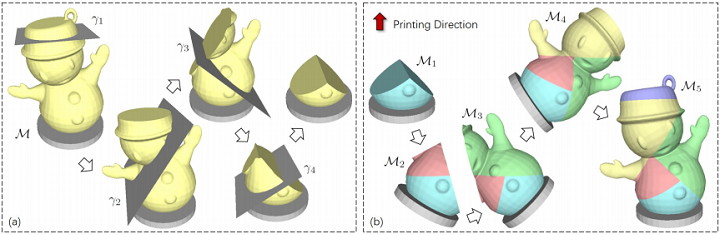
An illustration for the idea of the algorithm: (a) a progressively determined planar clipping results for generating the optimized base planes, and (b) the inverse order of clipping planes results in a sequence of regions to be fabricated where the printing direction of each region is the normal of its base plane. The orientation of a printing head is fixed during the procedure of physical fabrication. The parts under fabrication are reoriented to realize the multidirectional 3D printing.
In most planar-layer based 3D printing systems, material collapse is prevented on large overhangs by adding support structures to the bottom. But support structures in single-material 3D printing methods have some major issues, like material waste and the possibility of surface damage. This can be helped by introducing rotation and turning the hardware into a multidirectional system, where models are subdivided into separate regions and each one is 3D printed along a different direction.
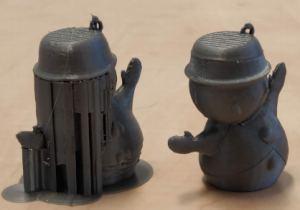
L-R: Snowman models fabricated by an FDM 3D printer and the team’s multidirectional 3D printing system by adding only one rotational axis on the same 3D printer.
A team of researchers from Tsinghua University, TU Delft, and the Chinese University of Hong Kong developed two types of multidirectional 3D printing hardware systems: one modified from an off-the-shelf FDM 3D printer with an added rotational degree-of-freedom (DOF), and the other implemented on an industrial robotic arm to simulate a tilting table for two rotational DOFs. They outlined their work in a paper titled “General Support-Effective Decomposition for Multi-Directional 3D Printing.”
The abstract reads, “We present a method to fabricate general models by multi-directional 3D printing systems, in which different regions of a model are printed along different directions. The core of our method is a support-effective volume decomposition algorithm that targets on minimizing the usage of support-structures for the regions with large overhang. Optimal volume decomposition represented by a sequence of clipping planes is determined by a beam-guided searching algorithm according to manufacturing constraints. Different from existing approaches that need manually assemble 3D printed components into a final model, regions decomposed by our algorithm can be automatically fabricated in a collision-free way on a multi-directional 3D printing system. Our approach is general and can be applied to models with loops and handles. For those models that cannot completely eliminate support for large overhang, an algorithm is developed to generate special supporting structures for multi-directional 3D printing. We developed two different hardware systems to physically verify the effectiveness of our method: a Cartesian-motion based system and an angular-motion based system. A variety of 3D models have been successfully fabricated on these systems.”
The researchers wanted to create a 3D printing system that would be able to “add rotational motion into the material accumulation process” to ensure fewer supports, if any. To do so, they created a general volume decomposition algorithm, which “can be generally applied to models with different shape and topology.”
“Moreover, a support generation algorithm has been developed for multidirectional 3D printing,” the researchers explained. “The techniques developed here can speedup the manufacturing of 3D printed freeform models by saving the time of producing and removing supports.”

Progressive results of fabricating models on 4DOF multidirectional 3D printing system and a 5DOF system realized on a robotic arm.
The research team’s paper made several technical contributions, including their support-effective algorithm, which is based on beam-guided search and can be applied to 3D models with handles and loops. In addition, they also summarized decomposition criteria through their multidirectional 3D printing process and created “a region-projection based method” for generating supports for multidirectional 3D printing.
There are, however, some drawbacks involved when changing from one 3D printing direction to another, such as slowing down the process, which is why the researchers “prefer a solution with less number of components, which can be achieve by considering the following criterion of clipping.”
“After relaxing the hard-constraint of support-free into minimizing the area of risky faces as described in JG, the scheme of generating support is considerately vital while both feasibility and reliability should be guaranteed,” the researchers wrote. “To tackle this problem, we propose a new pattern called projected supports that ensures the fabrication of remained overhanging regions through a collision-free multi-directional 3D printing.”
The team applied their algorithm to several models, and were able to reduce, and even eliminate in some cases, the need for support structures. In addition, their method’s “computational efficiency” was on par with general 3D printing time.
“We present a volume decomposition framework for the support-effective fabrication of general models by multidirectional 3D printing,” the researchers concluded. “A beam-guided search is conducted in our approach to avoid local optimum when computing decomposition. Different from prior work relying on a skeletal tree structure, our approach is general and can handle models with multiple loops and handles. Moreover, a support generation scheme has been developed in our framework to enable the fabrication of all models. Manufacturing constrains such as the number of rotational axes can be incorporated during the orientation sampling process. As a result, our algorithm supports both the 4DOF and the 5DOF systems. A variety of models have been tested on our approach as examples. Hareware setups have been developed to take the physical experiments for verifying the effectiveness of our system.”
Co-authors of the paper are Chenming Wu, Chengkai Dai, Guoxin Fang, Yong-Jin Liu, and Charlie C.L. Wang.
Discuss this research and other 3D printing topics at 3DPrintBoard.com or share your thoughts below.
Subscribe to Our Email Newsletter
Stay up-to-date on all the latest news from the 3D printing industry and receive information and offers from third party vendors.
Print Services
Upload your 3D Models and get them printed quickly and efficiently.
You May Also Like
Reinventing Reindustrialization: Why NAVWAR Project Manager Spencer Koroly Invented a Made-in-America 3D Printer
It has become virtually impossible to regularly follow additive manufacturing (AM) industry news and not stumble across the term “defense industrial base” (DIB), a concept encompassing all the many diverse...
Inside The Barnes Global Advisors’ Vision for a Stronger AM Ecosystem
As additive manufacturing (AM) continues to revolutionize the industrial landscape, Pittsburgh-based consultancy The Barnes Global Advisors (TBGA) is helping shape what that future looks like. As the largest independent AM...
Ruggedized: How USMC Innovation Officer Matt Pine Navigates 3D Printing in the Military
Disclaimer: Matt Pine’s views are not the views of the Department of Defense nor the U.S. Marine Corps Throughout this decade thus far, the military’s adoption of additive manufacturing (AM)...
U.S. Congress Calls Out 3D Printing in Proposal for Commercial Reserve Manufacturing Network
Last week, the U.S. House of Representatives’ Appropriations Committee moved the FY 2026 defense bill forward to the House floor. Included in the legislation is a $131 million proposal for...