Ongoing Betatype and Safran Collaboration Results in Reduced Weight & Build Time for 3D Printed Electrical Generator Housing
London-based 3D printing consultancy company Betatype, founded in 2012, knows a little something about optimizing metal 3D printing applications in order to create functional components for customers in a wide variety of industries, such as aerospace, automotive, consumer goods, medical, and more.
Last fall, the UK company was approached by Safran Electrical & Power, which designs and fabricates electrical systems for fixed and rotary wing commercial and military aircraft, for help in improving the design of an electrical generator housing, and in 3D printing it as well.
“We came across Betatype in a search for additive manufacturing specialists and it was clear after our initial discussions that they had the knowledge and skillset we were looking for to add value in our new part production programme,” Dr. Mark Craig, the Materials, Special Processes and Composites Company Expert for Safran’s Power Division, said in the original case study.
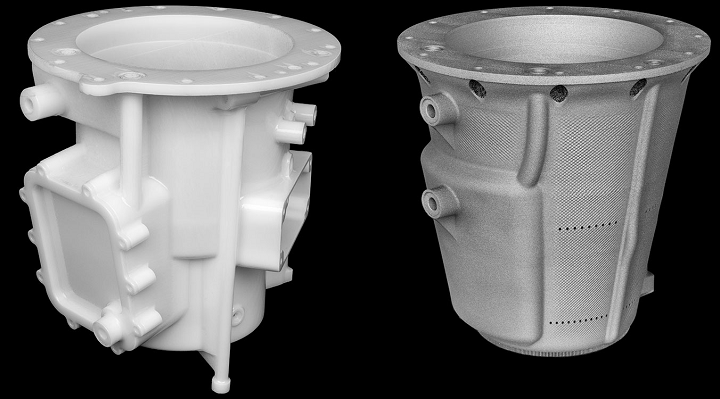
Auxiliary Power Unit Generator Housings, L-R: Current design for CNC machining, scale plastic prototype; First generation pilot part optimized for AM, designed and fabricated by Betatype, Grade 5 Titanium, full scale component (230 x 230 x 235 mm).
Here’s a quick recap of the original partnership: Betatype focused on some specific areas of the part – namely reducing the overall weight and improving its stiffness and strength – in its new and improved design. The company created a proof of concept, which was a first for one of its case studies: an ultra-high density lattice was used as part of a sandwich structure that had over ten million elements.
First Generation Auxiliary Power Unit Generator Housing: Section of pilot part highlighting metal foam core of outer wall sandwich structure.
“We knew creating a more complex, higher density lattice structure was the key to achieving what Safran was looking for in the part. Applying our technology and multi-scale approach, we were able to control the scan path and exposure settings down to each element of the sandwich structure’s design,” said Betatype CEO Sarat Babu. “By pushing laser powder bed fusion well beyond its standard processes, we created the ultra-high density lattice structure required.”
The proof of concept was a success – optimizing Safran’s original design for 3D printing and changing it from multiple machined components into a single part. In addition, Betatype was able to save costs and add value by majorly decreasing the amount of time it took to manufacture the housing, and reducing the overall part count.
Now, all of that information we already knew. But the collaboration between Safran and Betatype has continued since 2018, and the latest results are even more encouraging. Safran paired its knowledge and expertise of energy and power applications with Betatype’s main capabilities of software technology development and 3D printing application expertise to take the project to the next level.

Perspective views of Second Generation Auxiliary Power Unit Generator Housing Pilot Part, designed by Betatype, fabricated by Renishaw, Stone, AlSi10Mg.
The two companies continued to work on evolving Betatype’s original proof of concept, pushing the boundaries of what metal 3D printing can achieve. They combined Betatype’s scalable Process Control technology with specific application development, which helped reduce the weight of the complex part by 30%, when compared to the first generation version; additionally, this also lowers material use and waste.
They also used scan path optimization and precise process control, which standard AM software can’t offer, to increase productivity, make the build process faster, and ultimately reduce the build time by 30%. The collaborators also switched from using a sandwich panel on the part to using external ribbing, which helped maintain the necessary stiffness while reducing the profile volume, and also made it possible to 3D print the parts in aluminum, instead of titanium.

Top & bottom views of Second Generation Auxiliary Power Unit Generator Housing Pilot Part, designed by Betatype, fabricated by Renishaw, Stone, AlSi10Mg.
Betatype has helped Safran exceed its AM goals, and Safran is eager to continue using 3D printing to make other components and housings in the future.
Discuss this story and other 3D printing topics at 3DPrintBoard.com or share your thoughts in the Facebook comments below.
[Images: Betatype]Subscribe to Our Email Newsletter
Stay up-to-date on all the latest news from the 3D printing industry and receive information and offers from third party vendors.
Print Services
Upload your 3D Models and get them printed quickly and efficiently.
You May Also Like
U.S. Navy Lab Uses 3D Printing to Reduce Tooling Lead Time By Over 90%
The F-35 Lightning II Joint Program Office (JPO), responsible for life-cycle management of the key fifth-generation joint strike fighter (JSF) system used by the U.S., its allies, and its partners,...
Etsy Design Rule Change Reduces Selection of 3D Printed Goods
Online marketplace Etsy has implemented a rule change requiring all 3D printed goods on the site to be original designs. The update to the site’s Creativity Standards states, ¨Items produced using...
Honeywell Qualifies 6K Additive’s Nickel 718 for 3D Printed Aerospace & Defense Parts
6K Additive is renowned for manufacturing sustainable additive manufacturing (AM) powder, and offers a wide portfolio of premium metal and alloy powders that include titanium, copper, stainless steel, and nickel,...
MetalWorm Sells WAAM Systems to Research Institutes in Brazil and Malaysia
Turkish WAAM firm MetalWorm has sold a system in Malaysia and another in Brazil. This is an excellent example of a few emerging trends in additive. Firstly, WAAM was experimented...