We’re starting out with a little business in today’s 3D Printing News Briefs, then moving on to planes, automobiles, and camping, followed by some medical news. Renishaw just received a business award and EOS signed an agreement with Z3DFAB. UTC Aerospace Systems is increasing its use of 3D printing, and Volkswagen used the technology to set a new record in a race. Researchers from ETH Zurich developed a unique 3D printed camp stove that protects its flame from the elements. Finally, Renishaw’s 3D printing technology was used to help during a difficult cranial surgery, and NBC’s Megyn Kelly highlights the story of a former firefighter who designed and 3D printed his own prosthetic hand.
Renishaw Wins Business Award
Global metrology and engineering company Renishaw was recently named the Winner of Winners at the 30th annual PWC West of England Business Awards, taking the Business of the Year award while company Co-Founder and Executive Chairman Sir David McMurtry, who invented the company’s famous touch-trigger probe, was named the region’s top CEO, though he stepped down from the role in February. Renishaw first won this title back in 1996, but to celebrate the awards’ 30th anniversary, former winners were invited to re-enter this year, and were judged on criteria such as community, regional contributions, finance, human resources, innovation, and training. Renishaw, now a FTSE 250-listed company, has certainly grown in the last three decades, operating out of 35 countries with 95% of its annual sales derived from exports.
“Renishaw has gone from strength to strength as a result of investing for the long term in people and innovation. The company puts around 15 per cent of annual turnover back into research and development, fosters a culture of innovation and is passionate about treating employees well,” said Chris Pockett, Renishaw’s Head of Communications. “Renishaw is honoured to be named Winner of Winners at the 30th and final year of the awards.”
EOS Signs Agreement with Z3DFAB
Korean company Z3DFAB, the joint venture between French additive manufacturing expert Z3DLAB and HS HI-TECH, opened a digital production center this fall, using technology from EOS. Now, the two industrial 3D printing companies are partnering up again, and have signed an agreement to jointly build an additive manufacturing innovation center in Korea. Both EOS and Z3DFAB plan to develop and offer the range of advanced 3D printing solutions required by the country’s market, and will work to grow the market in Korea with several initiatives, including hosting workshops and seminars.
“China succeeded in developing the 3D printing market, and has become the largest 3D printing market in Asia thanks to its cooperation with service providers like Z3DFAB. The role of service provider is highly important to drive the market regardless of country, so we chose Z3DFAB as the most adequate player for this, as they already provided several industrial AM solutions,” said Jack Wu, Sales Director, EOS APAC. “EOS and Z3DFAB will collaborate to develop Korean market via various industrial AM solutions.”
Z3DFAB also announced that it has purchased its first M400-4, EOS’s biggest metal 3D printer, and will invest in several other industrial 3D printers to be installed in its factory.
UTC Aerospace Systems Increasing Its 3D Printing Usage
Two years ago, UTC Aerospace Systems opened a new 3D printing materials lab in Connecticut. Now, it’s increasing its 3D printing use even further, and has doubled its AM capacity in the last year – a fact that’s illustrated in the company’s new video.
“We’re feeling extra inventive! Why? We’re growing our additive design and manufacturing (ADaM) capabilities and unleashing innovation and unlocking productivity as a result,” read the video description.
The video gives a brief explanation of the 3D printing process, and shows how the company used the technology to fabricate a fuel nozzle with improved quality, a faster lead time, and just four parts – a major reduction of the 18 components that made up its legacy fuel injector.
Volkswagen Sets New Race Record with Electric Car and 3D Printed Components
Last month, German automobile manufacturer Volkswagen competed in the world’s most famous hill climb race – the Broadmoor Pikes Peak International Hill Climb (PPIHC) – with its first electric race car. The team engineered the aerodynamics of the car with 3D printed components in hopes of breaking the 8:57.118-minute record in the electric prototype class.
The automaker’s Motorsport works rally team 3D printed about 2,000 individual parts for its 1:2 scale model of the electric I.D. R Pikes Peak race car, some of which even ended up being used on the final car in the race – auxiliary components like switches and brackets for cables. But every single piece played an important part in helping driver Romain Dumas and the I.D. R Pikes Peak electric race car achieve the goal and set a new record of 7:57:148 minutes.
