In a new study, Korean medical researchers have been looking into the differences in quality and accuracy of several different modern ways to make dentures, with a focus on whether there is really any significant difference between any of the techniques. The key in producing dentures is in creating a snug fit between the base and the patient’s mucosal tissue, with both deformation and shrinkage being a concern because they can affect nearly every aspect of the wearer’s experience.
It’s no secret that no matter how good dentures are, challenges remain for everyone, whether they are the technician producing them or the patient wearing them. And you may not have dentures, but most likely you have seen someone else struggling with them. Manufacturers are constantly trying to improve on areas of discomfort and ill fit, and in the last 20 years, digitalization has played a major role in improving on accuracy in production.
“When manufacturing a complete denture using digital workflow, the process begins with digital scanning of the edentulous arch, including challenging areas for the intraoral scanner device to scan, which are movable areas such as non-keratinized tissue and smooth surfaces covered with saliva,” state the authors.
Once the impression is digitized, the denture is created in CAD and then it can be milled, or a 3D printed prototype can be created. The base is the most critical area, and results are centered around accuracy—making this a topic of great research (and development) over the years, and one that the authors mention has been greatly insufficient in regarding 3D printed prototypes.
In this study, thirty different denture bases (ten for three groups) were examined. For the injection molding group, wax block was milled, based on the .stl file, with the base created via injection and PMMA resin. The milling group bases were made on a five-axis milling machine, and the rapid prototyping group of dentures were made on a DLP Bio3D 3D printer, cleaned in isopropyl alcohol for five minutes and then hydrated for 24 hours.
“There was no significant difference in the overall deformation in the horizontal direction among the three methods through comparison of distances between the 4 notches of the ridge,” concluded the researchers. “Comparison of fit accuracy between the cast and the maxillary complete denture base was evaluated on the 2nd upper premolar and the 2nd upper molar crossing the midpalatal suture, showing relatively high deformation in the conventional method due to polymerization shrinkage and the internal stress.
“The mean value of discrepancies was the lowest in the RP method, followed by that in the milling method and the injection molding method. The injection molding method had significantly lower fit accuracy than the other two CAD/CAM methods at two points. The degree of resolution was evaluated by measuring the vertical distance between the highest point and the lowest point in the palatine rugae area because of the complexity of the architecture. The injection molding method had significantly higher resolution than the milling method and the RP method.”
If you are just learning about 3D printing, you will probably be surprised to find out what a role it has played in the world of dentistry and orthodontics, and reconstruction in both areas. If you are well apprised of the miracles of 3D printing, you are probably still shaking your head in wonder over how it has taken off in the dental market, especially allowing for a variety of different dentures and molds to be made, along with new and improved 3D printers coming to market regularly.
What do you think of this news? Let us know your thoughts! Join the discussion of this and other 3D printing topics at 3DPrintBoard.com.
[Source / Images: ‘Comparing accuracy of denture bases fabricated by injection molding, CAD/CAM milling, and rapid prototyping method’]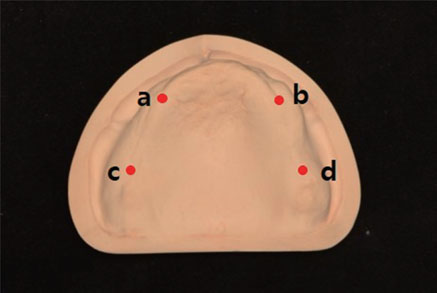
Points crossing the anterior alveolar ridge and posterior alveolar ridges (right: a, left: b) and points on posterior alveolar ridge from 15 mm distance parallel to the midpalatal suture from right and left hamular notches (right: c, left: d).
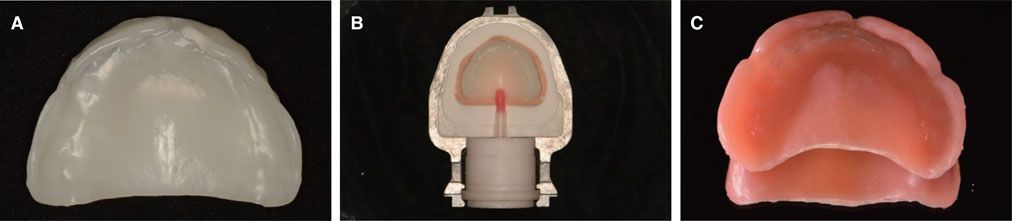
Injection molding method process. (A) Denture base fabricated from wax block by milling, (B) Investment of denture base, (C) Fabricated denture base.
Subscribe to Our Email Newsletter
Stay up-to-date on all the latest news from the 3D printing industry and receive information and offers from third party vendors.
Print Services
Upload your 3D Models and get them printed quickly and efficiently.
You May Also Like
Making Space: Stratasys Global Director of Aerospace & Defense Conrad Smith Discusses the Space Supply Chain Council
Of all the many verticals that have been significant additive manufacturing (AM) adopters, few have been more deeply influenced by the incorporation of AM into their workflows than the space...
EOS in India: AM’s Rising Star
EOS is doubling down on India. With a growing base of aerospace startups, new government policies, and a massive engineering workforce, India is quickly becoming one of the most important...
PostProcess CEO on Why the “Dirty Little Secret” of 3D Printing Can’t Be Ignored Anymore
If you’ve ever peeked behind the scenes of a 3D printing lab, you might have caught a glimpse of the post-processing room; maybe it’s messy, maybe hidden behind a mysterious...
Stratasys & Automation Intelligence Open North American Tooling Center in Flint
Stratasys has opened the North American Stratasys Tooling Center (NASTC) in Flint, Michigan, together with automation integrator and software firm Automation Intelligence. Stratasys wants the new center to help reduce...