christian L. Nall from the University of Texas at San Antonio and Pranav A. Bhounsule from the University of Illinois at Chicago wrote and published the paper, which presents their work creating and fabricating a small double-acting, On-Off type linear pneumatic actuator with FDM 3D printing.
“In this paper, we explore the use of 3D printing to create a pneumatic actuator and its utility on a legged robot,” the pair wrote.
“The actuator has an overall length of 8 cm, a bore size of 1.5 cm, and a stroke length of 2.0 cm. The overall weight is 12 gm and it generates a peak output power of 2 W when operating at an input air pressure of 40 psi ( 275.79 kPa).”
There are several ways to create actuated robots with 3D printing, such as 3D printing the components, assembling them, and adding motors, or 3D printing joints within a machine structure and stopping the print to embed actuators. 3D printed soft pneumatic actuators have been made before, but not, as the researchers explain, “conventional linear pneumatic actuators with sliding joints…the main novelty of this work.”
“The fundamental challenges in creating such an actuator are achieving leak-proof, low friction, and a strong actuator that can withstand relatively high air pressure. We address these challenges by using the chemical treatment after 3D printing to achieve a strong and leak-proof cylinder, design of cylinder and the piston head to achieve a tight fit for the O-ring, supplementing plastic with metallic inserts in high-stress areas to improve durability, and the lubrication of surfaces to achieve low friction movement.”
The team used an Ultimaker 3 Extended and ABS material to create the cylinder head, body, and end cap, as well as the piston head; the piston rod, rubber O-ring, and galvanized steel bot were purchased off-the-shelf. Even though a fine resolution was used for the cylinder parts, they had a rough finish, so Nall and Bhounsule dipped them in acetone for 15 seconds to clear up the issue. This also reduced air leakage through fine pores.

(a) The orientation of the different sub-systems of the actuator during 3D printing, (b) parts before surface finishing, and (c) after surface finishing with acetone.
“One of the advantages of 3D printing is the ability to embed materials by stopping the print process. We used this feature to 3D print the piston head on the steel bolt,” the researchers wrote.
They 3D printed scaffolds first, and used visual cues to determine when to stop the print and place the bolt vertically between the scaffolds, with the head at the top. Then, the piston head was 3D printed on the bolt head, with the scaffolds used as support material. Once the scaffolds were removed, they were left with “the piston head on top of the steel bolt.”
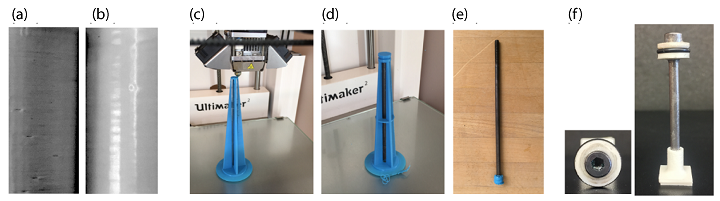
(a) Surface finish before and after (b) acetone treatment. (c) 3D printed scaffold followed by (d) bolt placement and printing the head and (e) bolt with piston head after removing the scaffold. (f) The 3D printed piston head is bonded to piston rod by an adhesive. The O-ring is manually placed in the groove on the piston head.
Then, it was time to put the actuator through its paces.
“First, we constrained the actuator to a sliding rail to measure the force and power generation capabilities,” they explained. “Next, we demonstrate unconstrained hopping and jumping motion by adding supports. Next, the actuator was incorporated on a Disney/Pixar inspired robot, Luxo Junior.”
A compressed air hose with pressure gauge was connecting to a double-acting solenoid valve’s inlet port, which used an Arduino Micro to allow pressurized air to flow between two output ports on the 3D printed actuator; this extended and retracted the piston rod. A piezoelectric sensor was used to measure how much force the actuator produced.
“The peak output power is 2 W at a supply pressure of 40 psi (275.79 kPa), maximum jump height is 3.93 cm, which is approximately 2 times the stroke length,” the team wrote.
By using external supporting legs, the 3D printed actuator can be used as a standalone robot, and was able hop in several scenarios, such as through the use of supports and vertically from a horizontal plane. Its average hopping height was about 5.34 cm – higher than jumps the actuator managed with a support rail.

(a) Actuator with supports demonstrating unconstrained hopping. (b) Actuator with supports for jumping from an inclined surface to the ground. (c) Actuator incorporated into legged robot based on Disney/Pixar Luxo lamp character.
“We also created a hopping lamp based on Disney/Pixar Luxo character,” they wrote. “The actuator was connected between the base plate and the vertical post of the lamp at a slight incline to the vertical. The actuator out-stroke timing was adjusted to provide sufficient thrust to the lamp. The thrust provided by the actuator powers the lamp forward by tipping and sliding motion. There was no flight phase, unlike the Pixar animation of the lamp. The speed of the lamp was 1.2 cm/s.”
The pair of researchers determined that it was possible to 3D print pneumatic actuators with excellent power-to-weight ratio, and “capitalize on the use of chemical treatment post-printing and waterproof grease to reduce friction that can improve force generation.”
“With the advent of cheaper and more capable 3D printers, we expect to see the steady rise of high power-to-weight ratio 3D printed actuators, leading to further improvements in robot design and control,” they concluded.
Discuss this and other 3D printing topics at 3DPrintBoard.com or share your thoughts below.
Subscribe to Our Email Newsletter
Stay up-to-date on all the latest news from the 3D printing industry and receive information and offers from third party vendors.
Print Services
Upload your 3D Models and get them printed quickly and efficiently.
You May Also Like
Josh Makeshift and the New Gold Standard 3D Printing Content Creation
In the beginning, 2007 or so, 3D printing videos were almost wholly absent from the web. Then, here and there, makers started to upload pictures of their rickety RepRaps and...
Phase3D Sets Up Online Store for Quality Assurance Software
Inspection software startup Phase3D has started an online store for its in-situ quality assurance Fringe Inspection software. This move should make it easier for people to quickly purchase the software...
Teen Developed Desktop 3D Printing Extruder
Inexpensive desktop 3D printing extrusion has always been an impactful potential ally to 3D Printing users. Filabot and 3Devo have been trying to make this a reality for years, with...
3D Printing News Briefs, June 4, 2025: Full-Color Slicer, Denture Implants, & More
In today’s 3D Printing News Briefs, we’ll start with some software and post-processing news, and then move on to a case report in which digital dentistry was successfully used. Read...