Although Japan is famous for their creations in origami, the craft is appreciated around the world, and recently by TU Delft researchers in the Netherlands who sought to understand more about folding mechanisms for complex efficient structures. Their findings are fully outlined in ‘Hyperbolic origami-inspired folding of triply periodic minimal surface structures,’ by Sebastien J.P. Callens, Nazlı Tümer, and Amir A. Zadpoor.
The Dutch researchers point out at the beginning of their study that geometries from triply periodic minimal surfaces—those that locally minimize an area, with vanishing mean curvatures present—have received a great amount of attention lately due to their potential for:
- High yield stress
- Low elastic modulus
- High fatigue resistance
- Bone-mimicking transport properties
And while TPMS structures are found to be ‘ideal for bone substitutes,’ the researchers explain that they are also suitable for creating a variety of structures that may be photonic, architected, or porous. They see obstacles in creating cellular structures, however, that can only be 3D printed in the form of lattices and are ‘incompatible with the planar functionality-inducing processes.’ As a result, the point of their research is to reduce constraints, while encouraging folding mechanisms, and innovating with new structures via sheet stretching. The authors also tweak the title of this new form of production from origami to origomu, since they are folding rubber instead of paper sheets—with ‘gomu’ meaning rubber.
Minimal material programming is required, and complex porous structures can be created this novel folding method:
“The rationale behind our approach consists of realizing curved minimal surface patches from a flat state, by combining rigid foldable frames with pre-strained elastomer sheets. Multiple of these foldable patches could then be connected together in a net and used as building blocks to fold a myriad of 3D TPMS-based architectures, ranging from single unit cells to larger assemblies consisting of multiple unit cells and 3D stackable minimal surface layers,” state the authors.
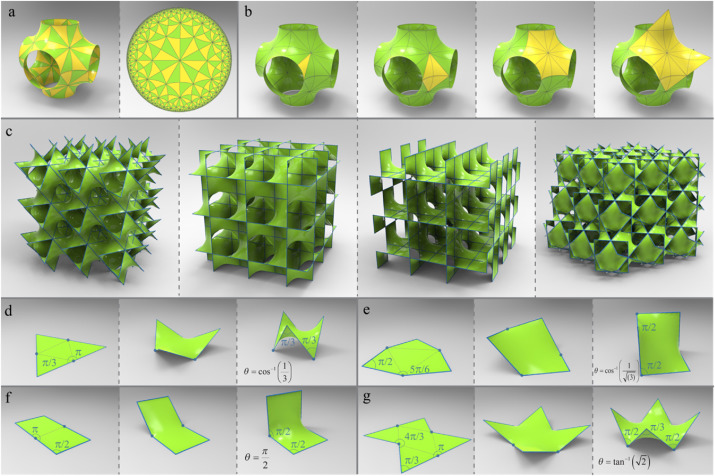
Geometry of TPMS and patch folding. (a) A translational P unit cell decorated with the hyperbolic *246 tiling of the fundamental asymmetrical patch. (b) Alternative patches to tile the P surface, shown together with the conventional unit cell. (c) The four TPMS considered here. From left to right: P, D, CLP, and C(P) surface. (d) Folding kinematics for the straight-edged skew polygonal patches of the P, D, CLP, and C(P) surfaces, respectively.
The concept of creating a TPMS structure in a saddle-shaped 3D puzzle form is the focus of the research, with their work using surfaces tiled by ‘straight-edged skew polygonal patches (homeomorphic to a disk).’
“A necessary (but not sufficient) condition therefore is the existence of embedded straight lines in the TPMS, which are axes of two-fold rotation and form the “linear skeletal net” of the surface,” state the researchers.
Polygonal patches are flattened with hinges attaches to boundary frame vertices, with edge lengths constant. This type of engineering allows for continuous folding of the frame to a flat polygon.

Connecting patches. (a) The edge-connection of two P patches. (b) The vertex-connection of two D patches. A transparent patch indicates a patch that fits in between two vertex-connected patches. (c) When trying to conform the hyperbolic (6,4) tiling of the D surface to the flat plane, one frequently encounters overlaps in the 2D net. (d–g) The folding of TPMS unit cells consisting of vertex-connected patches.
The patches can be connected to form more substantial minimal surfaces, resulting in a foldable 2D net, which then results in a 3D portion of the TPMS. Taking that one step further, the nets can continue to be connected, making even larger assemblies. Frames were 3D printed on an Ultimaker 2+ FDM printer, using PLA, with a 0.25 mm diameter nozzle and a layer thickness of 0.6 mm.