Dr. Benjamin Ahrenholz, Head of Calculations/Simulations at Volkswagen Motorsport, explained, “When we were in the wind tunnel with the 1:2 scale model of the I.D. R Pikes Peak, we gained a lot of time by using 3D printing.
“This way we did not have to suspend testing just because a certain part was not yet ready – for example, a cover for the batteries’ power electronics.”
3D Printed Camp Stove Developed in Zurich
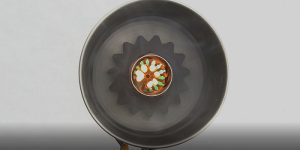
The burner is inside the cooking vessel (view from above). [Image: Peter Balicki Szczesiak, ETH Zurich]
Project Manager Julian Ferchow said in a translated quote, “Peakboil serves as a demonstration object, with which we can show companies what is possible with additive manufacturing technology and what one has to pay particular attention to when constructing.”
Renishaw’s Technology Used in Cranial Surgery
Bartolomé Oliver, MD, PhD, a neurosurgeon at the Teknon Medical Center in Barcelona, met a 68-year-old female patient with a benign growth on the left side of her cranium that was expanding into the skullbone. The growth was caused by a meningioma tumor, and a craniectomy was required to remove the growth, followed by a cranioplasty to rebuild the patient’s skull. Dr. Oliver decided to perform both operations in one procedure, and worked with top design consultancy and applied research center PDR, which partners with Renishaw for metal 3D printing.
PDR designed a cranial plate and custom surgical cutting guide from the patient’s CT scans, and Dr. Oliver shared the modifications he would need in a brief Skype session with PDR and Renishaw. The parts were 3D printed in titanium, with a satin finish, on a Renishaw AM250 metal 3D printer, and then treated with the company’s X-flex technology to ensure high ductility.
“Parts were delivered to us according to plan which allowed us to prepare them for the surgery,” said Dr. Oliver. “No adjustment was needed during surgery. Using the 3D-printed cutting guide and implant saved us approximately 30 per cent of the time required for this kind of surgery.”
The patient was discharged after only four days in the hospital, and post-op CT scans show good implant performance.
Former Firefighter 3D Prints Own Prosthetic Hand
Braden Leonard, who became a firefighter after 9/11, really enjoys outdoor sports like hiking and snowboarding. But after a freak mountain biking accident that involved a thorn in his hand, he contracted necrotizing fasciitis and had to have his right hand amputated while in a medically induced coma. Even though his days fighting fires were over, Leonard started looking into upper-limb prosthetic devices that would allow him to continue his outdoor sports. Not finding anything overly helpful, he realized that he would need to make his own prosthetic, and turned to 3D printing.
Leonard applied to the Autodesk BUILD Space in Boston, and used BigRep‘s 3D printers to fabricate new prosthetic devices, including one that lets him ride his motorcycle again. You can learn more about Leonard’s story, and his hope to fight fires again someday, here.
Discuss these stories and other 3D printing topics at 3DPrintBoard.com or share your thoughts in the Facebook comments below.
Subscribe to Our Email Newsletter
Stay up-to-date on all the latest news from the 3D printing industry and receive information and offers from third party vendors.
Print Services
Upload your 3D Models and get them printed quickly and efficiently.
You May Also Like
Reinventing Reindustrialization: Why NAVWAR Project Manager Spencer Koroly Invented a Made-in-America 3D Printer
It has become virtually impossible to regularly follow additive manufacturing (AM) industry news and not stumble across the term “defense industrial base” (DIB), a concept encompassing all the many diverse...
Inside The Barnes Global Advisors’ Vision for a Stronger AM Ecosystem
As additive manufacturing (AM) continues to revolutionize the industrial landscape, Pittsburgh-based consultancy The Barnes Global Advisors (TBGA) is helping shape what that future looks like. As the largest independent AM...
Ruggedized: How USMC Innovation Officer Matt Pine Navigates 3D Printing in the Military
Disclaimer: Matt Pine’s views are not the views of the Department of Defense nor the U.S. Marine Corps Throughout this decade thus far, the military’s adoption of additive manufacturing (AM)...
U.S. Congress Calls Out 3D Printing in Proposal for Commercial Reserve Manufacturing Network
Last week, the U.S. House of Representatives’ Appropriations Committee moved the FY 2026 defense bill forward to the House floor. Included in the legislation is a $131 million proposal for...