As we move from prototyping to production, testing is becoming more and more important. Crucial in qualifying parts and materials, but also in establishing QA or developing new materials, testing in 3D printing is expanding rapidly. You can test for mechanical properties or functionally test a part for a particular application. You may want to measure parts through CMM or 3D scanning or may want them chemically tested. You may need to check if your shoe sole actually performs well as a sole or if your 3D printing filament gives off the wrong fumes. Large polymer companies often do this kind of thing themselves, but even they don’t do all of their testing in house. For regulatory, compliance or trust reasons as well it is sometimes better to turn to an independent testing lab. One of those is JTL America, which specializes in testing for orthopedics, automotive and aerospace parts. The firm has seen an increase in its 3D printing business and we decided to interview Mei Ogata and Kevin Knight of JTL America to learn more about testing for 3D printing.
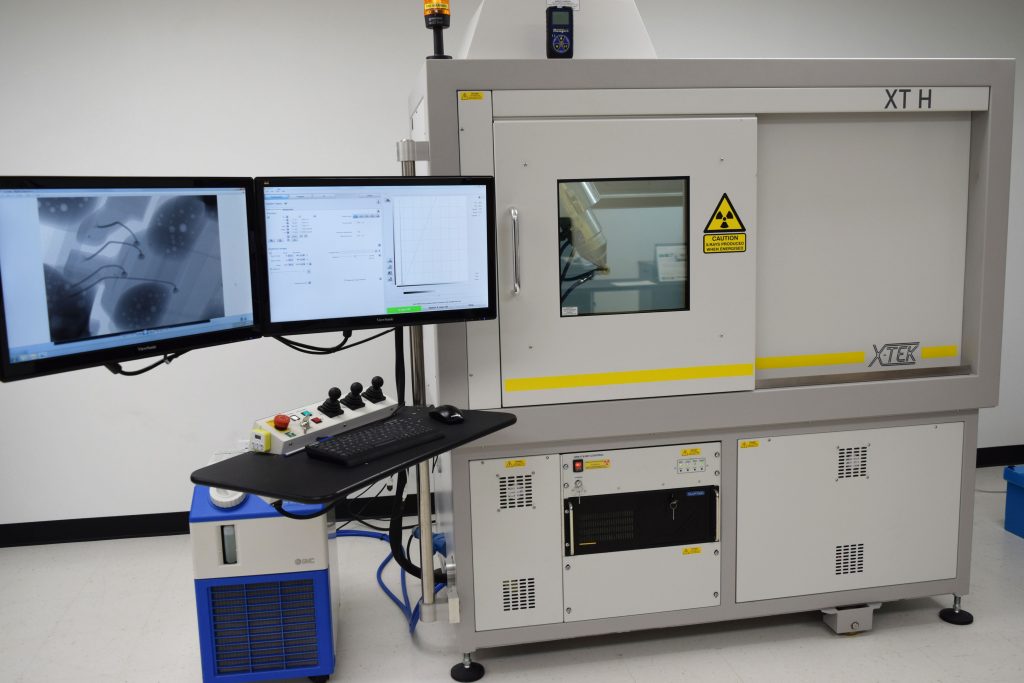
A CT scanner lets you see into a part. In metal 3D printed parts for example CT scanners can be used to see if the part has internal cracks.
What is JTL?
Mei: JTL America is an ISO 17025 accredited testing laboratory located in Fort Wayne, Indiana and Livonia, Michigan. JTL specializes in mechanical testing, vibration testing, and inspection by X-ray CT scanning and 3D scanning.
Why is testing important in 3D printing?
Each 3D printing machine has specific tolerances and 3D printed products may deviate from the actual intended dimensions.
Dimensional inspection by 3D scanning will provide colormaps overlaying the CAD model and the scanned parts to visualize the deviation. In addition, deviation labels and various profile measurement are available.
Mechanical testing such as fatigue, tensile, shear and compression testing will help understand and characterize 3D-printed material behavior.
The article, CT Scanning Proves to be an Effective Method for Qualifying 3D Printed Parts) talks about the importance of the CT scanning for additive manufactured parts.
JTL America provides X-ray 2D scanning and 3D CT scanning in addition to 3D surface scanning.
