BASF Venture Capital along with Materialise and Genesis Park (the Houston based VC not the park that purportedly gives us evidence that Man and Dinosaurs coexisted) closed their $22.2 million investment in Essentium. The company stated that the “The funding round will be used to scale manufacturing, engineering, international distribution, sales and marketing operations to meet market demand for the recently introduced Essentium High Speed Extrusion (HSE) Platform” which it feels will have an impact on the “manufacturing workflow of automotive, aerospace, contract manufacturing and biomedical industries.” Previously the three firms already partnered together.
Sven Thate of BASF Venture Capital stated that,
“Unleashing and accelerating the potential of additive manufacturing for our customers is a priority for BASF. Our investment, together with the strategic market partnership BASF has with Essentium, advances this strategy.”
Blake Teipel, the CEO of Essentium said that,
“Industrial additive manufacturing is ripe for transformation. The problem/solution paradigm is made clear through independent research we commissioned among executives in industrial manufacturing where 100% of respondents reported obstacles in using 3D printing for large scale production, and 88% stated that their industries’ will save billions of dollars in production costs when the barriers are eliminated. Eliminating these barriers is what Essentium is delivering on.”
What is Essentium?
Delivering on paper one imagines. Essentium is a Texas-based (Pflugerville again, is it something in the water?) materials and 3D printer OEM that aims to make 3D printers and materials for manufacturing. Their offering is very timely and seems to tick all of the right boxes. They state that their machines are ten times faster than current generation machines. Their HSE 180 S Platform will be a 740 x 510 x 650mm printer with a 600°C nozzle temperature with closed-loop temperature control and a 110°C, “fully-enclosed, multi-modal heated chamber” and a “200°C heating temp; multi-surface heated bed.” The motion stages are all linear and the printers claimed movement speed is 1m per second.
The printer costs $75,000 and if it has that temperature performance it could print high-performance materials such as PPA’s, Ultem, PEKK, PEEK and similar materials. The company wants to appeal to manufacturing and are making materials together with BASF.
What does Essentium have going for it?
Any high-temperature industrial machine with high speed is going to be an exciting proposition at this moment for aerospace and automotive companies. In closing the Octagon the company has the vision of making materials and the machine right simultaneously which would seem to be a good approach. In partnering with Materialise which has decades of experience in manufacturing they could get a lot of really expert feedback in using 3D printing for end-use parts. Materialise’s deep software expertise could also be a real boon to the firm. They could also get in contact with use cases and customers in 3D printing to get their feedback through them. With BASF on board, they have a tonne of polymer expertise as well as real heft with industrial firms.
Essentium also has Flash Fuse technology. In Fused Deposition Modeling (FDM, FFF and Material Extrusion) one of the problems is that you build up the object layer by layer. So in the X and Y plane you lay down nice melty gloopy plastic and then you go up a layer and do it again. Then you wait for those two layers to settle in gently and harden. Obviously, in between these layers, you will have issues with layer adhesion and because of this with your overall part strength. If pulled apart your part will tend to come apart where the layers are supposed to be fused. FDM 3D printed parts are therefore anisotropic because of this: eg are stronger in one particular direction. This is opposed to parts being isotropic, or as strong in all directions. Engineers always are oohing and aaahing about isotropy in 3D printing and say its preferable and then they go on and build cars with bumpers only on some sides. Generally, they love it when you make parts more isotropic.
Many firms have tried to get better layer adhesion in FDM and improve interlayer (and intralayer) bonding through additives or changing the cooling and heating process. Essentium’s Flash Fuse technology combines regular FDM with plasma welding in a totally brilliant way.
“The 3D printing process includes the steps of extruding a thermoplastic composite with the extrusion nozzle in successive layers to form a 3D part; directing a substantially evenly distributed plasma onto a predetermined location on the 3D part, and emitting an electromagnetic energy through the plasma. The plasma conducts the electromagnetic energy to the predetermined location on the 3D part. The thermoplastic composite includes a conductive material that generates heat by reacting to the electromagnetic energy.”
This sounds a lot like making a kind of a Plasma Transferred Arc Weld Deposition FDM hybrid or indeed sounds similar to the 2003 3D printing technology Microplasma Powder Deposition. The precise control could let them fuse layers in a much more fundamental way than just simply placing them ontop of one another could. Essentium maintains that with this “you are now able to fuse the individual layers in the printed part together inside the printer as the parts are being built. No postprocessing. This technology is scalable and can be applied to any type of thermoplastic.” These parts could then be much stronger in their Z direction than other parts printed on FDM systems.
If Essentium’s claims hold out in production systems then they may have found a way for manufacturing companies to make very strong and potentially very smooth (and perhaps annealed?) 3D printed parts straight on the machine. Very little data is available on Essentium’s systems and how they actually hold up in manufacturing environments. In every case we should be careful when assessing a company by its own promises. Part of the effort here at 3DPrint.com is to bring some much-needed realism and analysis to the Cheer squad that is 3D printing blogging so please don’t hate us when we repeat that claims of a company making true manufacturing materials on a true manufacturing machine can only be verified if independent people have access to materials and output of those machines and know what real life yield and part performance is like.
