Carbon has been making progress rolling out its 3D printers worldwide. The company has new directors, expanded its partnership with Ford and boldly reduced the prices on its resins. The company now takes a new step with the release of its L1 3D printer. The L1 has ten times the build volume of the M1 printer and five times the build volume of an M2 and is meant to be a manufacturing device. Interestingly the company says that “Products need to be validated by Carbon in the design phase in order to be printed on an L1 to ensure quality.” For certain industries not being able to validate their own designs could be a limitation. We reached out to the company for comment and they responded to tell us that,
“Validation is comprehensive and addresses all parts going into production. For adidas, that means different sizes and left and right models of the same shoe. For Riddell, every helmet is custom designed, so a broad array of designs are validated. For other applications, validation of one part could be sufficient to validate a closely related family of parts. Validation is an integral part of designing each Carbon Solution and is included in pricing the solution.”
Carbon’s power washing tools and the integrated software that comes with the system can be used in conjunction. Carbon’s materials will also be available. The solution comes replete with QA tools and monitoring to assure that you can control your production. Carbon’s products are developed in lockstep with each other and this level of tight integration means a tightly controlled ecosystem and should entail better ease of use. Carbon has always done this kind of thing in a very Apple-like way. This does mean that firms can go from a standstill to volume quickly but once we start targeting hundreds of thousands of parts wouldn’t companies want more control and more ability to use their own materials, settings, and procedures?
The company reports that:
“adidas and Carbon partnered to design and manufacture the adidas 4D midsole, and the L1 printer was one of the key innovations that made this possible. Together, we produced 100,000 pairs of the 4D midsoles in 2018. Our plan is to further scale the production of 4D shoes to millions in the coming years.”
If they pull off making millions of shoes then this indeed would be quite the coup for the technology. Only a few years ago I was very skeptical of Carbon being able to make 100,000 midsoles. I appear to stand corrected on that front, and with regards to Carbon apparently having made 100,000 midsoles for shoes that people are wearing today I congratulate them. I still am skeptical of Carbon being able to make shoe soles and midsoles that work in the real world, however. One firm that may make me partially more positive on this is Riddell. The American Football gear group is turning to Carbon to make helmet liners.
“Riddell and Carbon have partnered to be the first to bring customized, digitally printed helmet liners to market. Riddell’s SpeedFlex Precision Diamond is the first football helmet to have a digitally manufactured football helmet liner.”
The SpeedFlex Precision line is customized precision fit football helmet and indeed liners would seem to be a more doable application for the technology. It is precisely this kind of a combination of using 3D printing to develop mass customized higher functionality products that will deliver a lot of value for 3D printing in the future. Riddell itself has been working on custom made football helmets for a number of years now. By making a conventionally manufactured helmet and custom liners the company has a separation of concern which means that the process will not be costly and be relatively straightforward to implement. This paradigm is an excellent way of thinking about enabling mass customization for consumer goods.
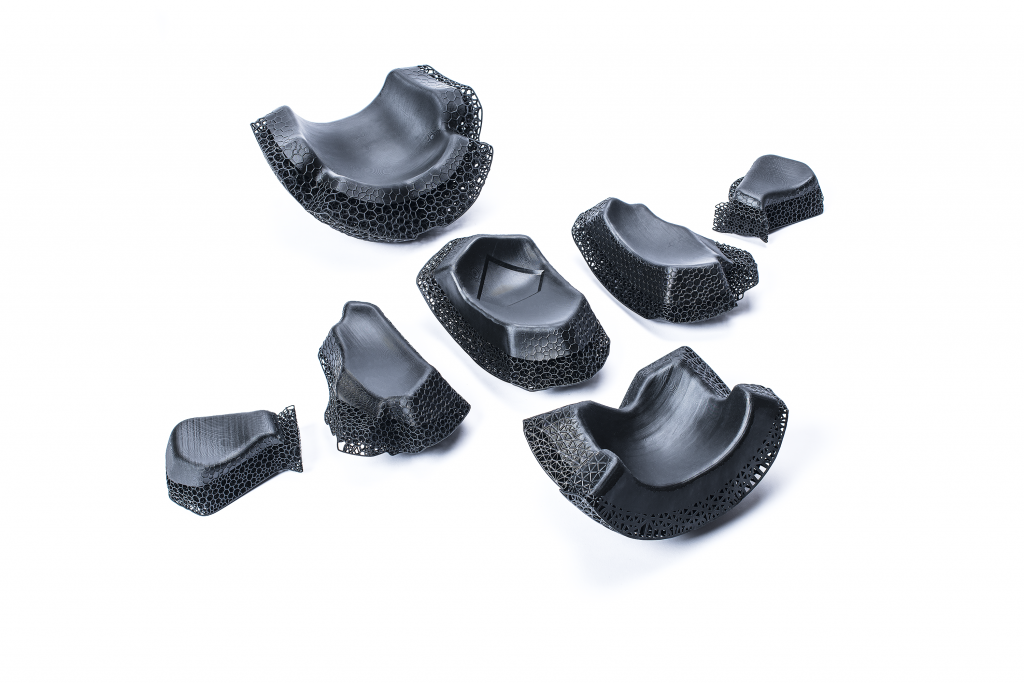
The seven custom 3D printed pads that make up the liner.
Carbon definitely seems to be making progress in delivering increased yield and throughput to customers. On the business development side, the company also seems to have laser-like focus in finding those clients on the cusp of significant mass customization initiatives and partnering with them. What do you think? Is my caution unwarranted and should I be more optimistic?
Subscribe to Our Email Newsletter
Stay up-to-date on all the latest news from the 3D printing industry and receive information and offers from third party vendors.
Print Services
Upload your 3D Models and get them printed quickly and efficiently.
You May Also Like
3D Printing News Briefs, July 2, 2025: Copper Alloys, Defense Manufacturing, & More
We’re starting off with metals in today’s 3D Printing News Briefs, as Farsoon has unveiled a large-scale AM solution for copper alloys, and Meltio used its wire-laser metal solution to...
3DPOD 260: John Hart on VulcanForms, MIT, Desktop Metal and More
John Hart is a Professor at MIT; he´s also the director of the Laboratory for Manufacturing and Productivity as well as the director of the Center for Advanced Production Technologies....
3D Printing News Briefs, June 28, 2025: Defense Accelerator, Surgical Models, & More
In this weekend’s 3D Printing News Briefs, 3YOURMIND was selected to join an EU Defense Accelerator, and PTC has announced model-based definition (MBD) capabilities within Onshape. Finally, a study out...
EOS in India: AM’s Rising Star
EOS is doubling down on India. With a growing base of aerospace startups, new government policies, and a massive engineering workforce, India is quickly becoming one of the most important...