In ‘Analysis of the advantages of 3D printing in the surgical treatment of multiple rib fractures: 5 cases report,’ Chinese researchers from Shijiazhuang Third Hospital explore better ways to treat rib fractures, one of the most common types of breaks; in fact, as the authors point out, they make up nearly 80 percent of chest injuries. For this study, they examined cases of five patients with multiple rib fractures and created 3D models of the ribs, plus pre-shaped titanium alloy rib locking plates.
Research in past years has shown that ‘surgical intervention’ often results in better outcomes for patients with multiple rib fractures. There are, however, complex considerations in working with fracture sites that are more unique—presenting challenges for surgeons in deciding where to perform incisions. This is where the benefits of 3D printed models enter the picture, allowing for better planning for surgeries.
The study was ongoing from January 2017 to August 2018, examining all five patients, each of which had CT scans to confirm fractures. In each case, 3D printed models were made, and the rib locking plates were 3D printed—specifically to each patient:
Patient one – a 61-year-old male. The 3D printed model assisted in the creation of a two-rib titanium alloy frame locking plate ‘placed on the 3rd rib’s surface, and well fitted with the non-fractured end of the 3rd rib front and rear.’
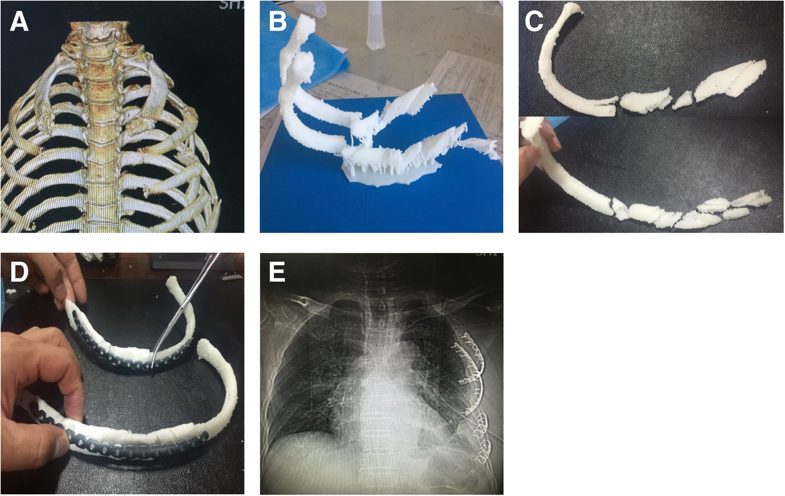
No.1 patient (a) Preoperative scanning revealed long segment comminuted fractures in 3 and 4 ribs. b Preoperative 3 and 4 rib models were prepared by 3D printing technology based on CT thin slice scanning. c, d Reduction fracture morphology; the 3D printing model was spliced and the titanium alloy rib locking plate was shaped according to the mode. e Postoperative review, the shape of the internal fixator was intact, and the shape of the contralateral rib was perfectly symmetrical compared with preoperative image A
Patient two – a 57-year-old male with multiple fractures of the left ribs. Surgeons decided to attach the inner end of the locking plate to the sternum the outer end to the rib bone.
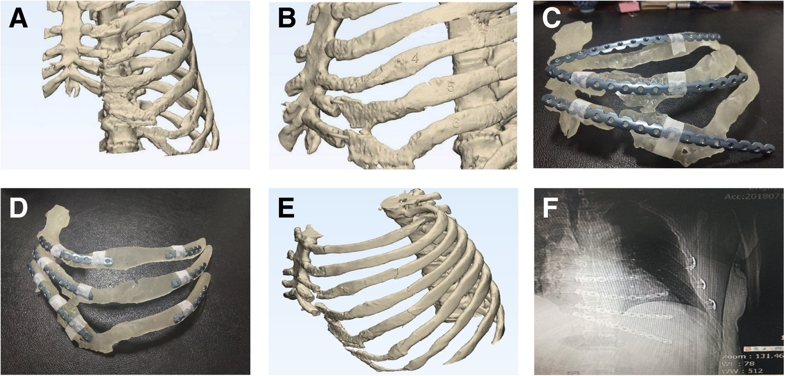
No.2 patient (a) According to the 3D model made by CT, 4 and 5 costal cartilage fractures and 6 costal anterior costal arch fracture can be seen. b The 3D model of the fracture end of the rib was adjusted by using 3D software model. c The 3D printed 4–6 rib model shows a large gap between the locking plate and the shape of the rib. d After giving the shape, the locking plate and the rib paste are in good condition. e, f Postoperative review, the shape of the internal fixator was intact, and the shape of the contralateral rib recovered well compared with the preoperative image
Patient three – a 64-year-old female. Surgeons were striving for minimally invasive surgery but were also required to protect breast tissue sufficiently. Ultimately, they affixed the locking plate’s medial side to her sternum body, with the sternum and armpit treated via ‘tunneling open reduction and internal fixation.’
Patients four/five – two male patients both had multiple fractures due to a car accident, with similar surgeries, performed ‘tunneling open reduction and internal fixation.’ A CT scan was used to create 3D models so that the broken ends of their ribs could be ‘adjusted and restored’ accordingly.