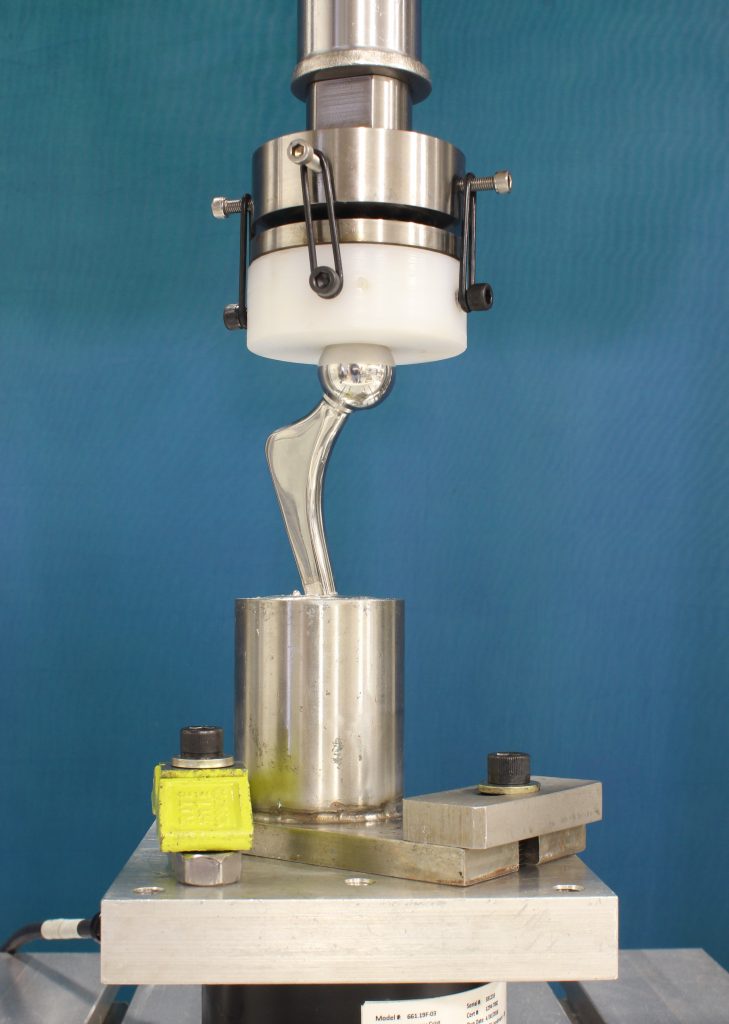
Mechanical testing of Orthopedic devices at JTL America
What types of customers do you wish to work for in our industry?
We mainly work for the Automotive, Aerospace and Orthopedic industry.
In the Orthopedic industry 3D printed implants are gaining popularity for two very important reasons. First, 3D printed implants can be designed and printed to match patient anatomy, eliminating the need to remove healthy bone. In traditional orthopedic surgery, the patient bone is cut or drilled to specifications defined by the implant design. When 3D printing is used, patient CT data is used to design the implant, preserving healthy bone which leads to better bone growth, smaller incisions, and faster healing time. Secondly, 3D printing allows implants to be printed with geometries that are not possible using traditional manufacturing methods. In particular, the porous trabecular structure of bone can be approximated using 3D printing. In total joint replacement in particular, it is important that the implant has a roughened, and ideally porous, structure to which new bone can attach and mechanically anchor itself. This process, called osseointegration, ensures that the implant will be well fixated in the patient bone in order to support the forces of daily living. Implants such as acetabular shells and tibial baseplates used in total hip and total knee replacements can now be printed with a truly porous structure and any thickness thanks to 3D printing technologies.
What services could you provide?
We can offer a lot of different testing services but the most popular are:
- 3D Scanning and dimensional inspection
- Mechanical testing
JTL will perform 3D scanning of 3D printed parts, then import the CAD model to the scanned data to overlay. Once a colormap is created, deviation labels are placed at relevant inspection areas. It is also possible to overly parts-to-parts to analyze the consistency.
