Chinese scientists are delving further into successful bioprinting in ‘3D printing of complex GelMA-based scaffolds with nanoclay,’ exploring why photo-crosslinkable gelatin methacrylate (GelMA) has become so enticing for researchers attempting to engineer tissue. In a realm rife with obstacles, however, GelMA is no exception—constricted by viscosity issues and long cross-linking time.
The authors decided to bolster the ink further with nanoclay, in the hopes of being able to print stable, complex scaffolds. During this study, they evaluated windows for printability, issues with porosity and mechanical strength, and biocompatibility.
Obviously, without cell viability, there is no bioink and there are no spectacular innovations to write about. A wide range of hydrogels have been used successfully, with alginate commonly involved due to rapid crosslinking speed. Here, however, the researchers explain that alginate is not always conducive to attachment of cells or good function. Gelatin methacrylate (GelMA), however, is known to crosslink easily during light exposure. The researchers point out also that it maintains the biocompatibility of gelatin.
In attempting to overcome multiple issues with the use of GelMA, such as low viscosity and extensive time required for cross-linking, they examined the use of pre-crosslinking, post-crosslinking, in-situ crosslinking, and two-step crosslinking. Ultimately, the consensus was that all the methods were unsuitable, resulting in inferior stability. With the addition of nanoclay, however, the authors discovered that the ink had higher viscosity, and the GelMA scaffolds had better shape fidelity.
“After extrusion, the nanoclay rapidly converted to the gel state upon the release of shear stress, thereby forming stable hydrogel filament,” stated the authors. “Finally, the 3D structure was printed layer-by-layer by stacking the filament, and the GelMA within the filament was covalently crosslinked under UV light, resulting in a stable scaffold.”
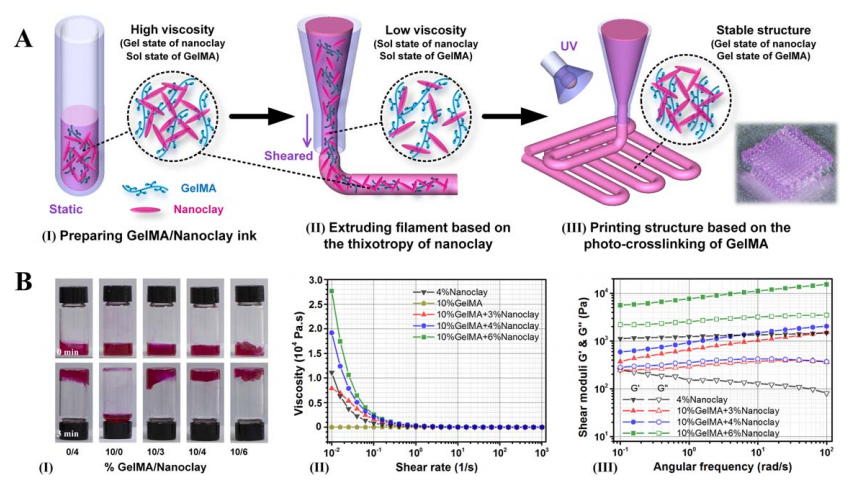
3D printing strategy of complex scaffolds with GelMA/Nanoclay ink. (A) Schematic illustration of printing scaffolds with GelMA/Nanoclay ink: (I) preparing GelMA/Nanoclay ink, (II) extruding filament based on the thixotropy property of nanoclay, and (III) printing structure based on the photo-crosslinking of GelMA. (B) Rheological properties of the GelMA/Nanoclay ink: (I) flow behavior of 4% nanoclay, 10% GelMA, 10/3% GelMA/Nanoclay, 10/4% GelMA/Nanoclay, and 10/6% GelMA/Nanoclay, (II) the viscosity-shear rate, and (III) the shear moduli-angular frequency of the respective biomaterial inks.
They also found that nanoclay at higher levels resulted in less expansion due to more shear stress, meaning that nanoclay with higher concentration needed greater yield stress for deformation. In further discussion, the authors states that greater balance needs to researched for printing with GelMA/Nanoclay, and that so far, they surmise that if ‘cell-laden structures’ are to be directly 3D printed, they are forced to give up shape fidelity. Along with that, greater control is required of the following:
- Mechanical strength
- Degradation rate
- Tissue regeneration capacity
“Through systematic experiments that included rheological testing, printability analysis, property characterization, and biocompatibility characterization, we have answered several fundamental questions relating to this ink, including the formation mechanism for shear-thinning and rapid-gelling and the printability window for the fabrication of complex GelMA scaffolds, as well as showing that the addition of nanoclay improved the basic properties and had no effect on the excellent biological performance of the scaffolds,” concluded the researchers.
