Metallic glass, also known as amorphous metal, was first introduced in the early 1960s, and since then, it seems that everyone wants in on the action. The material is valued for its many exceptional properties, such as low stiffness, near-theoretical strength, high corrosion resistance, and large elastic strain limits. Bulk metallic glasses (BMG), which have characteristic specimen sizes in excess of 1 mm, have been explored successfully for for glass formers.
It’s not easy to produce metallic glasses with complex geometry, because the molten alloys must be cooled rapidly to move past the nucleation and growth of crystals, and most commonly used methods, such as melt spinning, casting, and powder metallurgy, are limited in both complex geometry and dimension. That’s why it’s so important to continue exploring and developing more novel processing routes for producing amorphous components.
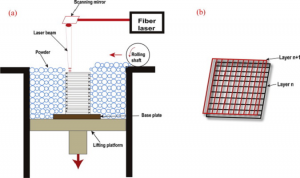
A schematic illustration of SLM-YZ250 3D printer: (a) operating mode of the device; (b) processing scanning pattern.
A team of researchers from the University of Science and Technology Beijing have been investigating the use of selective laser melting (SLM, also called DMLS, Direct Metal Laser Sintering, Powder Bed Fusion, Laser Powder Bed Fusion) 3D printing to fabricate Fe-based metallic glass powder with unrestricted, complex geometry. This specific technology offers very high cooling rates, which is important for glass formation of most BMGs, and can apply various processing parameters involving laser energy density to melt the metal powder.
The researchers recently published a paper, titled “Fabrication and characterization of Fe-based metallic glasses by Selective Laser Melting,” in the Optics and Laser Technology journal. The paper details SLM’s high potential for 3D printing metallic glass components with complex geometries.
The abstract reads, “Fe-based metallic glasses (MGs) can be potential structural materials owing to an exceptional combination of strength, corrosion and wear resistance properties. However, many traditional methods are difficult to fabricate Fe-based MGs with complex geometry. In this study, a new metallurgical processing technology, selective laser melting (SLM), was employed to fabricate Fe-Cr-Mo-W-Mn-C-Si-B metallic glasses. The microstructure, thermal stability and mechanical properties of the as-fabricate samples processing with different laser energy density have been investigated by X-Ray diffraction (XRD), scanning electron microscope (SEM), transmission electron microscopy (TEM), differential scanning calorimetry (DSC) and nano-hardness. Thanks to the high cooling rates of SLM, the crystalline phases in the gas-atomized powder almost completely disappeared and nearly fully amorphous structure parts were obtained after SLM processing. By choosing appropriate parameters, the size and quantity of the pores were reduced effectively and the relative density of the samples can reach values of over 96%. Although additional work is required to remove the residual porosity and avoid the formation of cracks during processing, the present results contribute to the development of Fe-based bulk metallic glasses parts with complex geometry via the SLM.”

(a) SEM secondary electron image of the gas-atomized powder; (b) SEM back-scattered image of the cross-section of the powder.
Fe-based BMGs are important for their unique combination of high physical, chemical, and mechanical properties, low affinity towards oxygen, and the fact that the raw material is less expensive than other commercial BMGs. So the researchers used a Fe-based metallic system Fe-Cr-Mn-Mo-W-B-C-Si with large glass forming ability (GFA) for the study, and used X-Ray diffraction (XRD), scanning electron microscope (SEM), transmission electron microscopy (TEM), and differential scanning calorimetry (DSC) to investigate structural variations between the original powder and the SLM 3D printer parts.
According to the powder’s morphology, the surfaces are very smooth, which results in good flowability. But, the team also observed that micro-pores were formed by trapped glass, and that crystallization did occur in a small amount of the powder, due to the fact that, as the researchers explained, “the cooling rate during gas atomization is not high enough to suppress crystallization.”
However, the crystalline phases in the gas-atomized powder disappeared after SLM 3D printing.
Samples were 3D printed with different laser energy densities, in order to investigate the metallic glasses’ mechanical properties and microstructural evolution. By choosing the appropriate parameters, the researchers were able to successfully 3D print high quality Fe-based metallic glasses.
“At present it is great challenge to produce large-scale glassy alloys in sophisticated geometries with the existing technologies. SLM technology, including heating the powder to melting in very short time and then the melting pool rapidly solidifying procedures, provides new opportunities for the creation of large, geometry freedom of metallic glass components,” the researchers explained. “From the results above, we noticed that although the as-received powder had partially crystallized, the powder experienced a quickly laser processing procedure with high cooling rates, leading to nearly fully amorphous structure. This phenomenon proves that under optimized SLM processing conditions, the nucleation and crystallization are inhibited, and amorphous structure can be acquired.”
They also noted that to improve the quality of the SLM 3D printed parts by decreasing micro-cracks and pores, further fine-tuning of the processing parameters is necessary.
The researchers concluded, “In addition, the preparation process of the powder system still needs to be optimized, and ensuring a fully amorphous structure powders can be obtained which eliminates crystallization in the SLM parts. The present results confirm that additive manufacturing by SLM represents an alternative processing method for the preparation of bulk metallic glass components without limitations in size and intricacy. The processing method and conditions are in principle available for a large variety of metallic glasses production.”
Co-authors of the paper include X.D. Nong, X.L. Zhou, and Y.X. Ren with the university’s State Key Laboratory for Advanced Metals and Materials.
Discuss this story and other 3D printing topics at 3DPrintBoard.com or share your thoughts below.
Subscribe to Our Email Newsletter
Stay up-to-date on all the latest news from the 3D printing industry and receive information and offers from third party vendors.
Print Services
Upload your 3D Models and get them printed quickly and efficiently.
You May Also Like
The Dental Additive Manufacturing Market Could Nearly Double by 2033, According to AM Research
According to an AM Research report from 2024, the medical device industry, specifically in dentistry, prosthetics, and audiology, is expected to see significant growth as these segments continue to benefit from...
Heating Up: 3D Systems’ Scott Green Discusses 3D Printing’s Potential in the Data Center Industry
The relentless rise of NVIDIA, the steadily increasing pledges of major private and public investments in national infrastructure projects around the world, and the general cultural obsession with AI have...
AM Research Webinar Explores Continuum’s Sustainable Metal Additive Manufacturing Powders
Metal additive manufacturing (AM) powder supplier Continuum Powders is working to develop solutions that empower industries to reduce waste and optimize their resources. An independent life cycle assessment (LCA) of...
3D Printed Footwear Startup Koobz Lands $7.2M in Seed Round
California-based Koobz is focused on reshoring the U.S. footwear supply chain with advanced manufacturing processes, including 3D printing. The startup just announced that it has added $6 million to its...