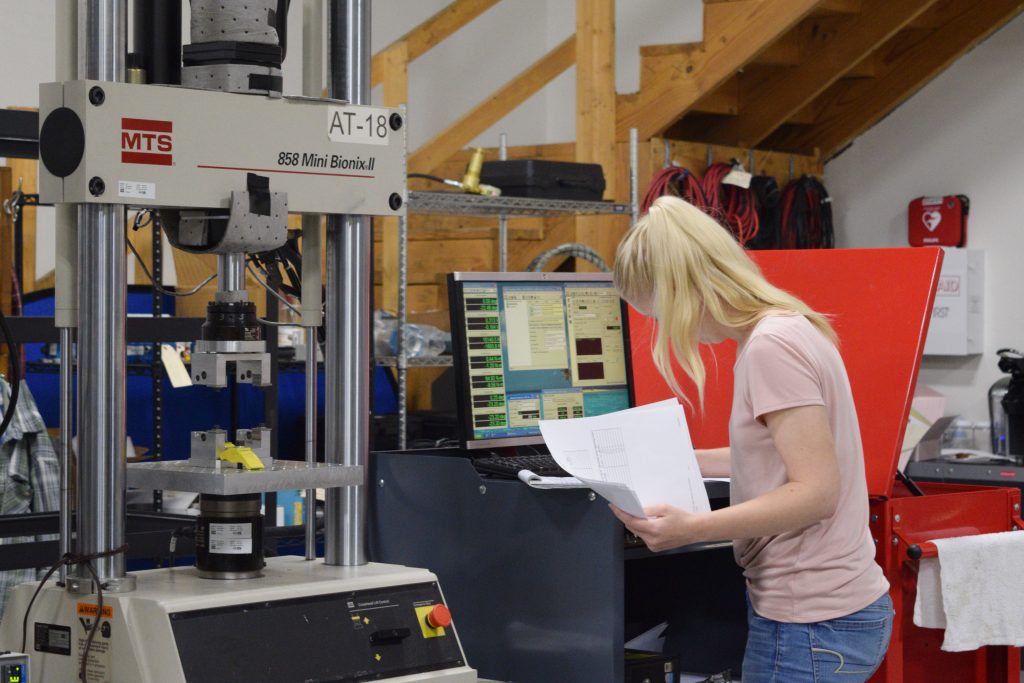
Mechanical testing at JTL America
Why would I outsource testing?
-
JTL America is a team of qualified test engineers who have the know-how from the years of its experience and has successfully completed many projects. Having JTL as a trusted testing partner will bring cost efficiency, reduce time to market and ensure the quality.
-
Using an independent and accredited testing laboratory add credibility and accountability to the testing results.
For a final parts producer what kind of testing would be interesting?
-
3D scanning
-
X-ray scanning to check inner structure
-
Mechanical testing
Is it difficult to test in 3D printing?
No. There is not much difference with other manufactured products. Mechanical testing of 3D printed parts is similar to printing traditionally manufactured parts.
Why is testing important to orthopedics?
Kevin: Testing is mandatory for orthopaedic implants. The FDA and regulatory agencies worldwide require that mechanical tests are performed on implant systems prior to approval for use. Aside from regulatory requirements, mechanical testing is important because it provides an assessment of the implants’ ability to withstand the forces generated during activities of daily life.
What can happen if I don’t do it?
If orthopedic implants are not tested, the risk of failure once implanted is increased because the mechanical integrity of the implant has not been evaluated.
Subscribe to Our Email Newsletter
Stay up-to-date on all the latest news from the 3D printing industry and receive information and offers from third party vendors.
Print Services
Upload your 3D Models and get them printed quickly and efficiently.
You May Also Like
The Market and Industry Potential of Multi-Material 3D and 4D Printing in Additive Electronics
Additive manufacturing leverages computer-based software to create components for products by depositing either dielectric or conductive materials, layer by layer, into different geometric shapes. Since its birth in the 1980s,...
3DPOD 262: Bio-inspired Design for AM with Dhruv Bhate, Arizona State University
Dhruv Bhate is an associate professor at Arizona State University. There, he looks at structures, materials, and design. Previously, he worked at PADT as well as in the semiconductor and...
3DPOD 261: Tooling and Cooling for AM with Jason Murphy, NXC MFG
Jason Murphy´s NXC MFG (Next Chapter Manufacturing) is not a generalist service; instead, the company specializes in making tooling. Using LPBF and binder jet, the company produces some of the...
3DPOD 260: John Hart on VulcanForms, MIT, Desktop Metal and More
John Hart is a Professor at MIT; he´s also the director of the Laboratory for Manufacturing and Productivity as well as the director of the Center for Advanced Production Technologies....