Acoustically Assembled Multidimensional Filler Networks 3D Printed Polymer Composites for Thermal Management
In ‘3D-printed polymer composites with acoustically assembled multidimensional filler networks for accelerated heat dissipation,’ authors Lu Lu, Zhifeng Zhang, Jie Xu, and Yayue Pa explore a new technique for printing composites with filler that could eliminate overheating in electronics. Part of the challenge for the researchers in this project was in thermal management and finding a balance in filler loading.
With acoustic field-assisted projection stereolithography, the research team focused on using just a small amount of filler to create a network of heat-diverting paths. This work could be critical to a variety of different applications, as many electronics are overloaded due to heating and may fail completely; in fact, the researchers include data from a U.S. Air Force survey reporting that over half of their issues with electronics are due to overheating. These problems need to be solved, in military applications especially, but also in other fields centered around chipsets, wearables, and flexible electronics.
Polymer composites are ‘promising’ due to their conductive qualities, along with being insulating and flexible. The traditional method involves mixing fillers in the matrix, with some success in adding ‘heavy filler loading.’ Historically, however, this has led to problems such as:
- Clogging
- Difficulty in mixing
- Agglomeration
- Trouble in filler embedding
- Limited manipulation of filler distribution
- Orientation issues
“Additionally, the manufactured composites with heavy filler loading usually suffer from insufficient binding, mechanical deterioration, and thermal expansion coefficient mismatch,” state the researchers. “The disordered distribution of fillers limits thermal performance enhancement due to the phonon scattering between isolated fillers.”
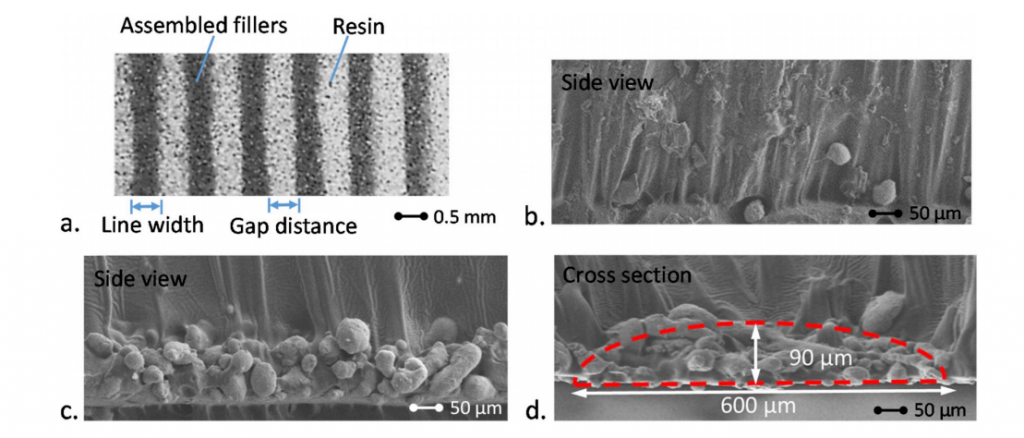
a. Photograph of parallel filler line pattern in liquid resin; SEM images of b.The uniform composite, c. The patterned composite, d. Acoustically assembled filler microstructure in cross-sectional view. (Filler: aluminum powder).
3D printing offers better results in alignment and orientation, but also allows for multi-material fabrication. Here, the researchers see the potential for superior performance with their acoustic-field-based filler manipulation technique, including the following features:
- Filler distribution controls
- Lack of manufacturing restrictions
- No filler shape or property requirements
The module is made up of electro-piezo elements, a function generator, and an amplifier.
“A function generator provides the sinusoidal signal with adjustable frequency and voltage. This signal is applied to the electro-piezo element after amplified. The piezo element actuation leads to structural deformation of the PET film, which subsequently induces an acoustic field in the filler-resin suspension. The acoustic radiation force drives fillers to the pressure nodes of the acoustic field to form a pattern,” state the researchers.
The team created five different composites, P1-P5, with the three patterned composites (P2, P3, P4) exhibiting better performance due to their 3D particle assembly networks—causing the researchers to state that the samples ‘proved the effects’ of filler assembly in regard to the new composite and technique.

a. Schematics of unit layers. b. Photograph of a printed sample P-1 and its microscopic images. c. Schematics of different filler distribution patterns and the microscopic images of fabricated samples in side views.
“By controlling the manufacturing parameters, such as the layer thickness and the projection mask, multidimensional filler networks formed,” concluded the researchers. “Multidirectional heat transfer paths provided by multidimensional filler networks accelerate the cooling process in the isolated polymer matrix. With the same feedstock or even the same number of particles filled in the polymer matrix, the patterned composites are superior to the uniform composite with significantly higher heat dissipation efficiencies.
“Future work will be to quantify the relationship of composite functionality with particle pattern design parameters.”
Composites are accentuating the realm of 3D printing materials as users in research, development, engineering, and industrial settings around the world seek better ways to make prototypes and products, including bioprinting structures—from graphene reinforced nanocomposites to wood composites and chitosan-gelatin hydrogels.
Find out more about 3D printing polymer composites for electronics here. What do you think of this news? Let us know your thoughts! Join the discussion of this and other 3D printing topics at 3DPrintBoard.com.
[Source / Images: ‘3D-printed polymer composites with acoustically assembled multidimensional filler networks for accelerated heat dissipation’]Subscribe to Our Email Newsletter
Stay up-to-date on all the latest news from the 3D printing industry and receive information and offers from third party vendors.
Print Services
Upload your 3D Models and get them printed quickly and efficiently.
You May Also Like
Consolidation in AM: How 2025 Is Shaping the Industry’s New Normal
The first half of 2025 has been marked by a clear shift in the additive manufacturing (AM) industry. Companies are no longer just focused on developing new tech by themselves....
Etsy Design Rule Change Reduces Selection of 3D Printed Goods
Online marketplace Etsy has implemented a rule change requiring all 3D printed goods on the site to be original designs. The update to the site’s Creativity Standards states, ¨Items produced using...
U.S. Congress Calls Out 3D Printing in Proposal for Commercial Reserve Manufacturing Network
Last week, the U.S. House of Representatives’ Appropriations Committee moved the FY 2026 defense bill forward to the House floor. Included in the legislation is a $131 million proposal for...
Transforming From Tourist to Native: Duro CEO Michael Corr Explains Why the Company Rebuilt its PLM Software on AI
In these early innings of the AI boom, many market analysts have expressed concern that AI spend has gotten too far ahead of the technology’s proven ability to deliver significant...