We’re very interested in connecting the 3D printing industry and have in a series of articles looked at organizations that are trying to bring us all together. We will need a voice in the media and in the political arena going forward and we don’t have one now. CECIMO is a European organization that connects Machine Tool Manufacturers and related firms. CECIMO’s interests are analogous to much of our industry and recently they have tried to engage the 3D printing industry and act on our behalf. We wrote about their stance on 3D printing legislation, their work in terminology and partnership with EPMA. Enough reason for us to wonder, who is CECIMO and what can they do for you? We interviewed Filip Geerts, Director General of CECIMO to find out.
Who do you represent?
Under our umbrella we represent 15 national associations of technology providers all over Europe. In turn, they all gather more than 350 organisations involved in one or more segments in the AM value chain: AM machine manufacturers, providers of software solutions, raw materials suppliers and manufacturers of post-processing equipment are all part of our family.
Why should I join?
You should join because we work to create the proper conditions to have AM thriving in Europe. We ease the involvement of AM companies in European law-making and convey their concerns on EU draft regulations or policies. For example, we work with policy-makers to guarantee the interest of AM businesses in new trade agreements or strategic public investment decisions. We also ensure supportive regulatory conditions on issues like AM product compliance Last but not least, we are a genuine platform for networking and discussion of business topics among peer companies.
And how much does it cost?
Any interested organisation can join CECIMO by becoming a member of the relevant national association in Europe. This membership allows access to two organisations at once. While the company can benefit from a variety of business services provided by the national association, at the same time it can also participate in CECIMO activities at European level. Membership fees are set out by national associations.
What advocacy is needed for 3D printing?
The latest potential developments are on issues like specific EU product compliance requirements and IP legislation and we have been collaborating closely with policy-makers on these subjects. It is vital for EU authorities to grasp what the technology can do and –especially– what cannot do at today’s level of maturity. We feel regulators are often perceiving industrial AM as a plug & play technique, which is not the case. In addition to these efforts, we also call the attention of European authorities to the significant investments that other regions in the world are earmarking for their local AM sector. China has recently pledged substantial funding support to its value chain as part of its ‘’Made in China 2025 strategy’’. America Makes in the US has managed a portfolio of AM R&D and workforce initiatives amounting to roughly $115 million between 2012 and 2018. Europe has gone to great lengths to support funding for its industry but, much of the EU funding is allocated to basic research activities where Europe has been traditionally strong. Considering the above international developments, Europe should focus on the commercialisation stage of new technologies and materials, and support SMEs in acquiring AM equipment and training. A few governments in Europe are running ambitious initiatives in this regard and we, as CECIMO, are putting emphasis on their positive effects on the modernization of industry.
What standards are needed?
There is a great variety of standards that need to be generated for serial AM production. In the short-term, two are the major areas: health and safety, and job profiles. First, AM users need standards in the health and safety field. In particular in metal additive production, we lack guidelines to mitigate and control risks associated with managing powders that pose flammability, inhalation or skin contact concerns. We also need standards on aspects like storage of metal powders and, importantly, AM-relevant facilities. Today, producers, interested to use this technology beyond prototyping purposes, are still hesitating because of missing standards. Second, we need a harmonised understanding of AM job profiles in Europe and validation of AM competences that have been acquired outside of formal education systems. The definition of job needs and knowledge requirements of a specific figure (i.e. a powder bed fusion operator) would ease the development of training modules in VET and higher education. It would also help employers’ in identifying the skills of an employee or a future one.
In the longer-term, we need to work on application-specific aspects, be them on materials, design, processes or finished components.
Are we doing enough on safety?
If we look at AM systems, the existing EU legislative requirements are quite comprehensive, but need better procedures in the conformity assessment, so to reduce the administrative burden on companies.
Industry is also putting a great deal of efforts in developing health and safety standards which will accelerate the uptake of the technology in the industrial environment. For example, ISO and ASTM are preparing end-to-end guidelines on the use of metallic materials, detailing recommended measures from the moment these materials reach the factory to when they are disposed.
In addition, there are strict requirements for AM components for sectors like aerospace and medical, where safety plays a vital role.
What regulatory hurdles are there?
Looking at recent trends, our concerns are more oriented towards possible new developments rather than the content of existing EU provisions. In addition to the examples given in the next answer, Nevertheless, we carefully monitor the interaction between AM, other emerging Industry 4.0 technologies and horizontal issues such as cybersecurity.
Do you anticipate people trying to legislate 3D printing differently?
We pay a great deal of attention to inform European authorities on the impact that specific regulations or policy initiatives would have on European AM. For example, CECIMO is collaborating with EU negotiators to deliver a final trade agreement that boost further EU-US trade of AM solutions. Some other EU initiatives, on the contrary, such as a proposal of legislation on intellectual property, may lead to negative consequences. CECIMO has been raising awareness on how current EU IP legislation is already appropriate to govern industrial AM, and how the real barriers for the technology’s uptake are actually elsewhere. Another aspect of relevance for healthcare applications is whether AM medical components will be considered custom-made devices or patient-matched devices under the new Medical Devices Regulation that will soon enter into force.
