In the recently published ‘Clinical Applications of 3-Dimensional Printing Technology in Hip Joint,’ authors Run‐zhi Xia BS, Zan‐jing Zhai MD, Yong‐yun Chang BS, and Hui‐wu Li MD explore current research regarding 3D printing techniques for hip joints. Looking at articles from as far back as 2015, they identified over 50 pieces of literature discussing 3D printed bony scale models, custom prostheses, and patient-specific instruments (PSI).
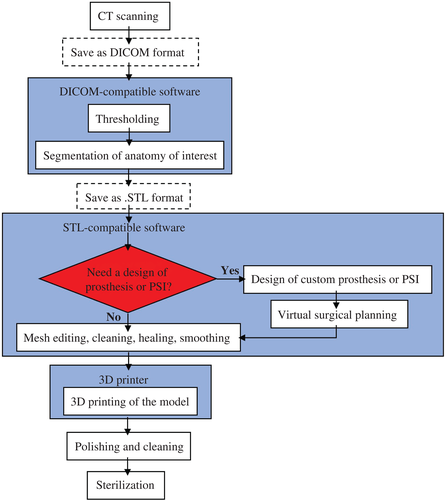
Whole process of three‐dimensional (3D) printing. CT scan obtained from the patients should be saved as digital imaging and communications in medicine (DICOM) format and imported into DICOM‐compatible software to conduct thresholding and segmentation of anatomy of interest. Then, the file should be saved in stereolithographic (.STL) format to be communicated to the STL‐compatible postprocessing software for further mesh editing, cleaning, healing, and smoothing. We can also design custom prostheses or patient‐specific instruments (PSI) for virtual surgical planning if necessary. Finally, the. STL file is imported into a 3D printer to result in the formation of 3D structures.
As the authors examine the uses of 3D printing and rapid prototyping in the medical field, they focus on the benefits that could be further offered in treatment for hip disorders. For creating 3D models, images are attained via CT scans and then imported into medical imaging processing software. Bones are differentiated through image thresholding, and an image is then created for the part of the anatomy in question.
“Accurate segmentation of the bones is key for reproduction of relevant anatomy in the 3D model,” stated the researchers. “It requires technical skill and for the radiologist to be experienced with the software segmentation tools. The custom cage and PSI can be designed using MIMICS software.”
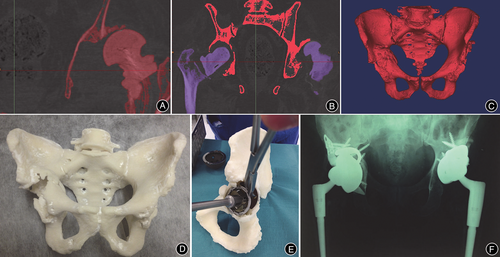
A, Image thresholding was performed by using software, which allowed for bone to be differentiated from surrounding soft tissue based on bone and soft tissue densities on the CT scan; B, Using the region growing process, both femurs were digitally segmented from their corresponding pelvis. The red pelvis will be retained, while the purple femurs will be removed; C, Once both femurs were erased, the 3D isolated image of pelvis (namely, the anatomy of interest) was created; D, The final life‐size 3D‐printed pelvis model, providing the surgeon with visual and tactile appreciation of the defects; E, Acetabular cup, augment, and buttress sizes, as well as cage dimensions were selected and trialed in preoperative surgical stimulation using a 3D‐printed pelvis; F, Postoperative anteroposterior pelvic plain film radiographs showed satisfactory revision total hip arthroplasty in situ17.
Because 2D images can be limiting, 3D printed models are used for a more in-depth understanding of the pelvis. The models are helping in diagnosing, treating, educating patients, and allowing for better preoperative planning procedures.
