3D4Makers: Father-Son Team Tell Us About New Filament Extrusion Technology and Building a Business Spurred by Failed 3D Prints
More than a few 3D printing-related companies have arisen almost by accident. A maker has a problem with a particular aspect of 3D printing, comes up with a solution to solve it, and then realizes that they can market that solution, leading to often-successful businesses. That was the case with 3D4Makers, a Netherlands-based filament manufacturer started by Jan-Peter Wille and his son Jasper. Jan-Peter had been working with polymers for three decades, and Jasper was gaining experience with a range of 3D printers and 3D printing technologies. Like many makers, they found themselves frustrated with the filament they were using.
“We saw a lot of failed prints happen because the filament was failing,” Jasper Wille told 3DPrint.com. “Breaking in the filament, bubbling and problems with the diameter would cause a lot of parts to fail to 3D print. We set out to make good filament that eliminated these problems. We saw that to really make good 3D printing filament we would have to develop a completely new way to make filament.”
Many of the problems, they realized, could be chalked up to one thing: moisture. It’s a familiar and aggravating problem to anyone who 3D prints on a regular basis, particularly with PLA, a hydrophilic material that loves to soak up moisture from its environment, making for all sorts of issues during printing. Moisture also causes problems with most other filaments to varying degrees, and while many have developed solutions such as filament-drying machines and moisture-resistant storage, the Willes decided to attack the issue from the very beginning.
“Besides a lot of problems that were down to filament producers being sloppy there were issues that were tied to existing extrusion processes. These all used water to cool the filament,” Jasper explained. “Engineering plastics do not like water. Performance of the filament degrades. People in the 3D printing community have long struggled with moisture, especially in PLA and PA. We thought that if we made a completely new extrusion technology where the filament would not come into contact with water that we would eliminate these problems.”
The project would take two years. With the help of Servan Bakker, who had 13 years of experience building industrial extruders, the Willes developed a filament extruder that uses a multiple jet air cooling system to cool the filament without water. When they began printing with the filament, they noticed a significant decrease in failed prints as well as an increase in layer adhesion, leading to stronger, higher-quality parts. While the Willes had begun the project with the intention to simply make better filament for their own projects, they soon realized that they could market their materials. A family friend named Robert Becker invested in the idea and joined the team to help with the creation of a website, bringing another friend named Ardy Struijk to handle marketing and sales, and a business was born.
“What we also noticed is that we could get a roundness on the filament of 99%,” Jasper told us. “Poor filament roundness leads to a lot of misprints as well especially in bowden based 3D printers. We then started to make pure grades of filament with no additives such as plasticizers. This we can also do because of our unique extrusion line.”
