Researchers delve further into the relationship between technology, fabrication, and performance in ‘On the Impact of the Fabrication Method on the Performance of 3D Printed Mixers,’ examining how unibody lab-on-a-chip (LOC) devices perform, depending on whether they are printed via polyjet, stereolithography (SLA), and FDM (FFF) platforms.
LOC devices, usually created (as the name would infer) in science labs, offer greater efficiency to numerous applications, including:
- Chemical
- Biological
- DNA and protein analysis
- Food safety control
- Drug development

Computer-assisted design (CAD) drawing of the designed micro-mixer with dimensions in mm; (b) 3D model of unibody passive micro-mixer.
Previously, such devices offered specialized, beneficial services, but were also high-maintenance due to the need for skilled operators and expense. 3D printing has brought substantial advantages to the manufacturing of LOC systems and devices, however, with all the classic benefits—from the ease in design and production to the ability to create more complex geometries, and better affordability. The authors point out that the process becomes even more refined with the unibody-LOC concept, allowing for ease in making, assembling, and connecting.
“Despite the ubiquity of studies on the use of 3D printing technologies in microfluidic devices, cross-platform comparisons with regard to microfluidic performance are less common,” state the researchers.
Micro-mixers are critical to fabrication systems and consequence performance, as they are responsible for transforming the laminar into turbulent flow, usually by changing a structure or design—and functioning either through diffusion or chaotic advection. Most studies thus far, however, have been centered around basic research of simple parts and devices. And while SLA was previously considered to be the superior choice for fabricating micro-mixers, other 3D printers are certainly capable—and are examined in the study in relation to mixing quality, channel length, and fabrication.
Three samples were created, in the form of Y-shaped connected channels, with the main elements being the inlets, the main channel, and the outlet. Four different flow rates were evaluated in the study:
- 10 µL/min
- 50 µL/min
- 200 µL/min
- 400 µL/min
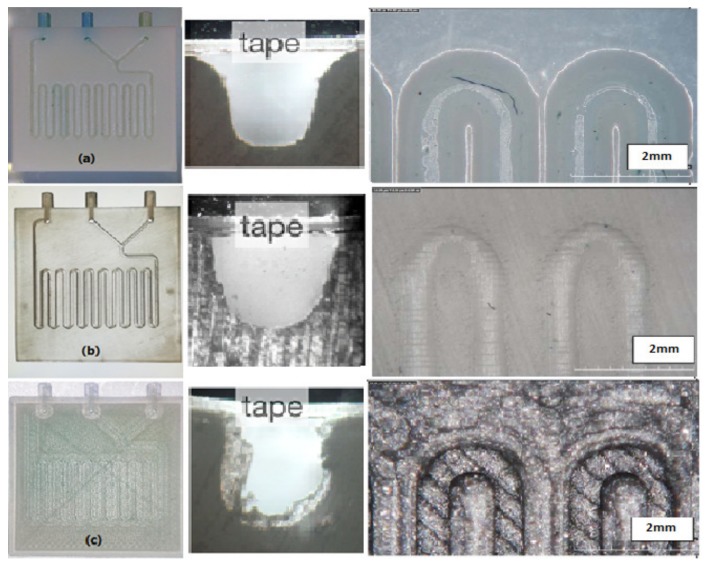
Fabricated micro-mixers by three different methods of printing. (a) micro-mixer with polyjet in cross-section and top view (b) micro-mixer with SLA in cross-section and top view (c) micro-mixer with FDM in cross-section and top view.
In SLA 3D printing, the researchers found the micro-mixer to be smoother and more transparent, while printable materials were difficult to even find for polyjet fabrication—along with high cost. FDM surfaces were less smooth, but materials were more accessible.
“The main advantages of FDM are its relatively low cost and the possibility of using different materials. The FDM LOC was also imaged with back illumination, whereas the polyjet was opaque and was imaged under ambient light,” stated the researchers.
“The polyjet method shows a higher fidelity than the SLA and FDM approaches. In FDM, due to the spreading of the polymer as it is extruded, the channel can be, in some sections, consistently smaller than the CAD model.”
Ultimately, the research showed that all the 3D printing processes would be suitable for the fabrication of micro-mixers. The authors noted that both FDM and polyjet processes ‘behaved better’ at low flow rates—but SLA offered the same performance for both lower and higher flowrates.
“Further studies on the relationship between surface micro and macro geometry, flow speed and completeness of mixing must be conducted through new tests with different flow rates and new channel micro and macro geometries,” concluded the researchers.
The lab on a chip is a progressive concept that continues to gain momentum and popularity amongst researchers interested in the benefits of microtechnology, from studying microfluidics and miniaturization to commercializing bioprinting platforms and creating new systems. What do you think of this news? Let us know your thoughts! Join the discussion of this and other 3D printing topics at 3DPrintBoard.com.
[Source / Images: ‘On the Impact of the Fabrication Method on the Performance of 3D Printed Mixers’]Subscribe to Our Email Newsletter
Stay up-to-date on all the latest news from the 3D printing industry and receive information and offers from third party vendors.
Print Services
Upload your 3D Models and get them printed quickly and efficiently.
You May Also Like
The Dental Additive Manufacturing Market Could Nearly Double by 2033, According to AM Research
According to an AM Research report from 2024, the medical device industry, specifically in dentistry, prosthetics, and audiology, is expected to see significant growth as these segments continue to benefit from...
Heating Up: 3D Systems’ Scott Green Discusses 3D Printing’s Potential in the Data Center Industry
The relentless rise of NVIDIA, the steadily increasing pledges of major private and public investments in national infrastructure projects around the world, and the general cultural obsession with AI have...
AM Research Webinar Explores Continuum’s Sustainable Metal Additive Manufacturing Powders
Metal additive manufacturing (AM) powder supplier Continuum Powders is working to develop solutions that empower industries to reduce waste and optimize their resources. An independent life cycle assessment (LCA) of...
3D Printed Footwear Startup Koobz Lands $7.2M in Seed Round
California-based Koobz is focused on reshoring the U.S. footwear supply chain with advanced manufacturing processes, including 3D printing. The startup just announced that it has added $6 million to its...