Typically, metals are all composed of highly ordered, crystalline structures of atoms. While there are obvious uses and benefits of this type of atomic arrangement, there is a limit to how strong any metal is ultimately capable of being. However, an amorphous metal, or “metallic glass,” is a fully-solid metal material that has its atomic-scale structure completely disordered, similar to conventional glass. They are unlike the glass we typically use for our windows, but metallic glasses, thanks to their atomic structure, can be up to three times as strong as conventional metal alloys. They also offer electrical conductivity properties that far exceed those of traditional metal alloys. Until recently the only way to produce metallic glass was to rapidly cool metal before its solid-state crystalline structure could form, which meant that it was difficult to produce in large enough amounts to be widely adopted for industrial uses.
A Swedish startup named Exmet has partnered with materials company Heraeus Group on the development of a process to 3D print using amorphous metal components. The partnership is seeing success thanks to Heraeus’ expertise in the development of cutting edge manufacturing materials and Exmet’s 3D printing process knowledge and experience. With the addition of amorphous metal in a powder form to their extensive materials portfolio, Heraeus has now made available what is expected to be one of the most sought after group of 3D printing materials of the future. Virtually any metallic alloy can be produced as a metallic glass, each with a wide range of uses and potential applications that far exceed their traditional alloy forms. These metallic glass powders can be used in several powder-bed 3D printing systems.
“Amorphous metals will change our future. They possess a wide variety of previously incompatible characteristics: They are very strong and yet malleable, as well as harder and more corrosion-resistant than conventional metals. Together with Exmet, we intend to open up this new class of materials for industry and 3D printing. Particularly in additive manufacturing, it is crucial for the material and the manufacturing process to be perfectly matched in order to ensure the utmost consistency and quality,” head of 3D Printing at Heraeus New Businesses Tobias Caspari explained.
Amorphous metals are ideal next-generation materials for a large number of high-tech applications in multiple industries and markets. Objects made from an amorphous metal material are energy-absorbing and virtually scratch-proof, which lend themselves to everything from consumer electronics to nanoparticles to almost indestructible electronic components and even longer-lasting medical implants. Metallic glasses have a high resistance to water, making them essentially corrosion-proof, however they can be engineered to slowly dissolve inside the human body, making it an excellent material to 3D print bone scaffolds that will encourage new bone material to grow and replace the dissolving implant.
“For fifty years the commercial success of amorphous metals has been held back by inadequate manufacturing methods. Now that changes. Exmet looks forward to cooperating with Heraeus as a competent partner with a worldwide network to help bring this disruptive new technology to the market,” says Exmet co-founder and CEO Mattias Unosson.
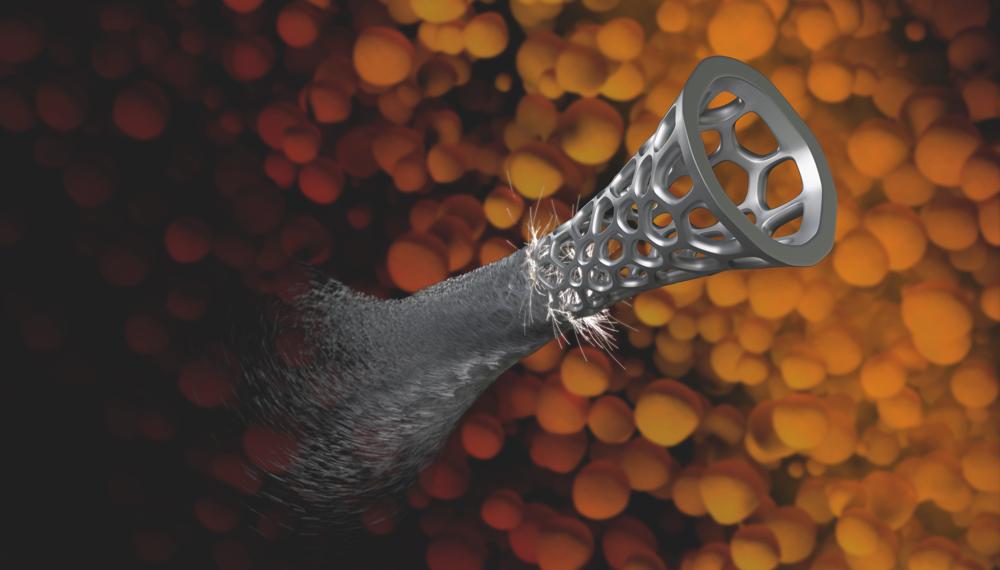
In partnership with Exmet, Swedish startup Heraeus has developed the 3D printing of amorphous components, thereby expanding its range for special materials. [Source: Heraeus]
Subscribe to Our Email Newsletter
Stay up-to-date on all the latest news from the 3D printing industry and receive information and offers from third party vendors.
Print Services
Upload your 3D Models and get them printed quickly and efficiently.
You May Also Like
Havaianas Collaborates with Zellerfeld to Launch 3D Printed Flip-Flops
The shoe of the summer is undoubtedly the flip-flop. Easy on, easy off, your feet won’t get sweaty because there’s not much material, and they’re available in a veritable rainbow...
UCLA Researchers Develop 3D Printed Pen that May Help Detect Parkinson’s Disease
Diagnosing Parkinson’s disease is difficult. Often, early symptoms of the progressive neurological condition may be overlooked, or mistaken for signs of aging. Early diagnosis can help save lives and improve...
Printing Money Episode 30: Q1 2025 Public 3D Printing Earnings Review with Troy Jensen, Cantor Fitzgerald
Printing Money is back with Episode 30, and it’s that quarterly time, so we are happy and thankful to welcome back Troy Jensen (Managing Director, Cantor Fitzgerald) to review the...
Heating Up: 3D Systems’ Scott Green Discusses 3D Printing’s Potential in the Data Center Industry
The relentless rise of NVIDIA, the steadily increasing pledges of major private and public investments in national infrastructure projects around the world, and the general cultural obsession with AI have...