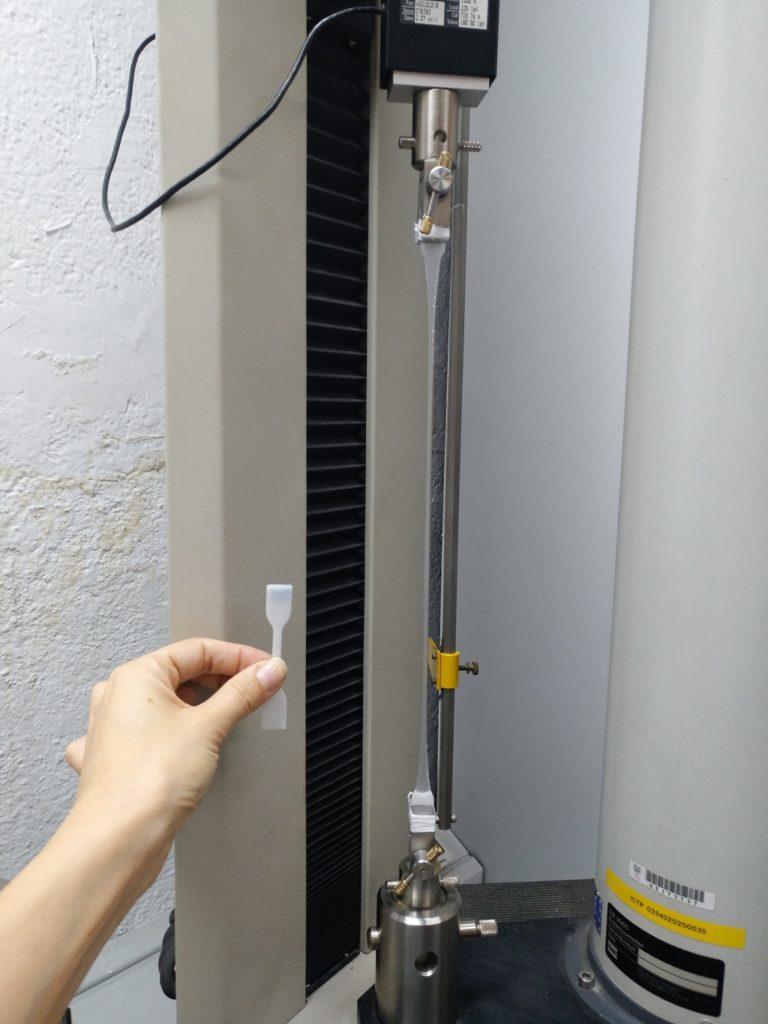
Nieves Cubo Mateo, R&D engineer for Exovite, conducts a tensile strength test on PCL 99. [Image: Nieves Cubo Mateo]
“These 100% pure filaments such as our one of a kind PLLA filament found a market with medical researchers using it for scaffolding material for bioprinting,” Jasper continued. “We then were able to develop unique low temperature filaments such as PCL 99 and PCL 100 that also found customers in Universities and research labs. With PCL we have a unique material that is very strong, biodegradable, nontoxic and that can be shaped post 3D print. A brace for example can be printed to size and then remelted to fit perfectly. Our PCL material is also used in combination with hydrogels and materials such as hydroxyapatite in bioprinting research.”
Additional filament offerings include ABS, ASA, PLA, PETG, and hemp PLA. Prices range from about €20 per 750g for ABS and PLA to nearly €480 for PEEK. 3D4Makers also offers custom labels for companies to offer their own personal filament brands.
“We love to support the 3D printing community and deliver high quality affordable filament to them,” Jasper told 3DPrint.com. “Mainly though our focus now in on bioprinting and medical filaments as well as engineering filaments for manufacturing such as our PPSU and PEI filaments. Increasingly we’re getting more industrial companies that are coming to us to have filaments made for a particular manufacturing application. All in all it has been a very exciting journey over these past years. We started by simply wanting good filament for ourselves and now we deliver to so many exciting partners worldwide. It’s amazing really.”
Discuss in the 3D4Makers forum at 3DPB.com.
[Images via 3D4Makers]
Subscribe to Our Email Newsletter
Stay up-to-date on all the latest news from the 3D printing industry and receive information and offers from third party vendors.
Print Services
Upload your 3D Models and get them printed quickly and efficiently.
You May Also Like
The Market and Industry Potential of Multi-Material 3D and 4D Printing in Additive Electronics
Additive manufacturing leverages computer-based software to create components for products by depositing either dielectric or conductive materials, layer by layer, into different geometric shapes. Since its birth in the 1980s,...
3DPOD 262: Bio-inspired Design for AM with Dhruv Bhate, Arizona State University
Dhruv Bhate is an associate professor at Arizona State University. There, he looks at structures, materials, and design. Previously, he worked at PADT as well as in the semiconductor and...
3DPOD 261: Tooling and Cooling for AM with Jason Murphy, NXC MFG
Jason Murphy´s NXC MFG (Next Chapter Manufacturing) is not a generalist service; instead, the company specializes in making tooling. Using LPBF and binder jet, the company produces some of the...
3DPOD 260: John Hart on VulcanForms, MIT, Desktop Metal and More
John Hart is a Professor at MIT; he´s also the director of the Laboratory for Manufacturing and Productivity as well as the director of the Center for Advanced Production Technologies....