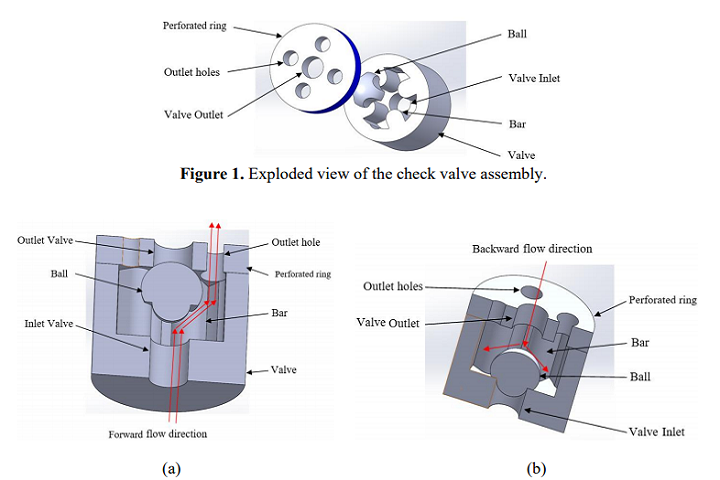
Cross sectional view of the assembly in the forward flow position (a) and backward flow
position (b), with the flow shown as red arrows.
Check valves are devices that allow for flow in one direction, while at the same time preventing flow in the opposite direction. The design of this device continues to improve as technology advances, and check valves have been made out of everything from graphene and hydrogels to shape memory alloys and piezoelectric materials. Micro check valves are self-controlled, relying on pressure changes for operation, and are often used in areas of biomedical engineering like drug delivery and surgical procedures, due to how cost effective and quick they are to fabricate.
A group of researchers from Alfred State College, one of eight Colleges of Technology within the State University of New York (SUNY) system, recently wrote a paper, titled “3D Printed Micro Check Valve for Biomedical Applications,” detailing how they used 3D printing and SOLIDWORKS modeling to develop a novel, imprinted micro check valve for a specific biomedical application: IV transfusions.
“This paper presents the design, fabrication and testing of a micro check valve used in I.V. fluid transfusion,” the researchers wrote. “The goal was to design a check valve that could be classified as a microsystem and be fully functional when being applied in an I.V. transfusion. The check valve has a free floating ball inside on tracks. When fluid is pushed through the valve, the ball will move to open the flow chamber, allowing fluid to pass. When the flow stops, the ball will slide down on the tracks to stop any backward flow.”
The initial design of the micro check valve used ball and socket parts, where the 2 mm ball would block the smaller channel from any backward flow and then settle into a perforated socket so fluid could pass. Then, the team added bars to hold the ball in the chamber and used a cap-like bottom to cover the smaller channel. Small tabs were added, which connected to these bars so the ball wouldn’t rotate.
“In order to improve the valve performance, a three part valve was designed and included a perforated ring, a containing ring with bars and a ball with grooves cut into it,” the researchers explained. “The ball still need to contain the capped bottom to allow for proper backward flow prevention, while the bars needed to remain to contain the ball. When fluid comes from the inlet of the valve, the ball will be pushed up into the perforated ring, allowing for fluid to freely flow around the ball through the small holes in the ring. Once the fluid stops flowing, the back pressure on the outlet of the valve will push the ball flush against the inlet of the valve, ensuring that no fluid will be able to flow backwards.”
The cap on the bottom makes a tight seal on the valve inlet, so backward flow is prevented. This design does not use a spring loaded ball, but rather relies on the laws of pressure flow to only initiate a one-way flow.
A Form 2 3D printer was used to make parts, modeled first in SOLIDWORKS, out of ABS. The three parts that made up the check valve – the ball, valve inlet, and perforated ring outlet – were all 3D printed at the same time. The completed valve was coated with a thin layer of parylene to make it safe for use inside the human body.
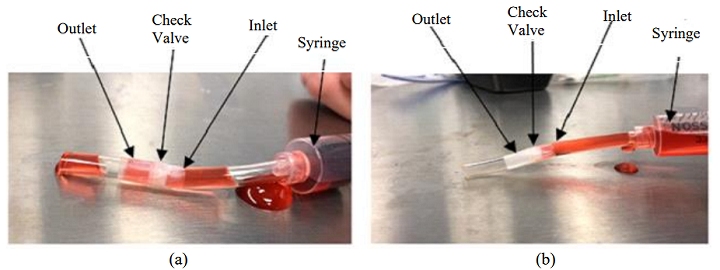
Experimental set up of the check valve, (a) forward flow (open direction) and (b) backward flow (closed direction).
The check valve was made in two sizes, with the larger one being used as a visual representation of what was happening inside the normal-sized valve, which was used for gathering data and test results. The team conducted multiple tests on the two check valves to prove that they would allow fluids to pass freely through, while also preventing any backward flow, including subjecting the 3D printed check valves to a certain pressure, as well as seeing if any liquid would freely flow through it without much pressure used.
“The tests showed that the check valve design allowed for zero backward flow while also allowing flow through the device in the proper direction at a rate of 98.6 μl/sec,” the researchers concluded.

Volume of colored water passing through the micro check valve over time in forward and backward flow directions; Flow rate in forward and backward flow directions of the micro check valve.
Co-authors of the paper are Abdou Mbaye, Colton Kreamer, Lukas Zink, Mitchell Fredenburg, and Reza Rashidi.
3D printing has been used multiple times to make valves for biomedical applications. Now, a micro check valve can be added to the list.
Discuss this and other 3D printing topics at 3DPrintBoard.com or share your thoughts below.
Subscribe to Our Email Newsletter
Stay up-to-date on all the latest news from the 3D printing industry and receive information and offers from third party vendors.
Print Services
Upload your 3D Models and get them printed quickly and efficiently.
You May Also Like
The Market and Industry Potential of Multi-Material 3D and 4D Printing in Additive Electronics
Additive manufacturing leverages computer-based software to create components for products by depositing either dielectric or conductive materials, layer by layer, into different geometric shapes. Since its birth in the 1980s,...
3DPOD 262: Bio-inspired Design for AM with Dhruv Bhate, Arizona State University
Dhruv Bhate is an associate professor at Arizona State University. There, he looks at structures, materials, and design. Previously, he worked at PADT as well as in the semiconductor and...
3DPOD 261: Tooling and Cooling for AM with Jason Murphy, NXC MFG
Jason Murphy´s NXC MFG (Next Chapter Manufacturing) is not a generalist service; instead, the company specializes in making tooling. Using LPBF and binder jet, the company produces some of the...
3DPOD 260: John Hart on VulcanForms, MIT, Desktop Metal and More
John Hart is a Professor at MIT; he´s also the director of the Laboratory for Manufacturing and Productivity as well as the director of the Center for Advanced Production Technologies....