You may be familiar with 3D printing and even 4D printing now too, but 3D weaving is another technology offering improvements over its conventional 2D form in many different applications. After taking on a research contract from the United States Air Force Research Laboratory in 1991, the development team at Pennsylvania’s Bally Ribbon Mills (BRM) began to explore and master 3D weaving, able to produce structures helpful in applications such as aerospace, automotive, construction, the military, and more.
This new process which we previously wrote about allows users to create one-piece structures that are strong and complex and can be created with much lighter weight—making such pieces attractive to the aerospace industry as every pound eliminated can save fuel cost up to a staggering $1 million, including other operating costs too.
“Smart utilization of 3D woven composite structures in aircraft design can reduce the weight of an aircraft by up to 30 percent, resulting in considerable operational cost savings,” states the BRM team in a recent press release.
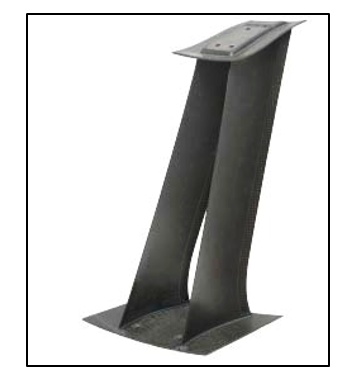
3D weaving benefits include weight reduction, elimination of delamination, reduced crack risk, lower production time, and cost reduction
Along with lightweight structures, these composites also offer new benefits such as:
- Reduced weight
- No delamination
- Less cracking
- Decreased production time
The BRM technique relies on adding a third axis to the 3D weaving process. While fabrics are conventionally woven on the X axis for length, and the Y axis for width, with the addition of the Z axis it is possible to make more sophisticated parts. This type of technology has previously not been possible without extensive tooling; however, with the advent of their research contract, BRM was able to construct an automated 3D bias loom, allowing them to create:
- Orthogonal panels
- Thermal protection systems
- Near-net shape
- Complex net shape preforms
Affordability is a major factor too, with cost savings available during both manufacturing and longevity of products which are resilient, requiring less maintenance and replacement.
“Automated 3D weaving technology and near net shape capabilities reduce direct labor and secondary machining costs,” explains the BRM team.
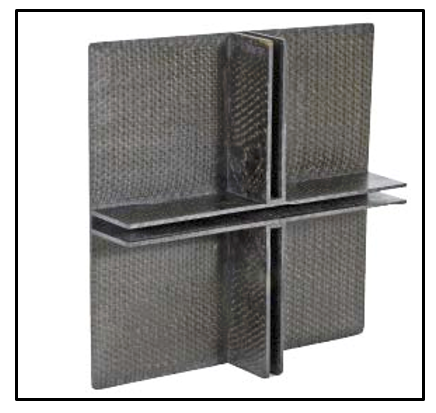
Replacing metal or 2-D laminated composites with 3-D composites reduces both manufacturing and operational costs.
And while use of polymers has been avoided previously due to manufacturing challenges, with the ability to switch out titanium for carbon fiber, weight is reduced along with noise levels. 3D weaving also advances aviation heat shield technology like thermal protection systems for space vehicles. Companies like BRM are able to modify yarns by density, width, and resin—meaning that materials can be completely customized for any space mission.
“Quartz compression pads, for example, have been woven by BRM for the Orion capsule in order to ensure structural strength during launch and heat resistance during re-entry,” states the BRM team. “Additionally, NASA’s Heatshield for Extreme Entry Environment Technology (HEEET) program is developing a carbon TPS for extreme entries, intended to be capable of surviving the challenging environments of Saturn or Venus. Both these technologies are being developed through extensive additional research, but both rely on the basic principles and strengths of 3D weaving.”
3D technology and weaving have been connected in numerous industry projects, from fashion, to structural applications, and generative design. What do you think of this news? Let us know your thoughts! Join the discussion of this and other 3D printing topics at 3DPrintBoard.com.
[Source / Images: Bally Ribbon Mills]Subscribe to Our Email Newsletter
Stay up-to-date on all the latest news from the 3D printing industry and receive information and offers from third party vendors.
Print Services
Upload your 3D Models and get them printed quickly and efficiently.
You May Also Like
Reinventing Reindustrialization: Why NAVWAR Project Manager Spencer Koroly Invented a Made-in-America 3D Printer
It has become virtually impossible to regularly follow additive manufacturing (AM) industry news and not stumble across the term “defense industrial base” (DIB), a concept encompassing all the many diverse...
Inside The Barnes Global Advisors’ Vision for a Stronger AM Ecosystem
As additive manufacturing (AM) continues to revolutionize the industrial landscape, Pittsburgh-based consultancy The Barnes Global Advisors (TBGA) is helping shape what that future looks like. As the largest independent AM...
Ruggedized: How USMC Innovation Officer Matt Pine Navigates 3D Printing in the Military
Disclaimer: Matt Pine’s views are not the views of the Department of Defense nor the U.S. Marine Corps Throughout this decade thus far, the military’s adoption of additive manufacturing (AM)...
U.S. Congress Calls Out 3D Printing in Proposal for Commercial Reserve Manufacturing Network
Last week, the U.S. House of Representatives’ Appropriations Committee moved the FY 2026 defense bill forward to the House floor. Included in the legislation is a $131 million proposal for...