3D printed bony models are used for the following:
- Acetabular fracture
- Total hip arthroplasty
- Periacetabular osteotomy
- Slipped capital femoral epiphysis
3D printed prostheses are created for:
- Fractures
- Hip deformities
- Tumors
- Osteonecrosis of the femoral head
Patient-specific instruments are also fabricated for intraoperative assistance:
“To improve the accuracy of the PSI, several aspects should be considered, including CT image resolution, suitability of anatomical land marking, and manufacturing errors. Recently, an experimental in vitro study including 60 cases by Lee et al. showed that a CT‐based navigation system with PSI was more accurate and consistent than the conventional technique for assessment of femoral component position.”
PSIs are used in the treatment of fractures, dysplasia of the hip, tumors, osteonecrosis of the femoral head, and fibrous dysplasia. In discussing advantages of using 3D printing to make models, the researchers point out that they provide a comprehensive view for surgeons, allow for simulation of procedures, and have the ability to improve the operating room experience substantially. Prostheses can be customized to reduce bone resorption, and bone loss, also working with some implants that can also act as controlled drug delivery vehicles.
There are limitations too, as 3D printing may not offer the required resolution, with any deviation being of considerable concern. Affordability is an issue too with current 3D models costing anywhere from $200 to $1,000.
“However, some authors maintain a positive view; they believe that we no longer need to depend on intermediaries for using 3D printing technology. Excluding the investment in the printer, the costs per preplanned model are relatively cheap. In addition, in the manufacture of individualized prostheses, the clinically useful material is limited to metal, ceramic, and plastic,” concluded the authors.
“Research on other materials such as collagen, chondroitin sulfate, hyaluronic acid, and hydroxyapatite is still in the laboratory stage. However, with the development of tissue engineering and digital medicine, new materials and technologies, we anticipate that 3D printing technology will be widely used in the field of joint surgery.”
3D printed models are making impacts in the medical field, and are wide-ranging, along with the use of pre-operative planning devices and prosthetics. What do you think of this news? Let us know your thoughts! Join the discussion of this and other 3D printing topics at 3DPrintBoard.com.
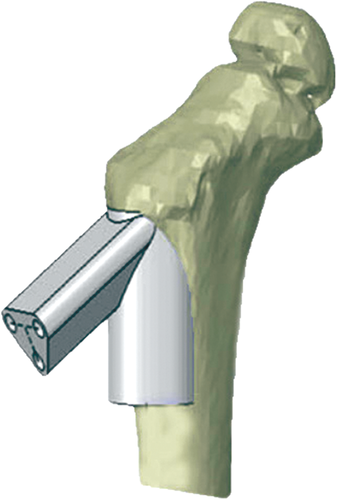
After reduction of the femoral neck fracture through software simulation, a navigation instrument was designed by the computer to conform to the proximal femur. The instrument provided optimal screw path and screw length for guiding pins and screws, which could be used to fix the Locking Compression Pediatric Hip Plate onto the fractured femoral neck during surgery
Subscribe to Our Email Newsletter
Stay up-to-date on all the latest news from the 3D printing industry and receive information and offers from third party vendors.
You May Also Like
Printing Money Episode 18: The DC Fly-In with Mark Burnham, AddMfgCoalition
It’s only been a week since the previous show, but Printing Money is back already with Episode 18. Certain events call for Printing Money’s coverage, and the recent 2nd Annual...
3DPOD Episode 199: Collaborative Design with Graham Bredemeyer, CEO of CADchat
About a decade ago, entrepreneur Graham Bredemeyer started Collider, a company that combined the best of 3D printing with injection molding. Now he runs CADChat, which hopes to make sharing...
Printing Money Episode 17: Recent 3D Printing Deals, with Alex Kingsbury
Printing Money is back with Episode 17! Our host, NewCap Partners‘ Danny Piper, is joined by Alex Kingsbury for this episode, so you can prepare yourself for smart coverage laced...
3DPOD Episode 198: High Speed Sintering with Neil Hopkinson, VP of AM at Stratasys
Neil Hopkinson, a pioneering 3D printing researcher, played a pivotal role in developing a body of research that is widely utilized today. He also invented High Speed Sintering (HSS), also...