“We physically realized our self-folding minimal surface structures by attaching stretched elastomer sheets to 3D printed foldable frames,” said the researchers. “Upon release, the strain energy in the sheets causes the flat polygonal frame to self-fold into the desired skew polygonal configuration, and the sheet spanning the frame adopts an energy-minimizing saddle-shaped geometry, approximating the minimal surface.”
For this study, the authors narrowed their focus to four different TPMS types, but other minimal surfaces could be constructed if desired; in fact, they predict that a variety of different morphologies could be created.
“In this work, we focused on sheet-based structures, but beam-based lattices derived from the boundary frames could also be folded,” concluded the researchers. “Finally, our approach is not strictly bound by a specific length scale, meaning that it could also inspire the self-folding of architectural-scale tensile structures, nor is it limited to specific constituent materials, as long as a sufficient area distortion of the sheet surfaces and the rigidity of the boundary frames can be obtained.”
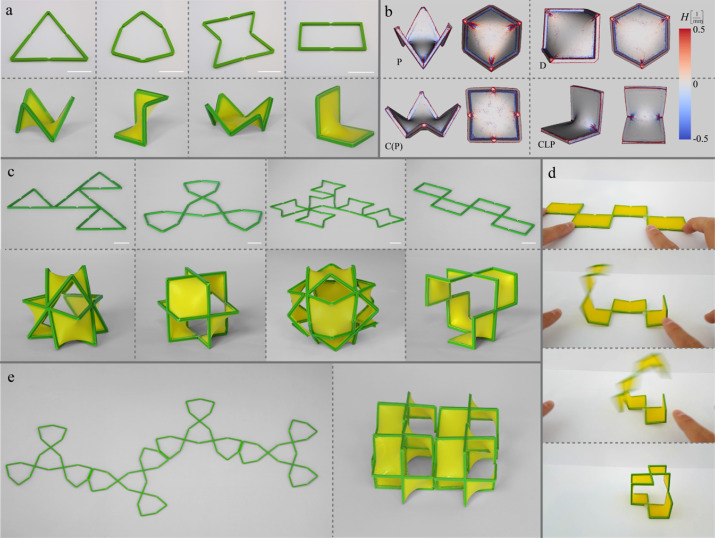
Self-folded physical models. (a) 3D-printed foldable frames for the four patch types in flat (top row) and folded (bottom row) configurations after the stretched latex sheets have been attached. (b) The mean curvature estimated using the 3D reconstructions of the four patch types obtained from micro-computed tomography data. (c) 3D-printed foldable TPMS unit cells in the flat (top row) and folded (bottom row) configurations. (d) The self-folding of the CLP unit cell through the pre-tension present in the latex sheet. (e) An assembly of four D unit cells in the flat (left) and folded (right) configurations. All scale bars are 20 mm.
Origami is an Asian craft so ancient that no one is sure whether it began in China or Japan, but Japanese artists have certainly made it their own over time. And because so many creative and scientific endeavors revolve around the creation of complex geometries and structures, origami has been an ongoing inspiration. In 3D printing, designers have also been inspired by the folding paper shapes to create complex structures for surgical implants, soft robotics, and even 4D printing to fabricate stronger metamaterials. Find out more about how origami is improving triply periodic minimal surface structures here.
What do you think of this news? Let us know your thoughts; join the discussion of this and other 3D printing topics at 3DPrintBoard.com.
[Source / Images: Hyperbolic origami-inspired folding of triply periodic minimal surface structures]
Subscribe to Our Email Newsletter
Stay up-to-date on all the latest news from the 3D printing industry and receive information and offers from third party vendors.
Print Services
Upload your 3D Models and get them printed quickly and efficiently.
You May Also Like
Consolidation in AM: How 2025 Is Shaping the Industry’s New Normal
The first half of 2025 has been marked by a clear shift in the additive manufacturing (AM) industry. Companies are no longer just focused on developing new tech by themselves....
Etsy Design Rule Change Reduces Selection of 3D Printed Goods
Online marketplace Etsy has implemented a rule change requiring all 3D printed goods on the site to be original designs. The update to the site’s Creativity Standards states, ¨Items produced using...
U.S. Congress Calls Out 3D Printing in Proposal for Commercial Reserve Manufacturing Network
Last week, the U.S. House of Representatives’ Appropriations Committee moved the FY 2026 defense bill forward to the House floor. Included in the legislation is a $131 million proposal for...
Transforming From Tourist to Native: Duro CEO Michael Corr Explains Why the Company Rebuilt its PLM Software on AI
In these early innings of the AI boom, many market analysts have expressed concern that AI spend has gotten too far ahead of the technology’s proven ability to deliver significant...