In the recently published ‘Development and Mechanical Properties of Basalt Fiber-Reinforced Acrylonitrile Butadiene Styrene for In-Space Manufacturing Applications,’ we learn more about materials necessary for building in space; for example, a habitat on Mars would most likely be built out of a combination of materials from Earth as well as what is naturally found there, cutting expenses exponentially.
As technology progresses, we realize that space travel and colonizing will mean extreme measures in sustainability. As the reality of a NASA mission to Mars looms, there are years of preparation ahead, along with enormous research and development efforts required to figure out logistics and countless details. Materials science will figure in predominantly though as it is critical to areas like aircraft maintenance and more, but also colonization.
The researchers list the most important features for space material:
- Strength
- Stiffness
- Impact resistance
- Ability to shield from radiation
For the near future, the research team decided to develop and test a thermoplastic composite, mixing both acrylonitrile butadiene styrene (ABS) and basalt for testing at the Additive Manufacturing Facility at the International Space Station. During this study, one of the main considerations was the expense for transporting materials, leading to a strong focus on how much local material would be available and could be used.
“The most reasonable alternative is to use as much locally available material as possible along with any recyclable waste from cargo missions, such as packaging materials,” stated the researchers. “This is different than traditional composite material design, in which there is an optimization between the amount of reinforcing fibrous material that strengthens the material and cost of the fibrous materials.”
3D printing in space has gone from a concept to a reality as astronauts have been fabricating test items, tools, and more at the ISS. Test samples sent back to Earth have been reviewed and evaluated as successful, with a 3D printer now installed at the ISS permanently.
In examining the materials found on Mars, the researchers remind us that this smaller planet has a surface not unlike the crust found on Earth. Fine particles and basalt cover a volcanic rock layer around 6 to 30 miles thick. Basalt fibers can be made in a similar fashion to the manufacturing of glass fibers and then used for reinforcement. Previous research has shown basalt mixed with PLA quite successfully, but these projects were not centered around space travel and colonization.
The composite developed for this study was used with FFF 3D printing, in the form of a FlashForge Creator Pro 3D printer and 1.75mm filament. Five ratios were fabricated, and four were 3D printed in the end. Basalt can be easily mined and made into fibers, and while there were several choices of material to mix it with, the research team chose ABS because of low extrusion temperature and previous testing in microgravity experiments. It can be recycled too, and even used as packaging for other cargo.
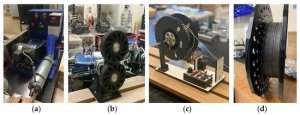
The filament manufacturing extrusion process (a) Single-screw extruder (b) Extrudate puller (c) Spooler (d) Spooled ABS-basalt filament.
Composite pellets were created for each fiber ratio, with accompanying 1.75mm filament. And while the 60 percent fiber ratio was assessed as too stiff for spooling and not suitable for small 3D printers, the researchers did not see that as an issue if large-scale printers were to be in use in space, fed by pellets. X-rays showed an even mix of the composite during both extrusion and deposition. They also proved that the material could be used for the fabrication of small tools.
“Further testing needs to be done on this material to learn about its fatigue strength (SN curve). Repeating similar testing to this paper but adding additional fiber content ratios between 25% and 40% would also be beneficial to future designers,” concluded the researchers.
“Fiber ratios above 40 percent should also be tested on large scale 3D printers equipped with a pellet extruder. Finally, studies should be conducted related to the recyclability of ABS packaging materials then used as an ABS-Basalt construction material for 3D printing.”
While 3D printing at the International Space Station is fascinating in its own right, the idea of colonizing the moon or Mars is doubly so; however, there is much ground to cover, from what type of materials and construction to use, to how long people will be able to sustain themselves. What do you think of this news? Let us know your thoughts! Join the discussion of this and other 3D printing topics at 3DPrintBoard.com.
[Source / Images: ‘Development and Mechanical Properties of Basalt Fiber-Reinforced Acrylonitrile Butadiene Styrene for In-Space Manufacturing Applications’]Subscribe to Our Email Newsletter
Stay up-to-date on all the latest news from the 3D printing industry and receive information and offers from third party vendors.
Print Services
Upload your 3D Models and get them printed quickly and efficiently.
You May Also Like
Reinventing Reindustrialization: Why NAVWAR Project Manager Spencer Koroly Invented a Made-in-America 3D Printer
It has become virtually impossible to regularly follow additive manufacturing (AM) industry news and not stumble across the term “defense industrial base” (DIB), a concept encompassing all the many diverse...
Inside The Barnes Global Advisors’ Vision for a Stronger AM Ecosystem
As additive manufacturing (AM) continues to revolutionize the industrial landscape, Pittsburgh-based consultancy The Barnes Global Advisors (TBGA) is helping shape what that future looks like. As the largest independent AM...
Ruggedized: How USMC Innovation Officer Matt Pine Navigates 3D Printing in the Military
Disclaimer: Matt Pine’s views are not the views of the Department of Defense nor the U.S. Marine Corps Throughout this decade thus far, the military’s adoption of additive manufacturing (AM)...
U.S. Congress Calls Out 3D Printing in Proposal for Commercial Reserve Manufacturing Network
Last week, the U.S. House of Representatives’ Appropriations Committee moved the FY 2026 defense bill forward to the House floor. Included in the legislation is a $131 million proposal for...