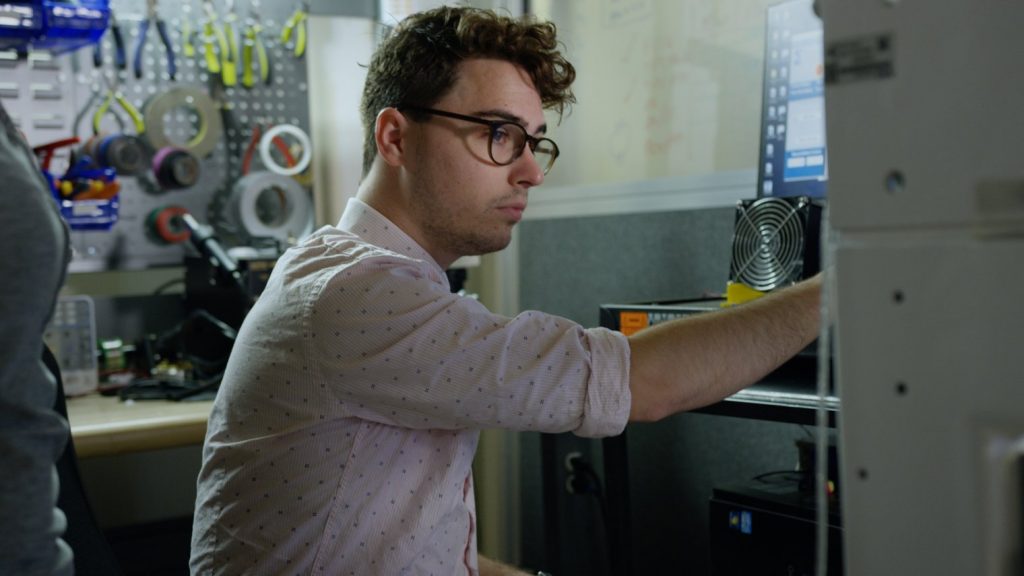
I should have moved to Greenpoint thinks the only hipster in Pflugerville.
Tonnes of 3D printing ideas are good but as we move into manufacturing the battle will be won and lost not in the press release but on the factory floor. So it will take quite some time for these claims to percolate back to us as beliefs held by people we know and trust.
Compared to many other FDM companies, however, Essentium seems to have tangible core advantages in the focus on materials and machine as well as the strong partners and cash that they have. They’re definitely a contender for true FDM manufacturing systems if indeed they work. If Flash Fuse were to work then it may be a significant leap for them and our industry.
What are the threats and limitations to them?
FDM is a very competitive field with hundreds of competitors. Many are trying to build a machine much like the Essentium but lacking the special sauce of Flash Fuse. Their technology is patented but could one achieve the same results with another welding process?
Could targetted cooling also get one very similar results at much lower cost?
Will their BASF partnership mean that other materials companies will shy away from the platform? Will, that deter industrial adoption?
Will this actually work in a production setting?
What is the surface quality of parts like? How dimensionally accurate are parts? It would seem that warping be less of an issue but are there any residual effects of their Flash Fuse process? Apart from this, how good is this as an FDM platform?
Sure their platform can bring the heat and indeed heat and cool quickly and higher yield sounds great but what are scrap rates?
Just improving better layer adhesion is only one feature, simultaneously the firm will have to ensure machine reliability and repeatability while having parts perform. Printer making can be kind of a unicycle while you’re juggling kind of challenge and apart from a cool technology and the right idea the company will have to get a whole host of other things right.
What is the value proposition actually? Where does this system’s performance lie when compared to existing technologies? It seems good but for what sized part at what cost would I use this over existing FDM or SLS?
How open is this system and how easy is it to introduce new polymers and new blends to it? Do all plastics work as they contend? Or must they all be blended or added to? If so what does that do to qualification and real-world performance of parts?
The company has not yet released a machine widely and indeed this is their first. 3D printers are very complex beasts because there is so much interplay between materials, environment, mechanical engineering, software etc. All 3D printers have teething problems and some are lemons. To what extent this will plague Essentium going forward is not known.
Conclusion
On the whole, this is still a giant leap for the Texan contender in FDM for manufacturing. With good partners and a good focus, the company could really make the leap into manufacturing. But, the truth will be determined on concrete floors by people with clipboards in the coming years. What do you think?
Subscribe to Our Email Newsletter
Stay up-to-date on all the latest news from the 3D printing industry and receive information and offers from third party vendors.
Print Services
Upload your 3D Models and get them printed quickly and efficiently.
You May Also Like
The Dental Additive Manufacturing Market Could Nearly Double by 2033, According to AM Research
According to an AM Research report from 2024, the medical device industry, specifically in dentistry, prosthetics, and audiology, is expected to see significant growth as these segments continue to benefit from...
Heating Up: 3D Systems’ Scott Green Discusses 3D Printing’s Potential in the Data Center Industry
The relentless rise of NVIDIA, the steadily increasing pledges of major private and public investments in national infrastructure projects around the world, and the general cultural obsession with AI have...
AM Research Webinar Explores Continuum’s Sustainable Metal Additive Manufacturing Powders
Metal additive manufacturing (AM) powder supplier Continuum Powders is working to develop solutions that empower industries to reduce waste and optimize their resources. An independent life cycle assessment (LCA) of...
3D Printed Footwear Startup Koobz Lands $7.2M in Seed Round
California-based Koobz is focused on reshoring the U.S. footwear supply chain with advanced manufacturing processes, including 3D printing. The startup just announced that it has added $6 million to its...