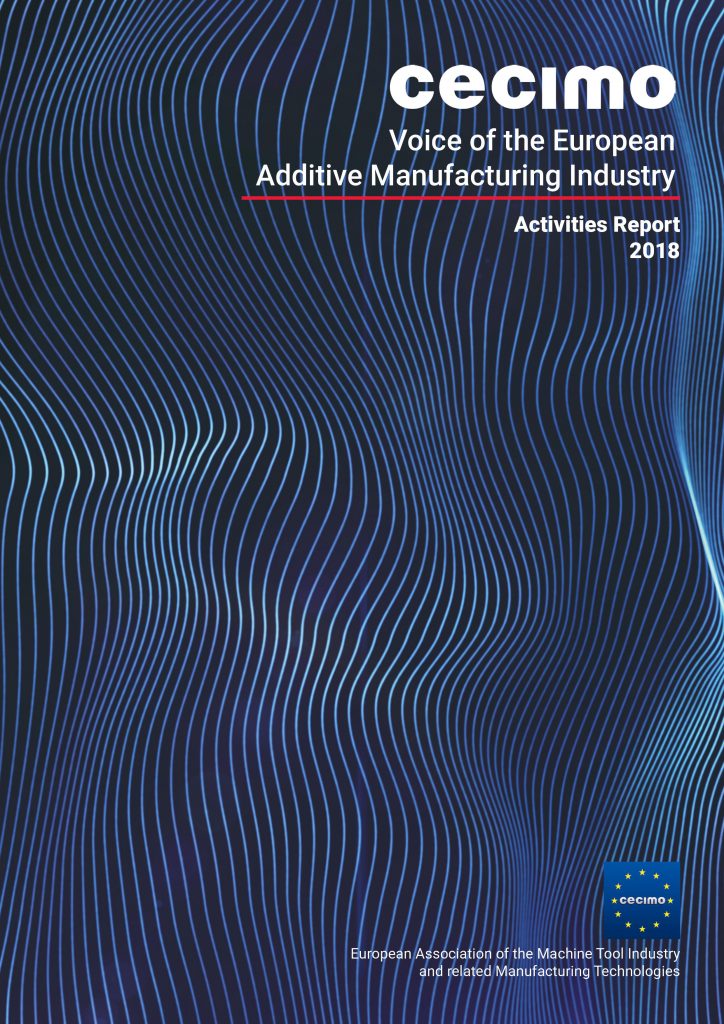
CECIMO has an Additive Manufacturing Activities Report to show you what they’re up to.
What is holding back 3D printing?
While the industry continues to grow, there are a variety of barriers which still deter companies from deploying AM in their production chain. In addition to standards mentioned before, one is the lack of skills: there’s a shortage of designers competent in DfAM and capable to spot precisely when it is more convenient to adopt AM. You can’t just produce additively all that you want. In addition to that, although more organisations are joining the materials’ supply segment of the market, there is still a limited set of suitable materials. The overall cost of powders exceeds that of billet, and the use of more than one type of powder per AM equipment remains an issue.
Another barrier, for metal-based technology in particular, is post-processing. AM does not replace machining, as the latter is needed to improve the mechanical properties of the component built. The complex shape of the part may also lead to problems in terms of fixturing. Parts may also require heat treatment and surface finishing treatment.These are all obstacles which underline how deploying industrial AM in the company requires patience. It takes time to build a business case around the technology. But once this is established, the rewards are high.
Subscribe to Our Email Newsletter
Stay up-to-date on all the latest news from the 3D printing industry and receive information and offers from third party vendors.
Print Services
Upload your 3D Models and get them printed quickly and efficiently.
You May Also Like
3D Printing News Briefs, July 2, 2025: Copper Alloys, Defense Manufacturing, & More
We’re starting off with metals in today’s 3D Printing News Briefs, as Farsoon has unveiled a large-scale AM solution for copper alloys, and Meltio used its wire-laser metal solution to...
3DPOD 260: John Hart on VulcanForms, MIT, Desktop Metal and More
John Hart is a Professor at MIT; he´s also the director of the Laboratory for Manufacturing and Productivity as well as the director of the Center for Advanced Production Technologies....
3D Printing News Briefs, June 28, 2025: Defense Accelerator, Surgical Models, & More
In this weekend’s 3D Printing News Briefs, 3YOURMIND was selected to join an EU Defense Accelerator, and PTC has announced model-based definition (MBD) capabilities within Onshape. Finally, a study out...
EOS in India: AM’s Rising Star
EOS is doubling down on India. With a growing base of aerospace startups, new government policies, and a massive engineering workforce, India is quickly becoming one of the most important...