Last summer, researchers from the Fraunhofer Institute for Laser Technology ILT and the RWTH Aachen University developed a new 3D printing process that offers eco-friendly, economical corrosion and wear protection, without having to deal with any of the drawbacks associated with other methods like chrome plating, laser metal deposition (LMD), and thermal spraying. The Extreme High-Speed Laser Metal Deposition process, known by its German acronym of EHLA, is based on LMD, which can be used to repair turbine blades but is too slow to coat large components.
During the EHLA process, metal powder particles are melted directly in the laser beam, which increases the process speed from only a few meters per minute to 500 meters per minute; it also lowers layer thickness from over 500 down to a range of 10 to 250 microns. This means that EHLA can be used as a good coating alternative to typical, more problematic methods, and can also cost-effectively 3D print and repair components.
The team behind the patented EHLA process received the Joseph von Fraunhofer Prize last year, and the Steel Innovation Prize this year, and now it’s been awarded a new accolade. Dr. Andres Gasser and Thomas Schopphoven of Fraunhofer ILT and Gerhard Backes, the Chair for Digital Additive Production DAP, RWTH Aachen University, have won the Berthold Leibinger Innovationspreis 2018 for the development of EHLA.Timing is everything – the team found out that it had been invited as a finalist to the jury session in Ditzingen by the private foundation Berthold Leibinger Stiftung on May 16th, which was the first International Day of Light. On July 13th, which just so happened to fall on a Friday, Schopphoven, representing the rest of the team, presented the EHLA process, competing against seven other finalist teams. The Innovationspreis has been awarded every other year since 2000 for outstanding research and development in the generation, or application, of laser light.

The finalists of the Berthold Leibinger Innovationspreis 2018 at the jury session on July 13th in Ditzingen.
Schopphoven, the Head of the Productivity and Systems Engineering team in the Laser Material Deposition Group at Fraunhofer ILT, said, “In the laser industry, this is one of the world’s top-class awards. We are extremely pleased about the recognition of our work on energy- and resource-efficient production with laser light.”
The international jury was so impressed by the team’s EHLA process that it decided to award the researchers with the prestigious prize. On September 21st at the Ditzingen headquarters of the TRUMPF Group, the Fraunhofer ILT and RWTH Aachen University team will receive the award, which is endowed with €50,000. Project group DELPHI took second place for its industrial application of femtosecond laser lithography in integrated optics, while third place was awarded to Prof. Jürgen Popp and Prof. Ute Neugebauer for their work in developing a laser-based method for rapid antibiotic resistance determination.
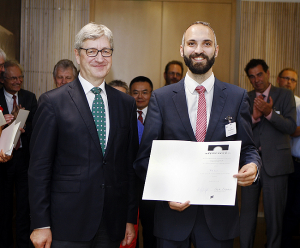
L-R: Juror Prof. Wolfgang Marquardt, Chairman of the Board of Directors of Forschungszentrum Jülich, and Thomas Schopphoven, Fraunhofer ILT, at the announcement of the Berthold Leibinger Innovationspreis 2018 winners.
The EHLA concept has already seen some commercial success – Dutch company IHC Vremac Cylinders B.V. has been using the process to coat its hydraulic cylinders, with diameters up to 500 mm and lengths up to 10 m, for offshore use around the world; these cylinders are also already coated with wear- and corrosion-resistant alloys. Fraunhofer ILT spin-off ACunity GmbH is circling China’s offshore market, and recently delivered three large EHLA systems to Hebei Jingye Additive Manufacturing Technology Co., Ltd., which will be used to coat offshore hydraulic cylinders.
But Schopphoven is certain that the offshore market is only the beginning, and believes that even more industry applications for the EHLA process will emerge.
“The EHLA process is particularly suitable for the automotive industry, such as for the coating of brake discs, which were previously difficult to coat because of the high loads and high demands on efficiency and environmental friendliness.”
Discuss this story and other 3D printing topics at 3DPrintBoard.com or share your thoughts in the comments below.
[Source: Fraunhofer ILT / Images: Berthold Leibinger Stiftung, unless otherwise noted]Subscribe to Our Email Newsletter
Stay up-to-date on all the latest news from the 3D printing industry and receive information and offers from third party vendors.
Print Services
Upload your 3D Models and get them printed quickly and efficiently.
You May Also Like
Metal Powder Supplier Elementum 3D Added to $46B Air Force Contract
Elementum 3D, a Colorado-based developer and supplier of metal powders used in additive manufacturing (AM), announced that the company has been added to the vendors list in the fourth on-ramp...
Ursa Major Lands $28.6M AFRL Deal for 3D Printed Draper Engine Flight Demo
The US Air Force Research Laboratory’s (AFRL’s) Rocket Propulsion Division at Edwards Air Force Base has awarded a $28.6 million contract to Ursa Major for follow-on work related to the...
3D Printing Financials: Rocket Lab’s Record-Breaking Year and Over 20 Launches Coming in 2025
Rocket Lab (Nasdaq: RKLB) closed 2024 with its best year yet. The company launched more rockets, signed more contracts, and expanded deeper into spacecraft and satellite production than ever before....
US Air Force Taps Beehive to Study 3D Printed Jet Engines
Propulsion 3D printing firm Beehive Industries secured a contract from the U.S. Air Force Life Cycle Management Center through SOSSEC. SOSSEC is a company that manages Other Transactions Authority (OTA)...