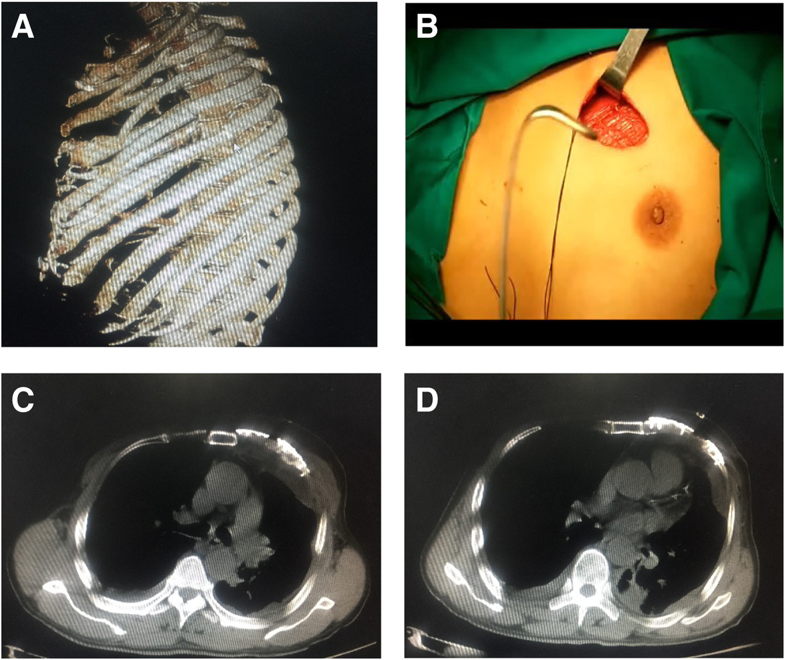
No.3 patient (a) Preoperative scanning revealed 2–11 left rib fractures where 2–6 ribs contained the costal cartilage multiple fractures involving the costal arch. b Preoperative 3–5 rib models were prepared by 3D printing technology based on CT thin slice scanning. c During the surgery, corresponding pre-shaping locking plates were placed in each rib
Overall, the study was a success, with no fatalities. Time in the operating room was around three hours at the most for each patient, with only one individual experiencing complications, resulting in an ICU stay for one day, due to respiratory issues.
“Postoperative chest radiographs of each patient showed that the internal fixation had good and natural shape,” stated the researchers. “There was good shape to the thoracic contour and [it] was basically symmetrical with the contralateral side.
“In conclusion, for the 5 cases of multiple rib fractures reported in this study, the preoperative application of 3D printing technology can fully reduce the shaping time of intraoperative internal fixator, the difficulty of operation and the injury of patients.
“Therefore, for some specific types of rib fractures, the preoperative application of 3D printing technology has potential significance in achieving precise and individualized treatment, but this method still needs more clinical experience to provide better services for patients.”
3D printing has offered huge advantages to surgeons, especially with models that can be used before and during surgery, allowing for better patient education, medical training for students and surgeons who may be attempting new procedures, and overall improved patient care.
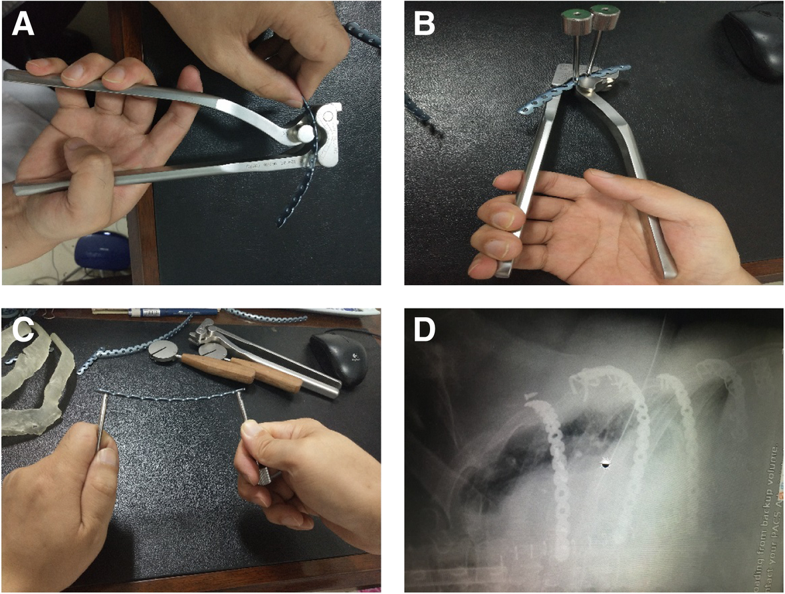
For fractures of the costal arch, a re-shaped locking plate is required. Adjust the (a) front and back radians of the rib lock, (b) upper and lower radians and (c) the rotation angle of the locking plate of the long axis of the ribs according to the 3D printing model. d the back end of the upper metal bone plate can be seen with abscission screw, the second metal bone plate is not ideal in shape, and the back end and the ribs are not well covered, and the embracing fixator is used as an accessory to prevent abscission
Subscribe to Our Email Newsletter
Stay up-to-date on all the latest news from the 3D printing industry and receive information and offers from third party vendors.
Print Services
Upload your 3D Models and get them printed quickly and efficiently.
You May Also Like
Making 3D Printing Personal: How Faraz Faruqi Is Rethinking Digital Design at MIT CSAIL
What if your 3D printer could think more like an intelligent assistant, able to reason through a design idea, ask questions, and deliver something that works exactly the way the...
Reinventing Reindustrialization: Why NAVWAR Project Manager Spencer Koroly Invented a Made-in-America 3D Printer
It has become virtually impossible to regularly follow additive manufacturing (AM) industry news and not stumble across the term “defense industrial base” (DIB), a concept encompassing all the many diverse...
Heating Up: 3D Systems’ Scott Green Discusses 3D Printing’s Potential in the Data Center Industry
The relentless rise of NVIDIA, the steadily increasing pledges of major private and public investments in national infrastructure projects around the world, and the general cultural obsession with AI have...
Formlabs Teams Up with DMG MORI in Japan
In late June, Nick Graham, Chief Revenue Officer at Formlabs, announced on LinkedIn that the company had partnered with DMG MORI, one of the world’s leading machine tool companies, to...