“Therefore, this method provides an easy way to fabricate complex GelMA-based scaffolds with good shape fidelity. It is very likely that this method will have versatile applications in the individualized therapy of tissue defects.”

Printability analysis of GelMA/Nanoclay ink with regard to the extrusion process. (A) Schematic illustration of the expansion phenomenon and definition α = D/d.(B) Effect of the nozzle diameter on (I) the extruded filament diameter, and (II) α. (C) Effect of the flow rate on (I) the extruded filament diameter, and (II) α.
The world of tissue engineering and bioprinting is rich in a variety of scaffolds, and while here we have learned more about the use of GelMA-based scaffolds, researchers around the world are constantly experimenting with new ways to sustain cells and make inks that are cell-laden. We have followed studies regarding transparent bioinks for fabricating corneas, making neural tissue, and 3D printing complex structures like alginate/gelatin hydrogels. What do you think of this news? Let us know your thoughts! Join the discussion of this and other 3D printing topics at 3DPrintBoard.com.
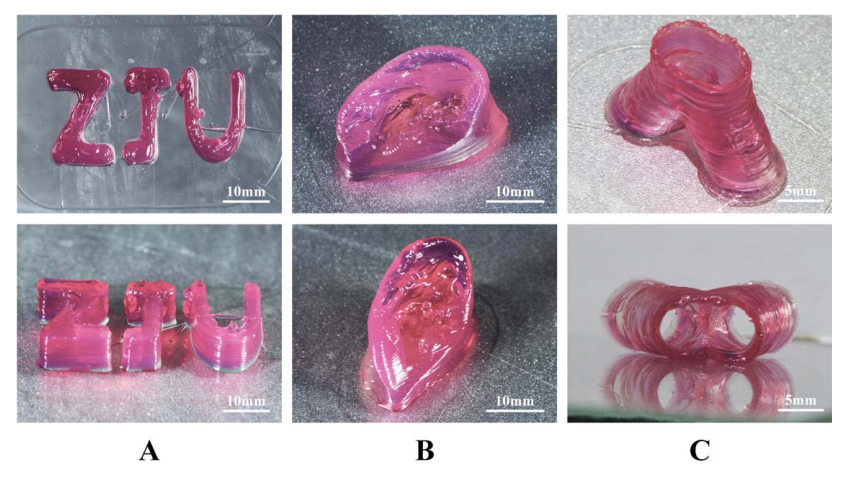
Photograph of the printed scaffolds with various shapes. (A) Abbreviation of Zhejiang University. (B) A bionic ear. (C) A branched vessel.
Subscribe to Our Email Newsletter
Stay up-to-date on all the latest news from the 3D printing industry and receive information and offers from third party vendors.
Print Services
Upload your 3D Models and get them printed quickly and efficiently.
You May Also Like
U.S. Navy Lab Uses 3D Printing to Reduce Tooling Lead Time By Over 90%
The F-35 Lightning II Joint Program Office (JPO), responsible for life-cycle management of the key fifth-generation joint strike fighter (JSF) system used by the U.S., its allies, and its partners,...
Etsy Design Rule Change Reduces Selection of 3D Printed Goods
Online marketplace Etsy has implemented a rule change requiring all 3D printed goods on the site to be original designs. The update to the site’s Creativity Standards states, ¨Items produced using...
Honeywell Qualifies 6K Additive’s Nickel 718 for 3D Printed Aerospace & Defense Parts
6K Additive is renowned for manufacturing sustainable additive manufacturing (AM) powder, and offers a wide portfolio of premium metal and alloy powders that include titanium, copper, stainless steel, and nickel,...
MetalWorm Sells WAAM Systems to Research Institutes in Brazil and Malaysia
Turkish WAAM firm MetalWorm has sold a system in Malaysia and another in Brazil. This is an excellent example of a few emerging trends in additive. Firstly, WAAM was experimented...